Argon welding, while essential in many industrial applications, poses significant safety risks, particularly due to the potential for argon gas displacement of oxygen in confined spaces. To mitigate these risks, several safety precautions are recommended. These include installing oxygen sensors to monitor argon levels and trigger alarms, using harnesses with ropes for worker safety in pits, employing air-blowers to ensure proper ventilation, and providing respirators with a constant fresh air supply for high-risk scenarios. These measures collectively aim to prevent asphyxiation, ensure worker safety, and maintain a safe working environment.
Key Points Explained:
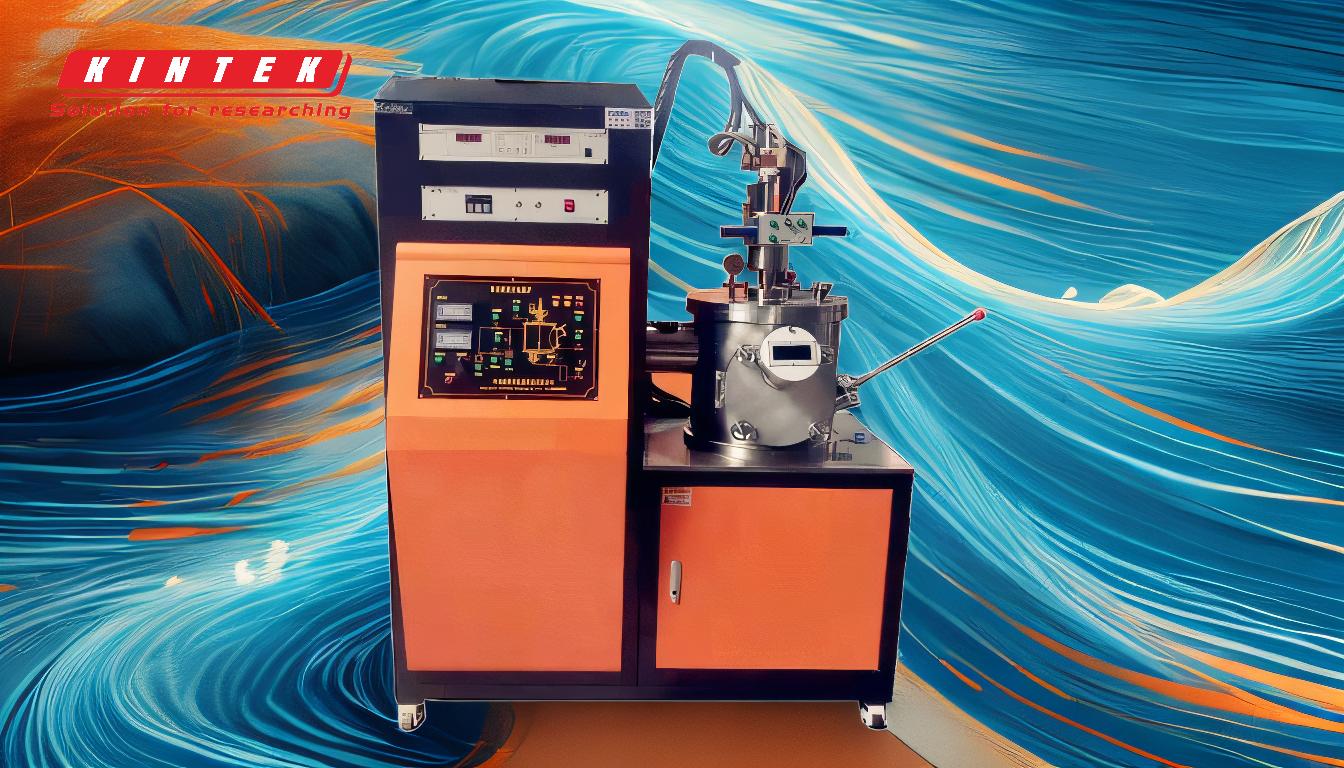
-
Installing Oxygen Sensors in Pits or Low Areas
- Purpose: Argon is heavier than air and can accumulate in low-lying areas, displacing oxygen and creating a hazardous environment. Oxygen sensors are crucial for detecting argon levels and ensuring oxygen concentrations remain safe.
- Implementation: Sensors should be strategically placed in pits, trenches, or other low areas where argon might accumulate. These sensors should be connected to alarms that alert workers when oxygen levels drop below a safe threshold (typically 19.5% oxygen by volume).
- Benefit: Early detection of argon buildup allows for timely evacuation or corrective action, preventing asphyxiation or other health hazards.
-
Using Harnesses with Ropes for Workers in Pits
- Purpose: Confined spaces, such as pits, pose a high risk of entrapment or asphyxiation if argon levels rise unexpectedly. Harnesses with ropes ensure that workers can be quickly rescued if an emergency arises.
- Implementation: Workers entering confined spaces should wear full-body harnesses attached to lifelines. The lifelines should be monitored by trained personnel outside the confined space, ready to initiate a rescue if necessary.
- Benefit: This system provides a reliable method for extracting workers from dangerous situations, reducing the risk of injury or fatality.
-
Using Air-Blowers to Circulate Fresh Air
- Purpose: Proper ventilation is critical in confined spaces to prevent argon accumulation and maintain safe oxygen levels. Air-blowers help circulate fresh air and dilute any argon buildup.
- Implementation: Portable or fixed air-blowers should be used to introduce fresh air into confined spaces. The airflow should be directed to ensure even distribution and effective dilution of argon gas.
- Benefit: Continuous ventilation reduces the likelihood of argon reaching dangerous concentrations, creating a safer environment for workers.
-
Providing Respirators with a Constant Supply of Fresh Air
- Purpose: In high-risk situations where argon levels cannot be adequately controlled, respirators with a constant fresh air supply provide a reliable means of protecting workers.
- Implementation: Workers should be equipped with supplied-air respirators (SARs) or self-contained breathing apparatus (SCBAs) in environments where argon levels are unpredictable or uncontrollable. These devices deliver clean, breathable air directly to the worker.
- Benefit: Respirators ensure that workers have access to safe breathing air, even in the presence of high argon concentrations, significantly reducing the risk of asphyxiation.
By implementing these safety precautions, workplaces can significantly reduce the risks associated with argon welding. These measures not only protect workers from immediate dangers but also contribute to a culture of safety and preparedness in industrial environments.
Summary Table:
Safety Measure | Purpose | Implementation | Benefit |
---|---|---|---|
Installing Oxygen Sensors | Detect argon buildup and ensure safe oxygen levels in low areas. | Place sensors in pits or trenches; connect to alarms for oxygen level monitoring. | Early detection prevents asphyxiation and ensures timely corrective action. |
Using Harnesses with Ropes | Enable quick rescue in confined spaces if argon levels rise unexpectedly. | Workers wear full-body harnesses with lifelines monitored by trained personnel. | Reduces risk of injury or fatality during emergencies. |
Using Air-Blowers | Prevent argon accumulation by circulating fresh air in confined spaces. | Use portable or fixed air-blowers to ensure even airflow and argon dilution. | Maintains safe oxygen levels, reducing argon concentration risks. |
Providing Respirators | Protect workers in high-risk environments with unpredictable argon levels. | Equip workers with SARs or SCBAs for a constant supply of clean, breathable air. | Ensures safe breathing air, even in high argon concentrations. |
Ensure your workplace is safe for argon welding—contact our safety experts today for tailored solutions!