Thermal evaporation is a widely used physical vapor deposition (PVD) technique for creating thin films. It involves heating a material to its evaporation point in a vacuum environment, allowing the vaporized atoms or molecules to travel and condense on a substrate, forming a thin film. The primary sources of thermal evaporation are resistive heating and electron beam heating. Resistive heating uses electrical resistance to generate heat, typically through a refractory metal element like a boat or coil, while electron beam heating employs a focused beam of high-energy electrons to directly heat the target material. Both methods are effective for depositing metals and alloys, with applications in OLEDs, solar cells, and thin-film transistors.
Key Points Explained:
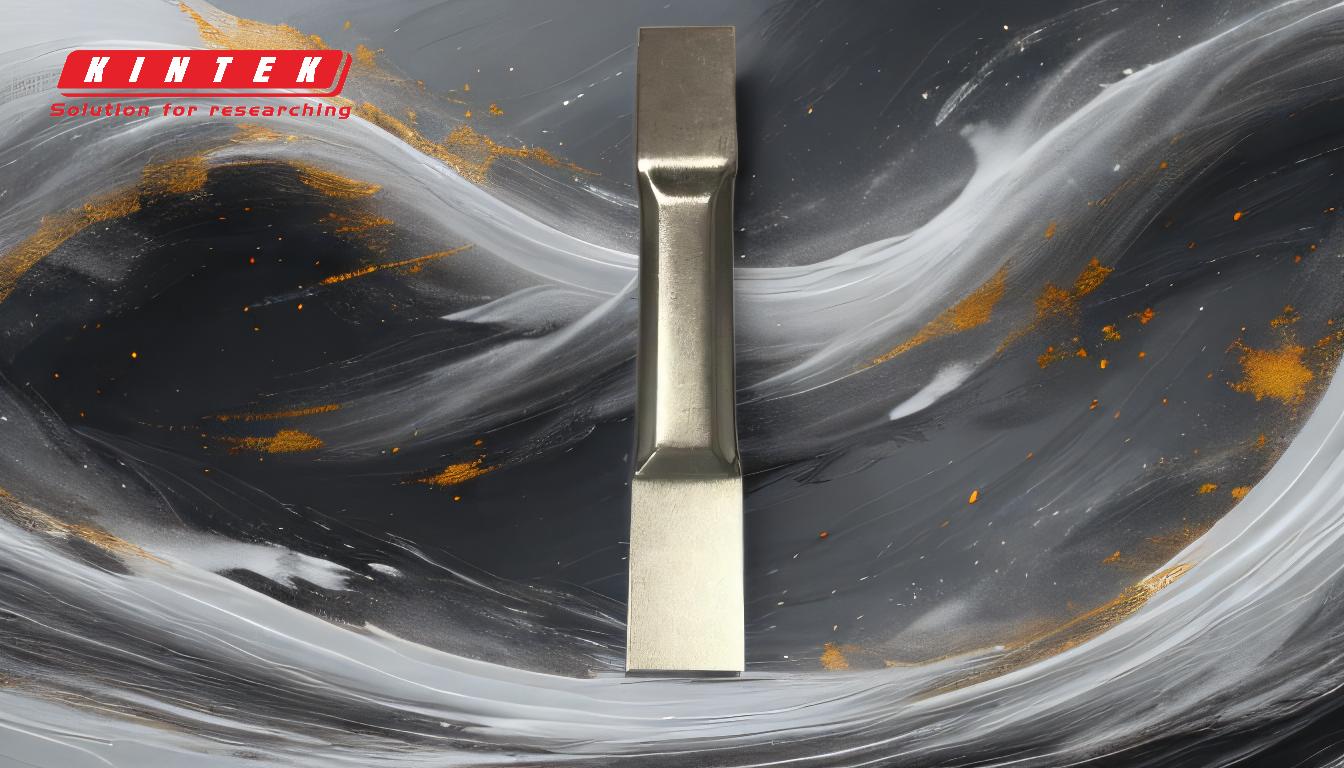
-
Definition and Process of Thermal Evaporation:
- Thermal evaporation is a PVD technique used to deposit thin films by heating a material until it vaporizes in a vacuum environment.
- The vaporized material then condenses onto a substrate, forming a thin film.
- This process is carried out in a high vacuum to minimize contamination and ensure the purity of the deposited film.
-
Primary Sources of Thermal Evaporation:
-
Resistive Heating:
- This method uses electrical resistance to generate heat.
- The target material is placed in a refractory metal element (e.g., a boat, coil, or basket) made of materials like tungsten or molybdenum.
- An electric current is passed through the metal element, heating it to the point where the target material evaporates.
- The evaporated material then travels through the vacuum and deposits onto the substrate.
- This method is also known as resistive evaporation and is commonly used for depositing metals like aluminum and silver.
-
Electron Beam Heating:
- This method uses a focused beam of high-energy electrons to directly heat the target material.
- The electron beam is directed at the material, causing it to vaporize without heating the surrounding crucible or boat.
- This approach is particularly useful for materials with high melting points or those that react with refractory metals.
- Electron beam evaporation allows for precise control over the deposition process and is often used for high-purity applications.
-
-
Components of a Thermal Evaporation System:
- Vacuum Chamber: Typically made of stainless steel to maintain a high vacuum environment.
- Crucible or Boat: Made of refractory materials like tungsten or molybdenum to withstand high temperatures.
- Evaporant: The material to be deposited, such as metals or alloys.
- Substrate: The surface onto which the thin film is deposited.
-
Applications of Thermal Evaporation:
- OLEDs: Used to deposit thin films of metals like aluminum and silver for electrodes.
- Solar Cells: Used to create thin-film layers that improve efficiency.
- Thin-Film Transistors: Essential for depositing conductive layers in electronic devices.
-
Advantages of Thermal Evaporation:
- Simplicity: The process is straightforward and easy to implement.
- Purity: High vacuum conditions ensure minimal contamination, resulting in high-purity films.
- Versatility: Suitable for a wide range of materials, including metals and alloys.
-
Challenges and Considerations:
- Material Compatibility: Some materials may react with the refractory metal elements used in resistive heating.
- Temperature Control: Precise control of heating is required to avoid damaging the substrate or the evaporant.
- Uniformity: Achieving a uniform thin film can be challenging, especially for large substrates.
By understanding these key points, equipment and consumable purchasers can make informed decisions about the thermal evaporation systems and materials that best suit their specific applications.
Summary Table:
Aspect | Details |
---|---|
Definition | A PVD technique for depositing thin films by vaporizing materials in a vacuum. |
Primary Methods | Resistive heating, Electron beam heating. |
Key Components | Vacuum chamber, Crucible/boat, Evaporant, Substrate. |
Applications | OLEDs, Solar cells, Thin-film transistors. |
Advantages | Simplicity, High purity, Versatility. |
Challenges | Material compatibility, Temperature control, Uniformity. |
Ready to enhance your thin film deposition process? Contact us today for expert guidance!