Sputtering is a widely used physical vapor deposition (PVD) technique for growing thin films, particularly in industries like semiconductors, optical devices, and solar panels. The process involves ejecting atoms from a target material onto a substrate using high-energy particle bombardment. The resulting films are known for their uniformity, density, purity, and adhesion. Key parameters influencing the sputtering process include the partial pressure of reactive gases, gas distribution in the chamber, sputtering duration, material mass, and particle energy levels. These factors collectively determine the film's properties, such as thickness, uniformity, and adhesion, making sputtering a versatile and precise method for thin film deposition.
Key Points Explained:
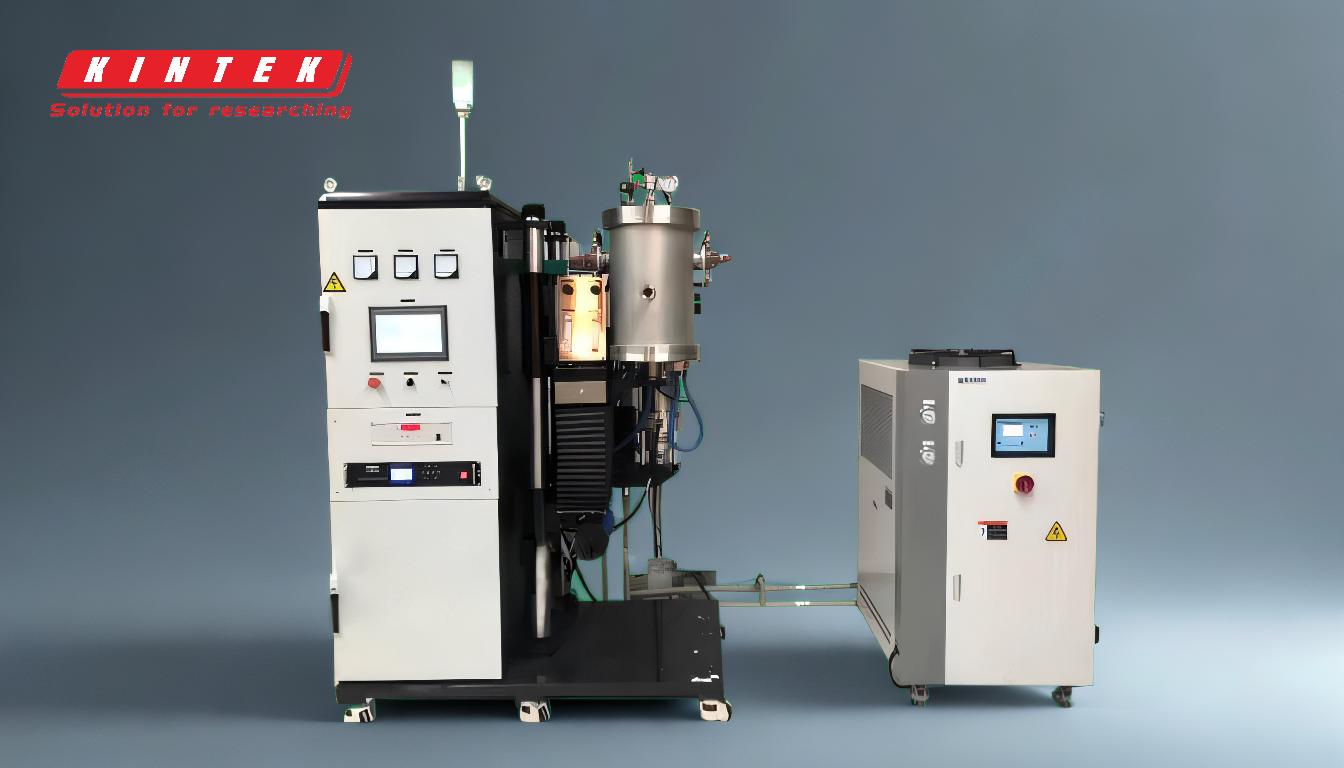
-
Sputtering Process Overview:
- Sputtering is a PVD method where atoms, ions, or molecules are ejected from a target material and deposited onto a substrate.
- This process is widely used in industries like semiconductors, optical devices, and solar panels due to its ability to produce high-quality thin films.
-
Film Properties:
- Sputtered films are known for their excellent uniformity, density, purity, and adhesion.
- These properties make sputtering a preferred method for applications requiring precise and reliable thin films.
-
Influence of Reactive Gases:
- In reactive sputtering, the properties of the film are influenced by the partial pressure of the reactive gas.
- The distribution of the reactive gas in the chamber and the mechanisms used to introduce the gas into the plasma also play crucial roles in determining the film's characteristics.
-
Film Thickness:
- The thickness of the thin film is determined by several factors, including the duration of the sputtering process.
- The mass of the materials involved and the energy level of the coating particles, which can range from tens to thousands of electron volts, also significantly impact the film thickness.
-
Energy Levels:
- The energy level of the coating particles is a critical parameter in sputtering.
- Higher energy levels can lead to more efficient ejection of atoms from the target material, resulting in better film quality and adhesion.
-
Applications:
- Sputtering is used in a variety of applications, including the production of semiconductors, disk drives, CDs, and optical devices.
- The ability to produce films with precise properties makes sputtering essential for advanced technological applications.
By understanding and controlling these sputtering parameters, manufacturers can tailor the properties of thin films to meet specific application requirements, ensuring high performance and reliability in their products.
Summary Table:
Parameter | Description |
---|---|
Reactive Gas Pressure | Influences film properties through partial pressure and gas distribution. |
Sputtering Duration | Determines film thickness and uniformity. |
Material Mass | Affects the rate and quality of atom ejection from the target. |
Particle Energy Levels | Higher energy levels improve film adhesion and quality (tens to thousands of eV). |
Applications | Semiconductors, optical devices, solar panels, and more. |
Need help optimizing your sputtering process? Contact our experts today for tailored solutions!