Graphite furnace processing involves heating carbonaceous materials to extremely high temperatures in a controlled environment to achieve graphitization. The process is divided into several stages, each critical to transforming raw materials into high-quality graphite. Key stages include material preparation, heating, graphitization, cooling, and post-processing. Each stage requires precise control of temperature, atmosphere, and time to ensure optimal results. Below, the stages are explained in detail, focusing on their purpose, requirements, and significance in the overall process.
Key Points Explained:
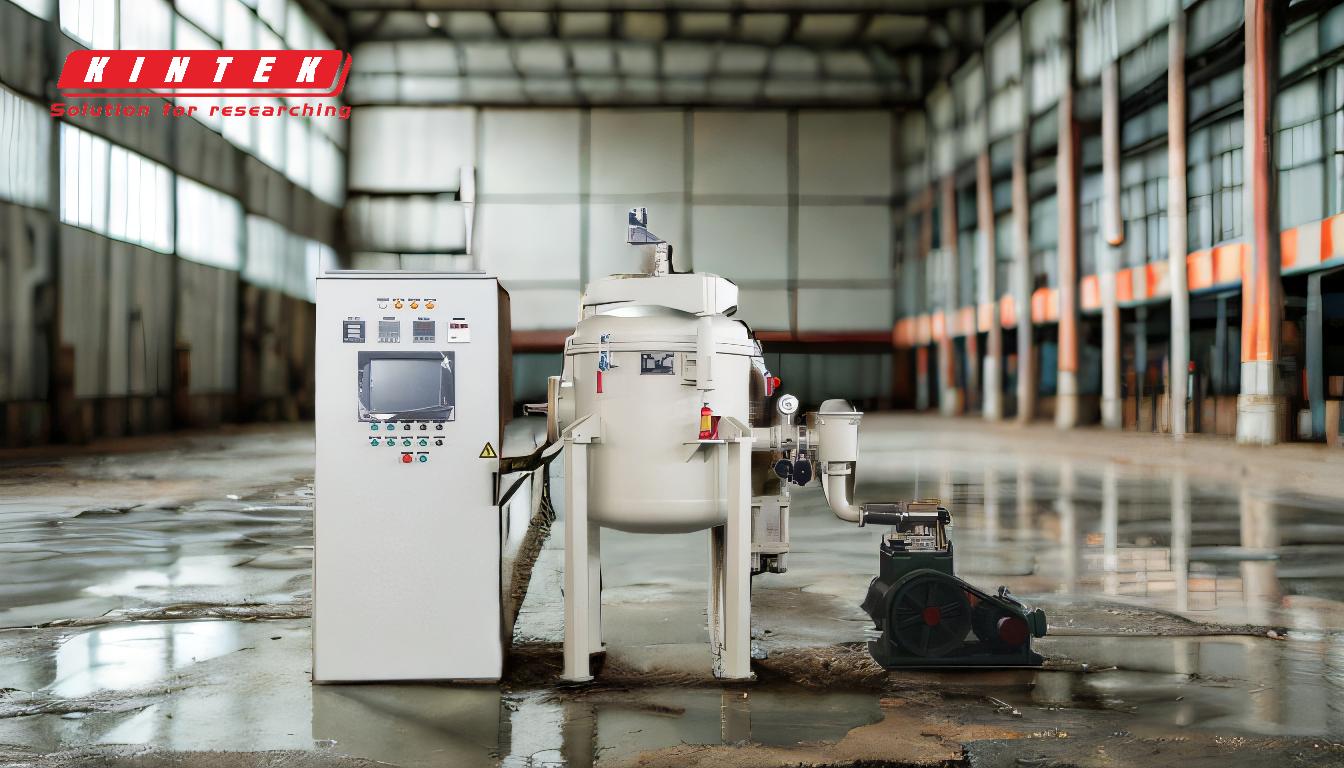
-
Material Preparation
- Purpose: Prepare raw carbonaceous materials for the graphitization process.
- Process: Raw materials, such as petroleum coke or coal tar pitch, are purified, mixed, and shaped into the desired form (e.g., blocks, rods, or fibers).
- Significance: Proper preparation ensures uniformity and reduces impurities, which can affect the quality of the final graphite product.
-
Heating Stage
- Purpose: Gradually increase the temperature to initiate the transformation of carbonaceous materials.
- Process: The furnace temperature is raised to intermediate levels (typically between 500°C and 1500°C) to remove volatile components and begin carbonization.
- Significance: This stage ensures the removal of non-carbon elements and prepares the material for the high-temperature graphitization phase.
-
Graphitization
- Purpose: Convert carbonized materials into graphite by reorganizing their atomic structure.
- Process: The temperature is increased to above 2500°C in an inert atmosphere (e.g., argon or nitrogen) to prevent oxidation. This high-temperature treatment aligns the carbon atoms into a crystalline graphite structure.
- Significance: This is the most critical stage, as it determines the final properties of the graphite, such as electrical conductivity, thermal resistance, and mechanical strength.
-
Cooling Stage
- Purpose: Gradually reduce the temperature to stabilize the graphite structure.
- Process: The furnace is cooled slowly to room temperature to prevent thermal shock, which could cause cracking or other defects.
- Significance: Controlled cooling ensures the integrity and durability of the graphite product.
-
Post-Processing
- Purpose: Finalize the graphite product for specific applications.
- Process: This may include machining, surface treatment, or coating to achieve desired dimensions, surface finish, or functional properties.
- Significance: Post-processing tailors the graphite to meet the requirements of its intended use, such as in electrodes, crucibles, or thermal management systems.
By understanding these stages, equipment and consumable purchasers can better evaluate the quality and suitability of graphite products for their specific applications. Each stage plays a vital role in determining the final properties and performance of the graphite, making it essential to ensure that the process is carried out with precision and care.
Summary Table:
Stage | Purpose | Process | Significance |
---|---|---|---|
Material Preparation | Prepare raw carbonaceous materials for graphitization. | Purify, mix, and shape materials (e.g., blocks, rods). | Ensures uniformity and reduces impurities for high-quality graphite. |
Heating Stage | Initiate transformation of carbonaceous materials. | Raise temperature to 500°C–1500°C to remove volatile components. | Prepares material for high-temperature graphitization. |
Graphitization | Convert carbonized materials into graphite. | Heat above 2500°C in inert atmosphere to align carbon atoms. | Determines final properties like conductivity, thermal resistance, and strength. |
Cooling Stage | Stabilize the graphite structure. | Cool slowly to room temperature to prevent thermal shock. | Ensures durability and integrity of the graphite product. |
Post-Processing | Finalize graphite for specific applications. | Machining, surface treatment, or coating for desired properties. | Tailors graphite for use in electrodes, crucibles, or thermal systems. |
Need high-quality graphite products? Contact our experts today to learn more about our advanced graphite furnace processing solutions!