The injection moulding process is a manufacturing technique used to produce parts by injecting molten material into a mould. The process typically lasts between 2 seconds to 2 minutes and consists of four main stages: clamping, injection, cooling, and ejection. Each stage plays a critical role in ensuring the final product meets the desired specifications. Understanding these stages is essential for optimizing the moulding process, reducing defects, and improving efficiency.
Key Points Explained:
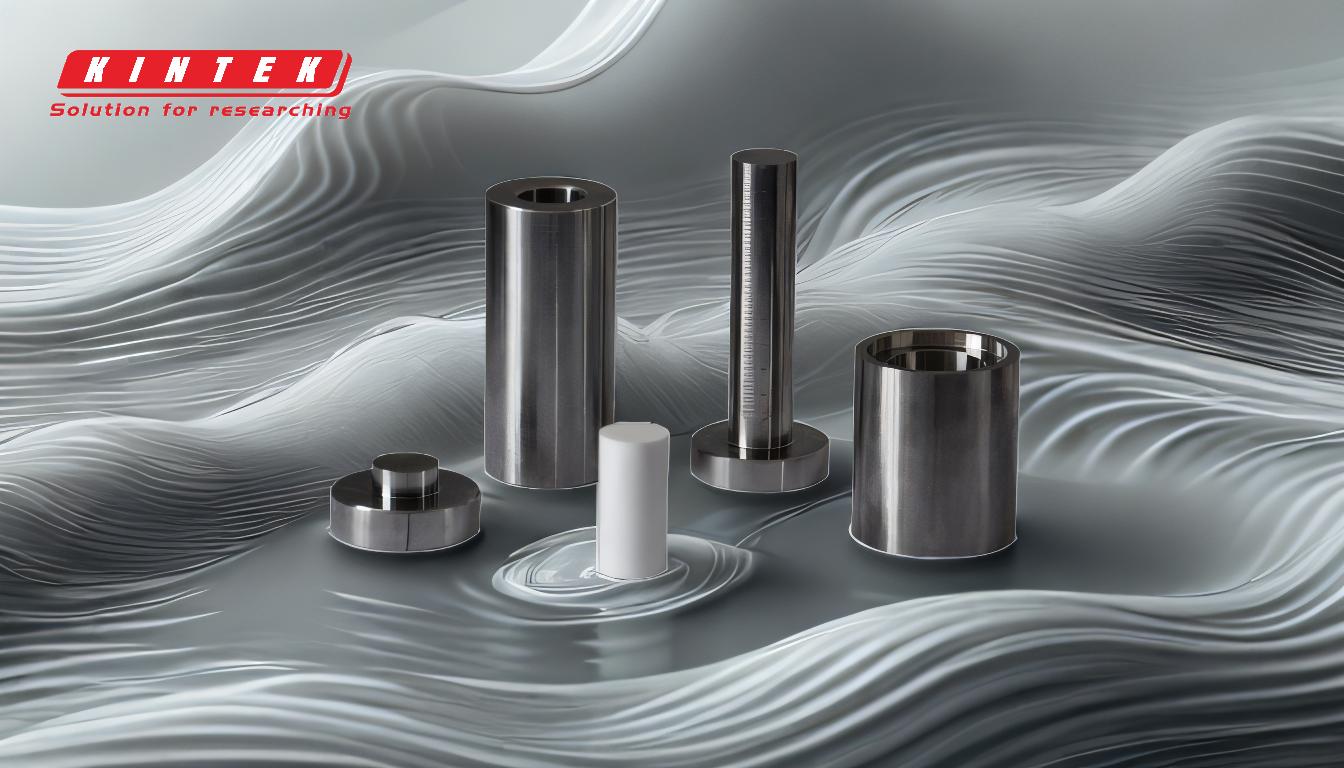
-
Clamping Stage:
- Purpose: The clamping stage is the first step in the injection moulding process. Its primary purpose is to securely close the two halves of the mould to prepare for the injection of molten material.
- Process: The mould is mounted on the injection moulding machine, and the clamping unit holds the mould halves together with sufficient force to withstand the pressure of the injected material. The clamping force required depends on the size and complexity of the part being produced.
- Importance: Proper clamping ensures that the mould remains closed during the injection and cooling phases, preventing defects such as flash (excess material that escapes from the mould cavity).
-
Injection Stage:
- Purpose: The injection stage involves the introduction of molten material into the mould cavity. This stage is critical for shaping the final product.
- Process: The material, typically in the form of pellets, is fed into the injection moulding machine's barrel, where it is heated until it reaches a molten state. The molten material is then injected into the mould cavity under high pressure. The injection speed, pressure, and temperature are carefully controlled to ensure the material fills the mould completely and uniformly.
- Importance: The injection stage determines the quality of the part's surface finish, dimensional accuracy, and structural integrity. Inadequate injection can lead to defects such as short shots (incomplete filling of the mould) or sink marks (depressions on the surface).
-
Cooling Stage:
- Purpose: The cooling stage allows the molten material to solidify within the mould, taking on the shape of the mould cavity.
- Process: After the mould cavity is filled, the material begins to cool and solidify. Cooling time varies depending on the material used, the thickness of the part, and the mould design. Cooling is typically facilitated by cooling channels within the mould that circulate water or other cooling media.
- Importance: Proper cooling is essential to ensure the part maintains its shape and dimensional stability. Insufficient cooling can result in warping, shrinkage, or internal stresses within the part.
-
Ejection Stage:
- Purpose: The ejection stage involves removing the solidified part from the mould.
- Process: Once the material has sufficiently cooled and solidified, the mould opens, and ejector pins or plates push the part out of the mould cavity. The part is then collected, and the mould closes again to prepare for the next cycle.
- Importance: The ejection stage must be carefully managed to avoid damaging the part or the mould. Proper ejection ensures that the part is released smoothly and without defects such as scratches or deformation.
Summary:
The injection moulding process is a highly efficient method for producing parts with complex geometries and high precision. The four stages—clamping, injection, cooling, and ejection—are integral to the success of the process. Each stage must be carefully controlled to ensure the production of high-quality parts. Understanding these stages allows manufacturers to optimize the moulding process, reduce defects, and improve overall efficiency.
Summary Table:
Stage | Purpose | Key Details |
---|---|---|
Clamping | Securely close the mould to prepare for injection. | Ensures mould remains closed under pressure, preventing defects like flash. |
Injection | Introduce molten material into the mould cavity. | Controls speed, pressure, and temperature to ensure complete and uniform filling. |
Cooling | Solidify the material within the mould. | Uses cooling channels to prevent warping, shrinkage, or internal stresses. |
Ejection | Remove the solidified part from the mould. | Ejector pins or plates release the part smoothly, avoiding scratches or deformation. |
Ready to optimize your injection moulding process? Contact our experts today for tailored solutions!