Physical Vapor Deposition (PVD) is a widely used vacuum deposition technique for creating thin, high-quality coatings on various substrates. The process involves transforming a solid material into a vapor phase and then condensing it back into a solid film on a substrate. The primary methods of PVD include sputtering and evaporation, which are carried out in a vacuum chamber. The process is environmentally friendly and allows for the deposition of a wide range of materials, including inorganic and some organic materials. The PVD process typically consists of four main steps: evaporation, transportation, reaction, and deposition. Each step plays a critical role in ensuring the quality and properties of the final coating.
Key Points Explained:
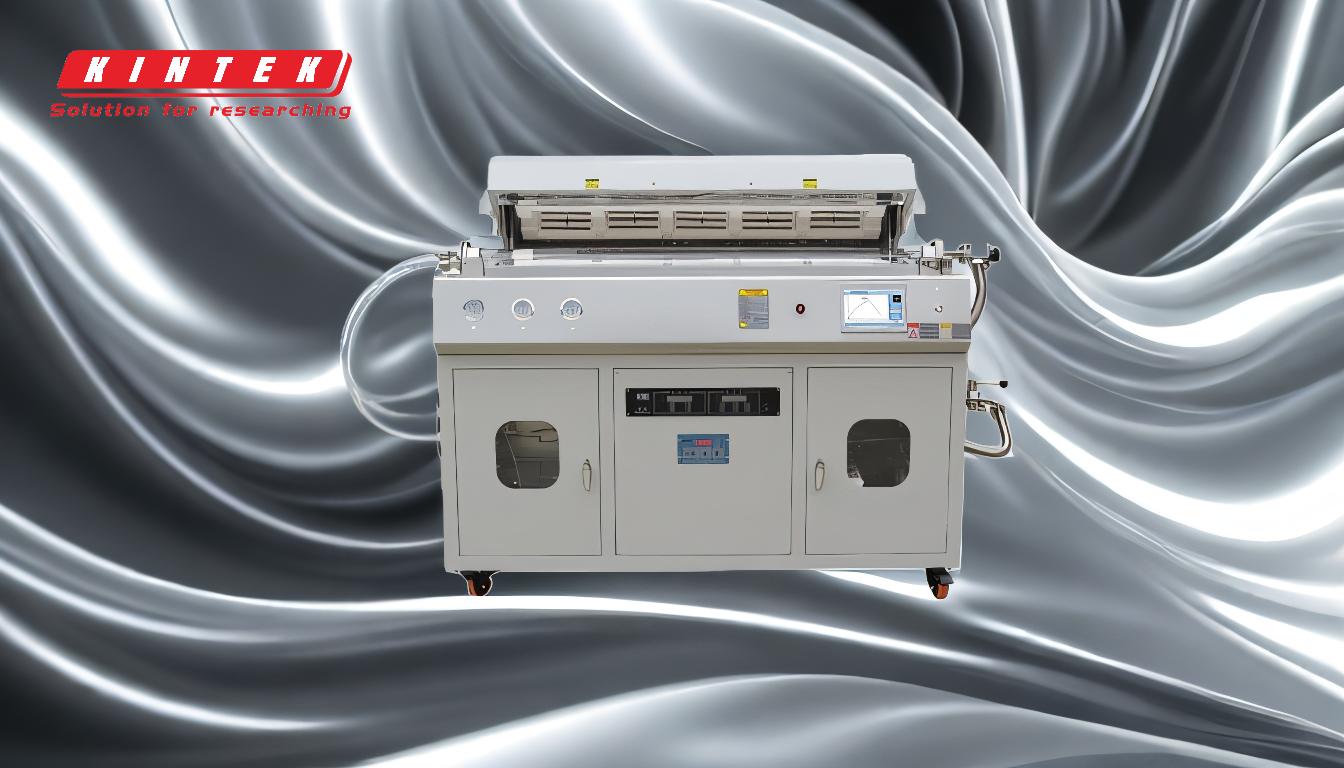
-
Evaporation:
- In this step, the target material is bombarded by a high-energy source, such as an ion beam, laser, or thermal energy, to dislodge atoms from the target. This process converts the solid target material into a vapor phase.
- The high-energy source can vary depending on the specific PVD method used. For example, in sputtering, a plasma discharge is used to bombard the target, while in thermal evaporation, the target is heated until it vaporizes.
- The goal is to create a vapor of the target material that can be transported to the substrate.
-
Transportation:
- Once the target material is vaporized, the atoms or molecules move through the vacuum chamber toward the substrate. The vacuum environment ensures that the vaporized particles travel without interference from air molecules, which could otherwise contaminate the coating.
- The transportation step is crucial for maintaining the purity and uniformity of the coating. Any contamination during this phase can lead to defects in the final film.
-
Reaction:
- During this step, the vaporized atoms may react with gases introduced into the vacuum chamber, such as oxygen or nitrogen, to form compound coatings like oxides, nitrides, or carbides. This step is optional and depends on the desired properties of the coating.
- For example, if a titanium nitride (TiN) coating is desired, nitrogen gas is introduced into the chamber, and the titanium atoms react with the nitrogen to form TiN.
- The reaction step allows for the creation of coatings with specific chemical and mechanical properties, such as increased hardness or corrosion resistance.
-
Deposition:
- In the final step, the vaporized atoms or molecules condense on the substrate surface, forming a thin, uniform coating. The substrate is typically positioned in such a way that it receives an even distribution of the vaporized material.
- The deposition process is carefully controlled to ensure that the coating adheres well to the substrate and has the desired thickness and properties. The quality of the deposition is influenced by factors such as the substrate temperature, the rate of deposition, and the vacuum conditions.
- The result is a high-quality, durable coating that can enhance the substrate's properties, such as wear resistance, electrical conductivity, or optical performance.
By following these four steps—evaporation, transportation, reaction, and deposition—the PVD process enables the creation of advanced coatings with precise control over their composition, thickness, and properties. This makes PVD a valuable technique in industries ranging from electronics and optics to aerospace and medical devices.
Summary Table:
Step | Description |
---|---|
Evaporation | Target material is vaporized using high-energy sources like ion beams or lasers. |
Transportation | Vaporized atoms move through a vacuum chamber to the substrate without contamination. |
Reaction | Atoms may react with gases to form compound coatings (optional step). |
Deposition | Vapor condenses on the substrate, forming a thin, uniform coating. |
Ready to enhance your materials with PVD coatings? Contact our experts today to get started!