Chemical vapor deposition (CVD) is a sophisticated process used to create thin films and coatings on substrates through chemical reactions in a controlled environment. The process involves several sequential steps, including the transport of gaseous reactants to the reaction zone, adsorption on the substrate surface, surface diffusion, chemical reactions, and desorption of by-products. These steps ensure the formation of a uniform and high-quality thin film. Below, the key steps are explained in detail to provide a comprehensive understanding of the CVD process.
Key Points Explained:
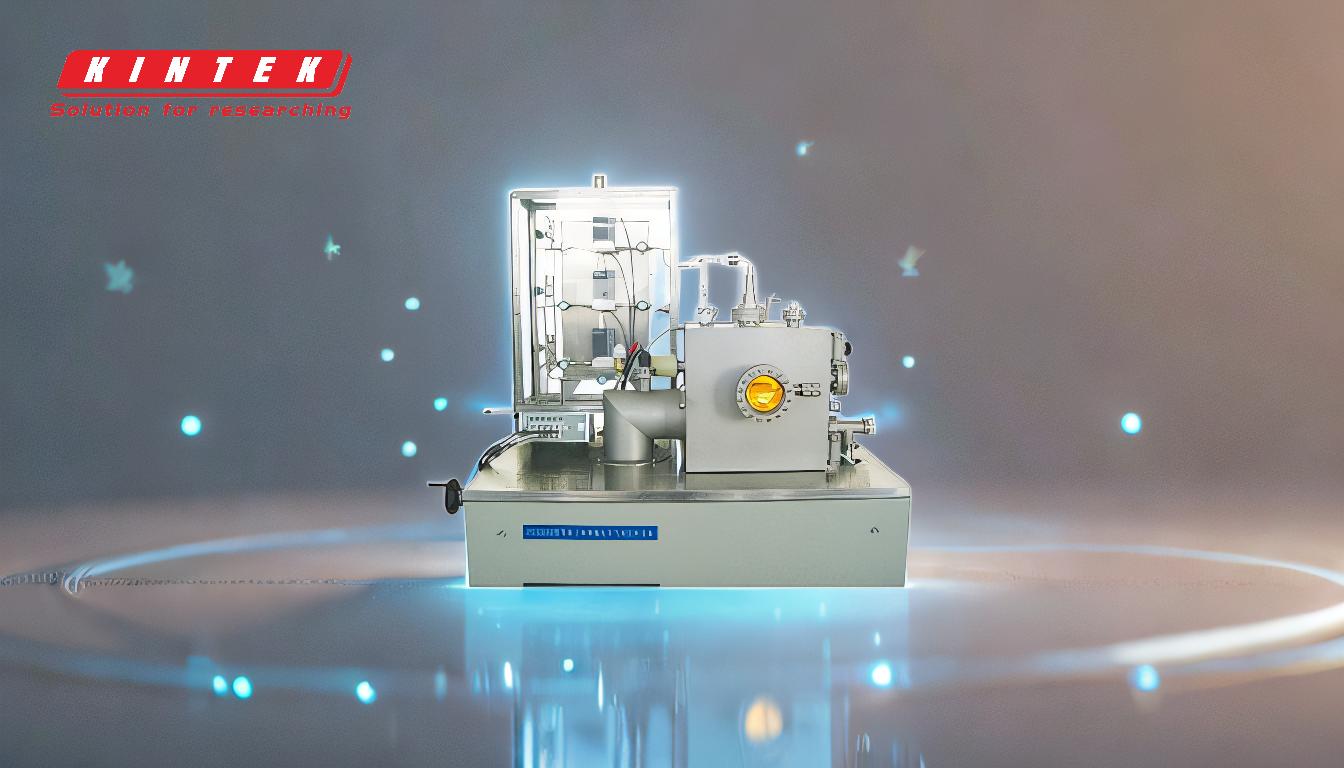
-
Transport of Reactants to the Reaction Zone
- The first step involves introducing precursor chemicals (e.g., TiCl4, BCl3, H2) into the CVD reactor, often carried by an inert gas like argon or nitrogen.
- These gaseous reactants are transported to the reaction zone through convection or diffusion.
- The reactants must move through a boundary layer near the substrate surface, which is critical for ensuring uniform deposition.
-
Adsorption of Precursors on the Substrate Surface
- Once the reactants reach the substrate, they adsorb onto its surface.
- Adsorption is a physical or chemical process where the precursor molecules adhere to the substrate, forming a thin layer.
- This step is influenced by factors such as temperature, pressure, and the nature of the substrate.
-
Surface Diffusion to Growth Sites
- After adsorption, the precursor molecules diffuse across the substrate surface to reach active growth sites.
- Surface diffusion is essential for ensuring uniform film growth and minimizing defects.
- The mobility of the molecules on the surface depends on the substrate's temperature and the energy of the adsorbed species.
-
Heterogeneous Surface Reactions
- At the growth sites, chemical reactions occur between the adsorbed precursors, leading to the formation of a solid film.
- These reactions are often catalyzed by the substrate surface and may involve decomposition, reduction, or oxidation of the precursors.
- The reactions produce the desired thin film and volatile by-products.
-
Desorption of By-products
- The by-products of the surface reactions must be desorbed from the substrate to prevent contamination and allow further deposition.
- Desorption involves the release of volatile by-products into the gas phase, which then diffuse through the boundary layer and are transported out of the reactor.
-
Removal of Gaseous By-products
- The final step involves removing the gaseous by-products from the reactor through convection and diffusion processes.
- Efficient removal of by-products is crucial for maintaining the purity of the deposition environment and ensuring consistent film quality.
-
Environmental and Economic Considerations
- CVD is a highly controllable and environmentally friendly process, as it typically uses non-toxic precursors and produces minimal waste.
- However, the process can be time-consuming and costly due to the need for sophisticated equipment and precise control of reaction conditions.
- These factors make CVD more suitable for high-value applications rather than large-scale production.
By following these sequential steps, the CVD process achieves the deposition of high-quality thin films with precise control over thickness, composition, and uniformity. This makes it a valuable technique in industries such as semiconductors, optics, and energy storage.
Summary Table:
Step | Description |
---|---|
Transport of Reactants | Precursor chemicals are introduced into the reactor and transported to the reaction zone. |
Adsorption on Substrate | Reactants adsorb onto the substrate surface, forming a thin layer. |
Surface Diffusion | Precursor molecules diffuse across the substrate to active growth sites. |
Heterogeneous Reactions | Chemical reactions at growth sites form the solid film and volatile by-products. |
Desorption of By-products | By-products desorb from the substrate to prevent contamination. |
Removal of Gaseous By-products | Gaseous by-products are removed from the reactor for consistent film quality. |
Environmental Considerations | CVD is eco-friendly but costly, ideal for high-value applications. |
Discover how CVD can enhance your thin film processes—contact our experts today!