Case hardening is a heat treatment process used to increase the hardness of the outer surface of a metal while maintaining a softer, more ductile core. This process serves two primary purposes: enhancing wear resistance and improving fatigue strength. By creating a hard outer layer, the material becomes more resistant to abrasion and surface wear, which is crucial for components subjected to friction or impact. Simultaneously, the softer core ensures that the part retains its toughness and ability to absorb stress, preventing catastrophic failure under cyclic loading. This combination of surface hardness and core toughness makes case hardening particularly valuable in applications like gears, bearings, and other mechanical components.
Key Points Explained:
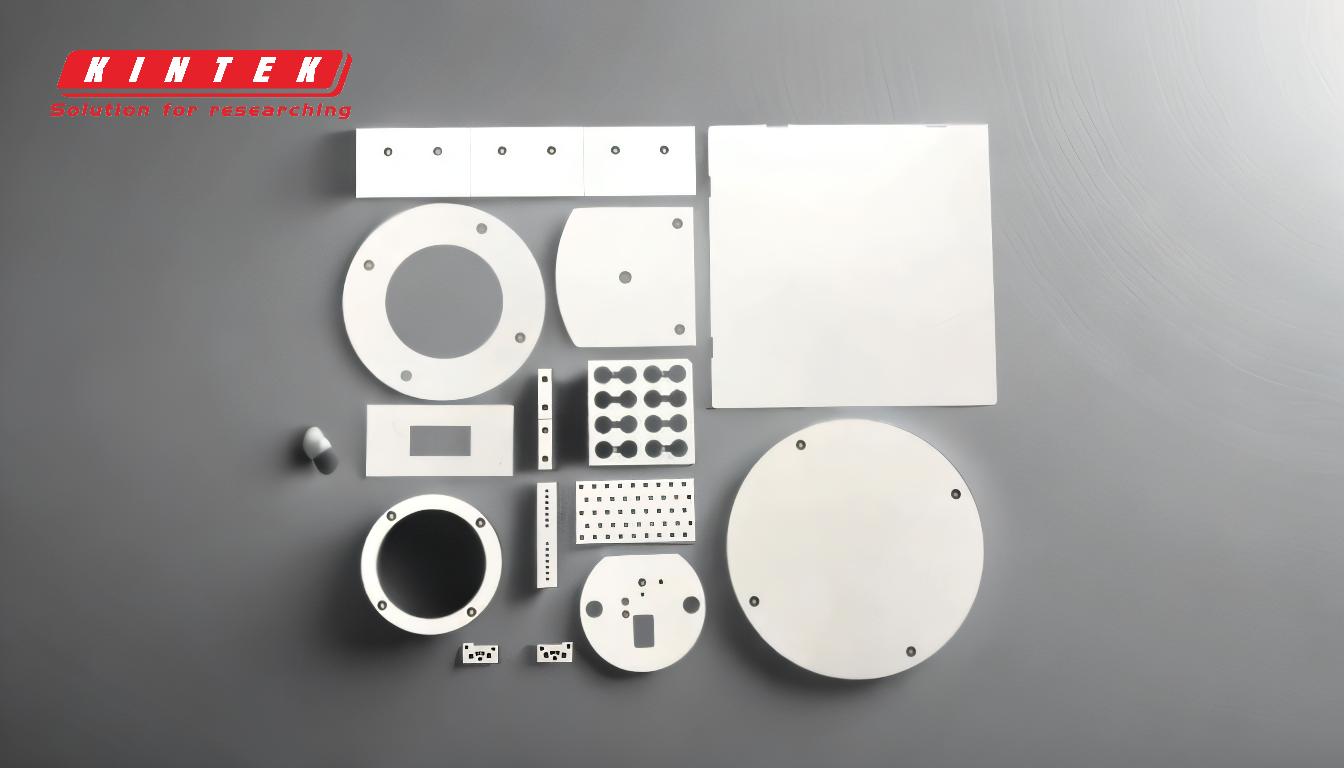
-
Enhancing Wear Resistance
- Case hardening significantly increases the hardness of the outer surface of a metal, making it more resistant to wear and abrasion.
- This is achieved by introducing carbon or nitrogen into the surface layer through processes like carburizing, nitriding, or carbonitriding.
- The hardened surface can withstand friction, impact, and other forms of mechanical wear, extending the lifespan of the component.
- This is particularly important for parts like gears, cams, and bearings, which are constantly exposed to high levels of friction and stress.
-
Improving Fatigue Strength
- Fatigue strength refers to a material's ability to withstand cyclic or repeated loading without failing.
- The hard outer layer created by case hardening resists surface cracks and deformations, while the softer core absorbs stress and prevents crack propagation.
- This dual-layer structure ensures that the component can endure repeated stress cycles without fracturing, making it ideal for applications like crankshafts, axles, and other rotating parts.
- The combination of surface hardness and core toughness is critical for maintaining structural integrity under dynamic loading conditions.
-
Applications of Case Hardening
- Case hardening is widely used in industries where components are exposed to high wear and stress.
- Common applications include automotive parts (e.g., gears, shafts, and camshafts), industrial machinery, and tools.
- The process is also employed in the manufacturing of cutting tools, where a hard surface is essential for maintaining sharpness and durability.
-
Advantages Over Other Heat Treatment Methods
- Unlike through-hardening, which hardens the entire component, case hardening selectively hardens only the surface, preserving the core's toughness.
- This makes it more suitable for parts that require both surface hardness and internal ductility.
- Additionally, case hardening can be applied to low-carbon steels, which are otherwise difficult to harden through conventional methods.
-
Processes Involved in Case Hardening
- Carburizing: Introduces carbon into the surface layer by heating the metal in a carbon-rich environment.
- Nitriding: Uses nitrogen to harden the surface, often at lower temperatures, reducing distortion.
- Carbonitriding: Combines carbon and nitrogen for enhanced surface properties.
- Induction Hardening: Uses electromagnetic induction to heat and harden specific areas of the component.
By achieving a balance between surface hardness and core toughness, case hardening ensures that components can withstand both wear and fatigue, making it an indispensable process in modern manufacturing.
Summary Table:
Purpose | Description |
---|---|
Wear Resistance | Increases surface hardness to resist abrasion, friction, and mechanical wear. |
Fatigue Strength | Combines a hard outer layer with a tough core to withstand cyclic loading. |
Learn how case hardening can optimize your components—contact our experts today!