Induction furnaces are widely used in metallurgy for melting metals due to their efficiency, precision, and versatility. The two primary types of induction furnaces are core-type (channel) induction furnaces and coreless-type induction furnaces. Each type serves distinct purposes based on their design and operational characteristics. Core-type furnaces are ideal for continuous melting of low-melting-point alloys or holding molten metals, while coreless-type furnaces are more versatile and suitable for melting a wide range of metals, including steel, copper, and aluminum. Modern advancements, such as IGBT induction furnaces, have further enhanced their efficiency and control.
Key Points Explained:
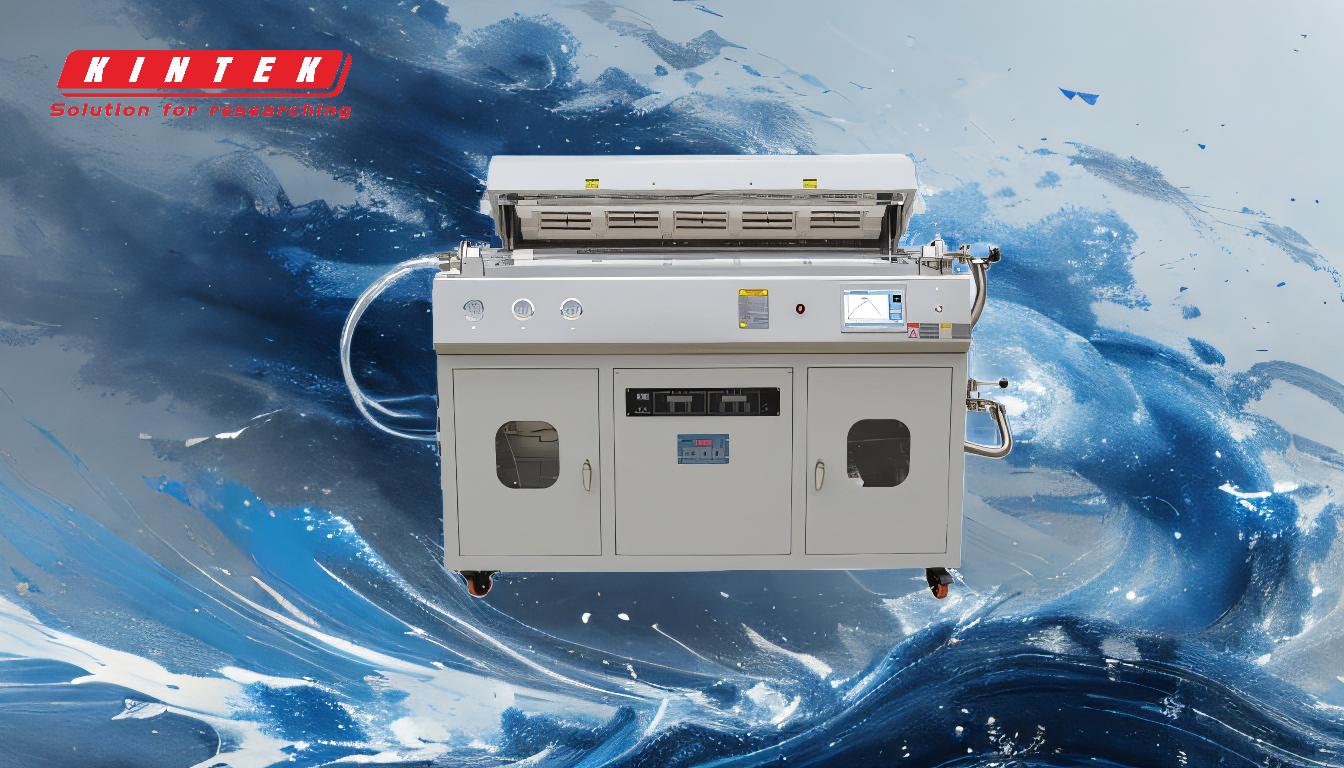
-
Core-Type (Channel) Induction Furnace:
- Design and Function: This furnace features a channel-like structure with a core made of magnetic material, surrounded by an induction coil. The molten metal flows through the channel, where it is heated by electromagnetic induction.
- Applications: Primarily used for melting low-melting-point alloys like zinc, lead, and aluminum. It is also employed as a holding and superheating unit for higher-melting-point alloys such as cast iron.
-
Advantages:
- Efficient for continuous melting processes.
- Low energy consumption for maintaining molten metal.
- Suitable for applications requiring consistent temperature control.
- Limitations: Less versatile compared to coreless furnaces, as it is not ideal for melting high-melting-point metals like steel.
-
Coreless-Type Induction Furnace:
- Design and Function: This furnace lacks a core and consists of a crucible surrounded by an induction coil. The alternating magnetic field generated by the coil induces eddy currents in the metal charge, causing it to melt.
- Applications: Widely used for melting a variety of metals, including steel, copper, aluminum, and precious metals. It is also suitable for alloying and refining processes.
-
Advantages:
- High versatility for melting different metals.
- Rapid heating and melting due to direct induction heating.
- Precise temperature control, making it ideal for high-quality metal production.
- Limitations: Higher energy consumption compared to core-type furnaces, especially for holding molten metal over extended periods.
-
Modern Advancements in Induction Furnaces:
-
IGBT Induction Furnaces: The integration of Insulated Gate Bipolar Transistor (IGBT) technology has revolutionized induction furnaces. These furnaces offer:
- Enhanced power efficiency and control.
- Reduced harmonics and improved power factor.
- Compact design and lightweight construction.
- Applications: IGBT induction furnaces are particularly suitable for steelmaking and other high-temperature melting processes due to their ability to handle medium-frequency power supplies efficiently.
-
IGBT Induction Furnaces: The integration of Insulated Gate Bipolar Transistor (IGBT) technology has revolutionized induction furnaces. These furnaces offer:
-
Operational Features of Induction Furnaces:
- Inductor Coil: Made of copper, the coil generates an alternating magnetic flux that heats the metal charge.
- Crucible Lining: The crucible is lined with acid or basic materials depending on the metal being melted, ensuring durability and preventing contamination.
- Hydraulic Tilting Mechanism: Modern furnaces use hydraulic plungers to regulate the furnace's inclination, facilitating easy pouring of molten metal.
-
Comparison of Core-Type and Coreless-Type Furnaces:
- Energy Efficiency: Core-type furnaces are more energy-efficient for holding molten metal, while coreless-type furnaces excel in rapid melting.
- Versatility: Coreless furnaces are more adaptable to a wide range of metals and alloys.
- Maintenance: Core-type furnaces require less maintenance due to their simpler design, whereas coreless furnaces may need more frequent crucible replacements.
By understanding the distinct characteristics and applications of core-type and coreless-type induction furnaces, as well as the advancements brought by IGBT induction furnaces, purchasers can make informed decisions based on their specific melting requirements.
Summary Table:
Feature | Core-Type Induction Furnace | Coreless-Type Induction Furnace |
---|---|---|
Design | Channel-like structure with a core | No core; crucible surrounded by coil |
Applications | Low-melting-point alloys, holding metal | Wide range of metals, alloying |
Advantages | Energy-efficient, continuous melting | Versatile, rapid heating, precise |
Limitations | Less versatile for high-melting metals | Higher energy consumption |
Maintenance | Low maintenance | Frequent crucible replacements |
Need help choosing the right induction furnace for your needs? Contact our experts today!