Coating methods for metal cutting tools are essential for enhancing their performance, durability, and efficiency. The two most widely used techniques are Physical Vapor Deposition (PVD) and Chemical Vapor Deposition (CVD). PVD coatings, such as titanium nitride (TiN), are applied to tools like drill bits to improve hardness and wear resistance. PVD processes include evaporating, sputtering, and reactive ion plating, each offering unique advantages. These methods significantly extend tool life and improve cutting performance, making them indispensable in modern machining and manufacturing industries.
Key Points Explained:
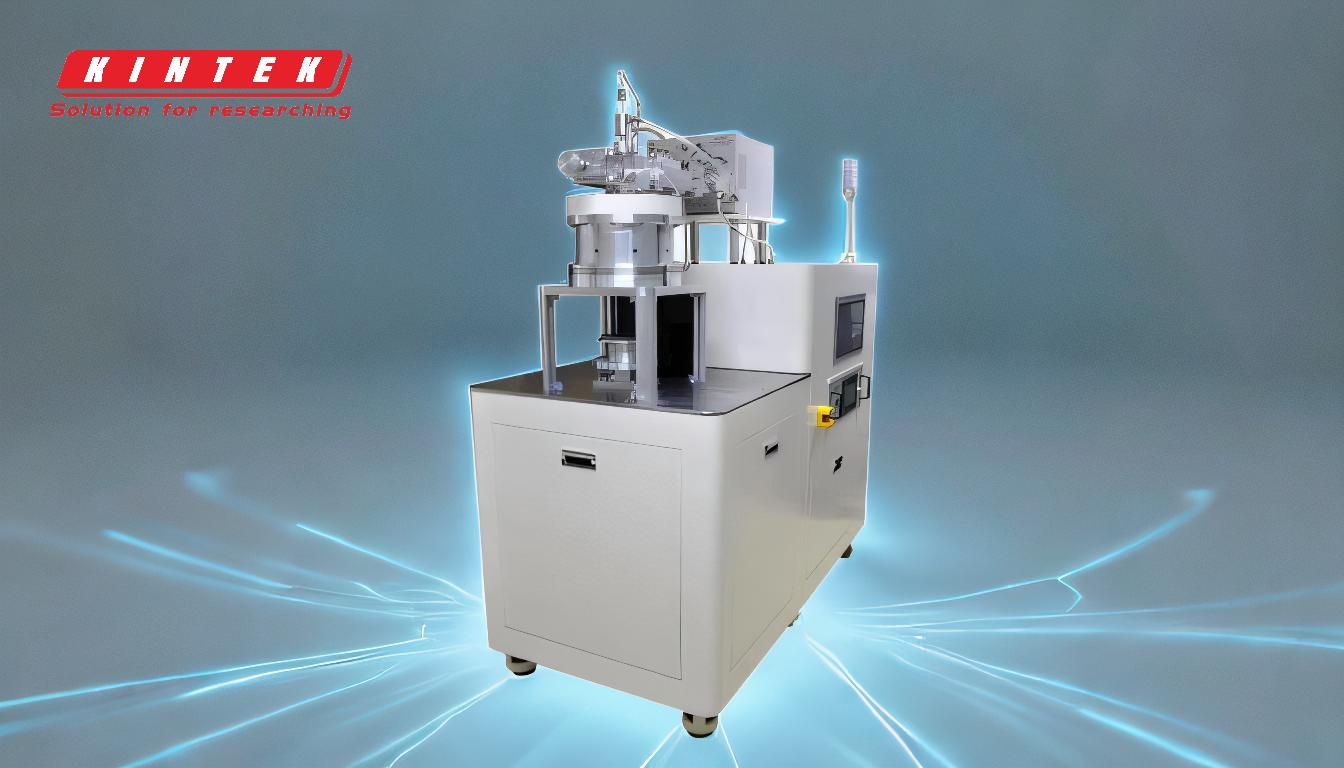
-
Physical Vapor Deposition (PVD):
- PVD is a widely used coating method for metal cutting tools due to its ability to enhance hardness, durability, and wear resistance.
- Common PVD coatings include titanium nitride (TiN), which is significantly harder than the base material of the tool, such as steel. This allows the tool to maintain sharpness and perform efficiently over extended periods.
- PVD processes involve three major techniques:
- Evaporating: In this process, the coating material is heated until it evaporates and then condenses onto the tool surface, forming a thin, uniform layer.
- Sputtering: This technique involves bombarding the coating material with ions, causing atoms to be ejected and deposited onto the tool surface.
- Reactive Ion Plating: Here, a reactive gas is introduced during the deposition process, creating a chemical reaction that forms a hard, durable coating on the tool.
-
Chemical Vapor Deposition (CVD):
- CVD is another prominent coating method used for metal cutting tools, particularly in high-temperature applications.
- This process involves introducing a chemical vapor into a chamber where it reacts with the tool surface, forming a solid coating layer.
- CVD coatings are known for their excellent adhesion, uniformity, and ability to withstand extreme temperatures, making them suitable for demanding machining operations.
-
Benefits of Coating Methods:
- Both PVD and CVD coatings significantly improve the performance and lifespan of cutting tools by:
- Increasing hardness and wear resistance.
- Reducing friction and heat generation during cutting operations.
- Enhancing corrosion resistance, which is particularly important in harsh machining environments.
- These benefits lead to reduced tool replacement costs, improved machining efficiency, and better overall productivity.
- Both PVD and CVD coatings significantly improve the performance and lifespan of cutting tools by:
-
Applications of Coated Tools:
- Coated cutting tools are used in various industries, including automotive, aerospace, and manufacturing, where precision and durability are critical.
- Specific applications include drilling, milling, turning, and threading, where the enhanced properties of coated tools ensure consistent performance and extended tool life.
By understanding the principles and advantages of PVD and CVD coating methods, purchasers can make informed decisions when selecting cutting tools for specific applications, ensuring optimal performance and cost-effectiveness.
Summary Table:
Coating Method | Key Features | Applications |
---|---|---|
PVD (Physical Vapor Deposition) | - Enhances hardness, wear resistance, and durability. - Common coatings: Titanium Nitride (TiN). - Processes: Evaporating, Sputtering, Reactive Ion Plating. |
- Drilling, milling, turning. - Automotive, aerospace, manufacturing. |
CVD (Chemical Vapor Deposition) | - Excellent adhesion and uniformity. - Withstands extreme temperatures. - Ideal for high-temperature applications. |
- Precision machining. - Harsh environments requiring corrosion resistance. |
Ready to enhance your cutting tools' performance? Contact us today to find the perfect coating solution!