The strength of ceramics is determined by a combination of factors, including their microstructure, composition, processing techniques, and the presence of defects. Fine ceramics, in particular, exhibit high strength due to their refined grain structure, controlled porosity, and advanced manufacturing processes. These materials are engineered to minimize flaws and optimize properties such as hardness, toughness, and thermal stability. Understanding these factors is crucial for selecting ceramics for specific applications, as their performance often depends on achieving a balance between strength and other material properties.
Key Points Explained:
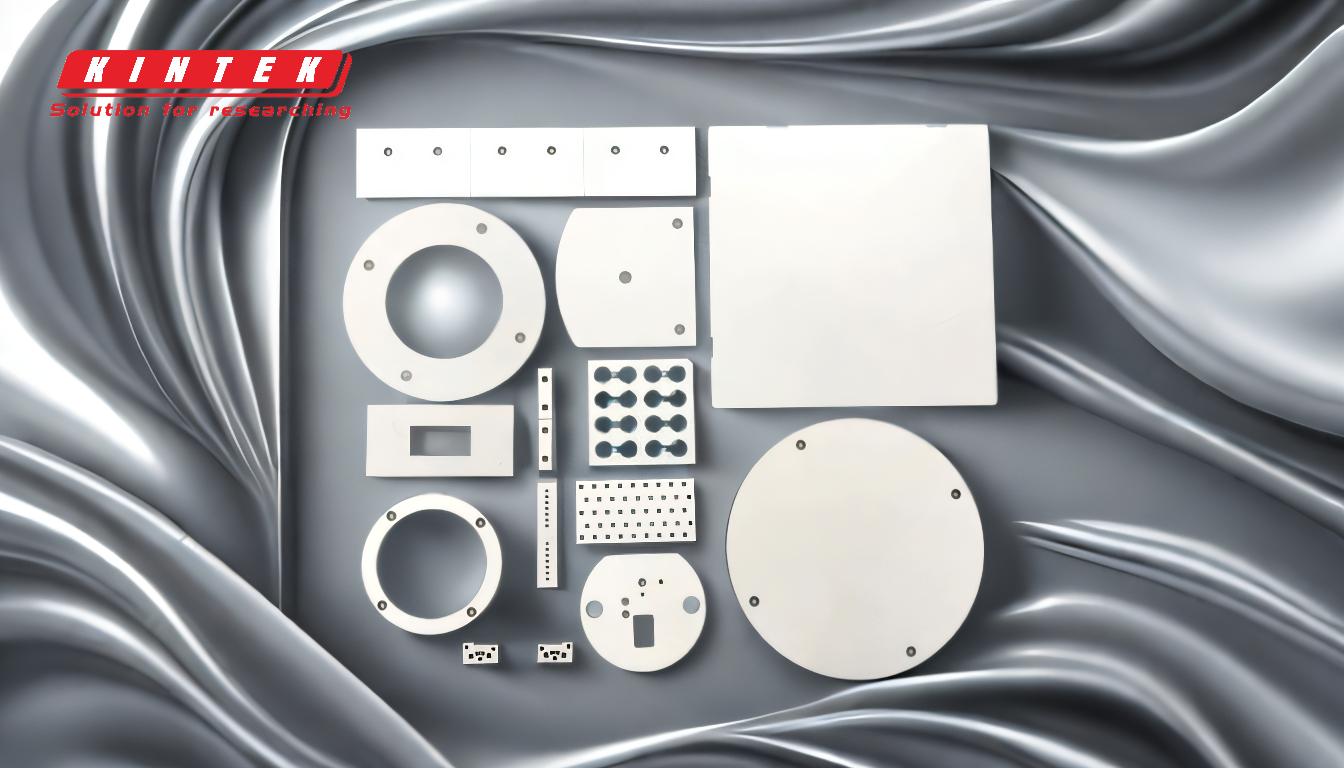
-
Microstructure and Grain Size:
- The microstructure of ceramics, particularly the grain size, plays a critical role in determining their strength. Fine ceramics are characterized by a small and uniform grain size, which enhances their mechanical properties. Smaller grains reduce the likelihood of crack propagation, as grain boundaries act as barriers to crack growth.
- Fine ceramics are engineered to achieve this refined microstructure through advanced processing techniques, such as sintering at controlled temperatures and pressures. This results in a dense and homogeneous material with minimal defects.
-
Composition and Chemical Bonding:
- The chemical composition of ceramics directly influences their strength. Fine ceramics are often composed of high-purity raw materials, such as alumina, zirconia, or silicon carbide, which provide excellent mechanical and thermal properties.
- The type of chemical bonding (ionic or covalent) in ceramics also affects their strength. Covalent bonds, found in materials like silicon carbide, are stronger than ionic bonds, contributing to higher hardness and fracture resistance.
-
Processing Techniques:
- The manufacturing process significantly impacts the strength of ceramics. Fine ceramics are typically produced using advanced techniques like hot pressing, spark plasma sintering, or chemical vapor deposition. These methods ensure a high degree of control over the material's density, grain size, and defect distribution.
- Proper sintering conditions are essential to achieve a dense and defect-free structure. Any residual porosity or impurities can act as stress concentrators, reducing the material's overall strength.
-
Defects and Flaws:
- The presence of defects, such as cracks, voids, or inclusions, can drastically reduce the strength of ceramics. Fine ceramics are designed to minimize these flaws through precise control of the manufacturing process.
- Non-destructive testing methods, such as ultrasonic testing or X-ray tomography, are often used to detect and eliminate defects in fine ceramics, ensuring their reliability in demanding applications.
-
Thermal and Mechanical Properties:
- Fine ceramics are known for their excellent thermal stability and mechanical properties, such as high hardness, wear resistance, and compressive strength. These properties make them suitable for use in extreme environments, such as high-temperature furnaces or abrasive conditions.
- The ability to withstand thermal shock is another critical factor. Fine ceramics with low thermal expansion coefficients and high thermal conductivity are less prone to cracking under rapid temperature changes.
-
Applications and Performance Requirements:
- The strength of fine ceramics is often tailored to meet the specific requirements of their intended applications. For example, in the aerospace industry, ceramics must withstand high temperatures and mechanical stress, while in biomedical applications, they need to be biocompatible and wear-resistant.
- Understanding the relationship between material properties and performance requirements is essential for selecting the right type of fine ceramics for a given application.
By considering these factors, manufacturers and purchasers can make informed decisions about the selection and use of fine ceramics, ensuring optimal performance and durability in their applications. For more detailed information on fine ceramics, visit /topic/fine-ceramics.
Summary Table:
Factor | Impact on Strength |
---|---|
Microstructure & Grain Size | Smaller, uniform grains enhance strength by reducing crack propagation. |
Composition & Bonding | High-purity materials and covalent bonds (e.g., silicon carbide) improve hardness. |
Processing Techniques | Advanced methods like hot pressing ensure dense, defect-free structures. |
Defects & Flaws | Minimizing cracks and voids through precise manufacturing boosts reliability. |
Thermal & Mechanical Properties | High thermal stability and wear resistance make ceramics ideal for extreme conditions. |
Applications | Strength is tailored to meet specific performance requirements in various industries. |
Need high-performance ceramics for your application? Contact our experts today to find the perfect solution!