Chemical vapor deposition (CVD) is a highly versatile and precise thin-film deposition process used across various industries to create durable coatings on materials like glass, metals, and ceramics. It involves chemical reactions in the vapor phase to deposit solid films on heated surfaces, enabling the formation of ultra-thin, high-purity layers. CVD is valued for its ability to produce coatings with tailored properties, such as corrosion resistance, abrasion resistance, and thermal stability. It is widely used in applications ranging from semiconductor manufacturing to the production of nanomaterials like carbon nanotubes and GaN nanowires. Additionally, advanced techniques like plasma-enhanced chemical vapor deposition (PECVD) enhance efficiency by enabling reactions at lower temperatures, making it suitable for delicate substrates.
Key Points Explained:
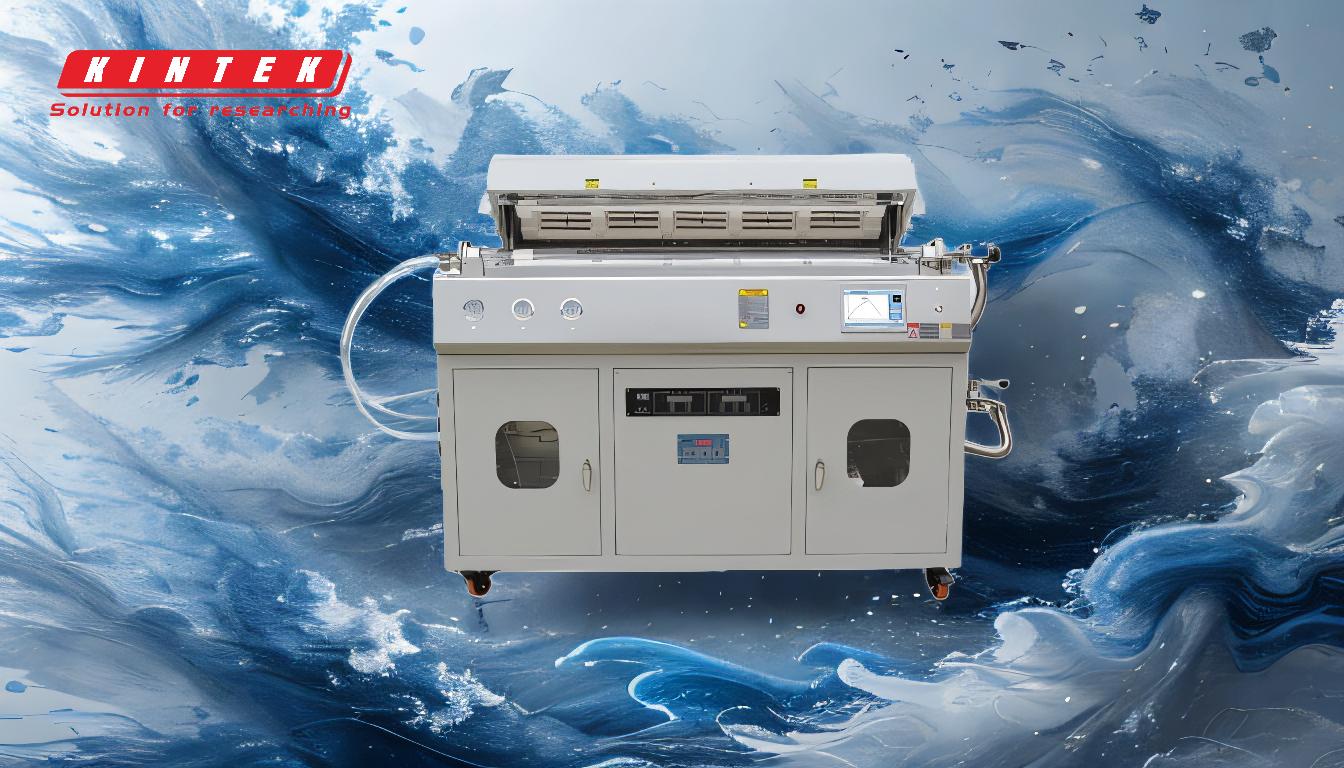
-
Definition and Process of CVD:
- Chemical vapor deposition (CVD) is a process where a solid film is deposited on a heated surface through chemical reactions in the vapor phase. The depositing species can be atoms, molecules, or a combination of both.
- This method is highly precise and requires a high level of skill to control the chemical reactions and deposition conditions.
-
Versatility in Materials and Applications:
- CVD can be applied to a wide range of base materials, including glass, metals, and ceramics, making it suitable for diverse industries.
- It is used to create ultra-thin layers of materials, which are essential for applications like semiconductor manufacturing, electrical circuits, and nanomaterial production (e.g., carbon nanotubes and GaN nanowires).
-
Advantages of CVD:
- Durability: CVD coatings are highly durable and can withstand high-stress environments, extreme temperatures, and temperature variations.
- Customization: The process allows for the optimization of gases to achieve specific properties, such as corrosion resistance or high purity.
- Precision: CVD can coat complex and precision surfaces, ensuring uniform and high-quality results.
-
Plasma-Enhanced Chemical Vapor Deposition (PECVD):
- PECVD is a specialized form of CVD that uses plasma to enhance chemical reactions, enabling deposition at lower temperatures. This makes it ideal for delicate substrates and applications requiring nanometer-thin coatings.
- It is particularly useful for controlling surface chemistry and customizing wetting characteristics of solid substrates.
-
Thermal Vapor Deposition:
- A related technique, thermal vapor deposition, involves heating a solid material in a high vacuum chamber to produce vapor pressure. The vapor then condenses on the substrate to form a thin film.
- This method operates at temperatures between 250 to 350 degrees Celsius and is effective for creating uniform coatings.
-
Applications in Advanced Materials:
- CVD is frequently used to grow advanced materials like carbon nanotubes and GaN nanowires, which are critical in nanotechnology and electronics.
- It is also employed to deposit metallic, ceramic, and semiconducting thin films, further expanding its utility in high-tech industries.
In summary, chemical vapor deposition is a critical process for creating high-performance coatings and thin films with tailored properties. Its versatility, precision, and ability to produce durable and ultra-thin layers make it indispensable in industries ranging from electronics to materials science. Advanced techniques like PECVD further enhance its capabilities, enabling efficient deposition at lower temperatures and expanding its application scope.
Summary Table:
Aspect | Details |
---|---|
Process | Deposits solid films via chemical reactions in the vapor phase. |
Materials | Glass, metals, ceramics, and advanced nanomaterials like carbon nanotubes. |
Key Advantages | Durability, customization, precision, and thermal stability. |
Advanced Techniques | Plasma-enhanced CVD (PECVD) for lower-temperature deposition. |
Applications | Semiconductor manufacturing, nanomaterial production, and thin-film coatings. |
Unlock the potential of chemical vapor deposition for your projects—contact us today to learn more!