A graphite furnace is primarily used for high-temperature applications such as melting, sintering, and material testing. It measures temperature using either a thermocouple or a pyrometer, with the former being a direct-contact method and the latter a non-contact method. These temperature measurement tools ensure precise control over the furnace environment, which is crucial for processes requiring specific thermal conditions. The furnace operates in a vacuum or protective atmosphere to prevent material contamination and oxidation, making it ideal for high-precision material treatment and research.
Key Points Explained:
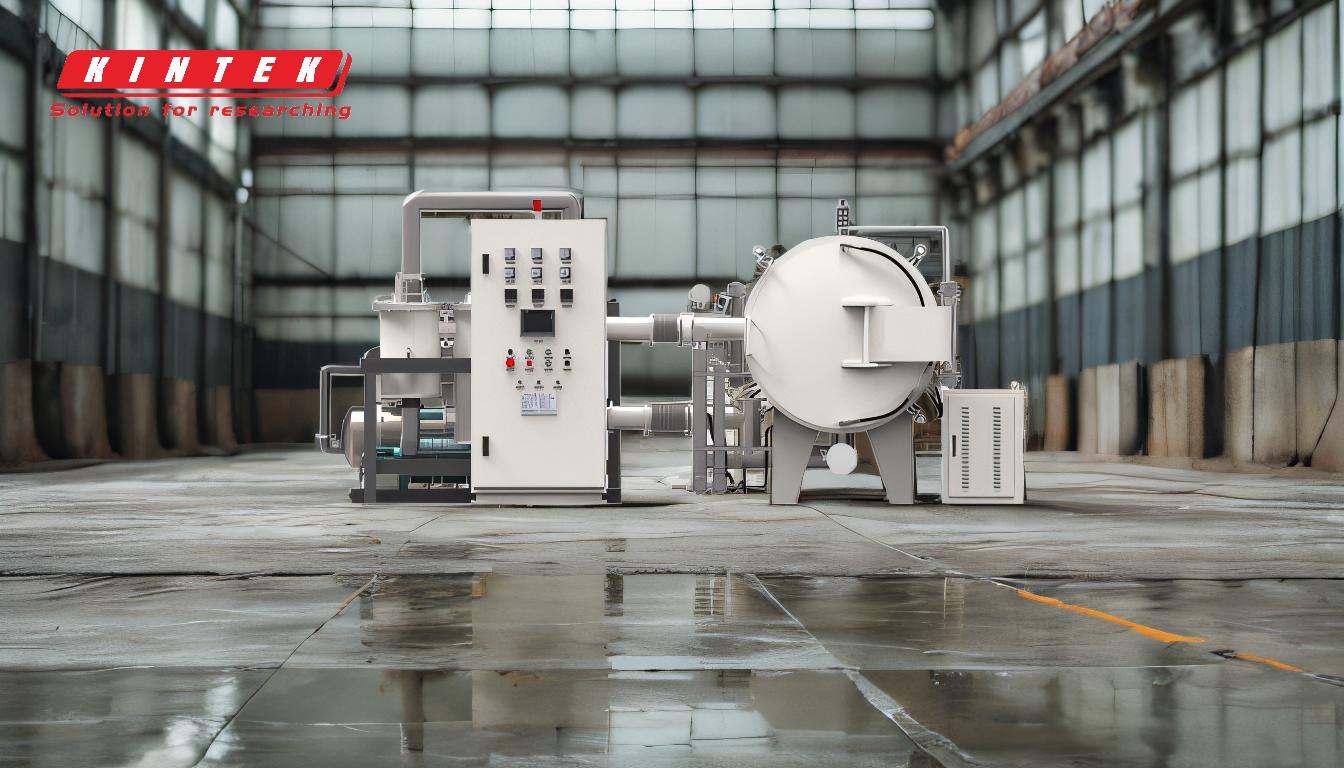
-
Primary Function of a Graphite Furnace:
- Graphite furnaces are designed for high-temperature processes, including melting, sintering, and material testing.
- They are used in environments where precise temperature control is essential, such as in the production of alloys, solid electrolytes, and high-temperature reaction kinetics studies.
-
Temperature Measurement Methods:
- Thermocouples: These are direct-contact temperature sensors that measure the temperature inside the furnace by being in physical contact with the material or the furnace environment. They are often made of materials like W-Re (Tungsten-Rhenium) for high-temperature applications.
- Pyrometers: These are non-contact temperature sensors that measure temperature by detecting the thermal radiation emitted by the furnace or the material. They are particularly useful in environments where direct contact is impractical or could contaminate the material.
-
Operational Environment:
- Vacuum or Protective Atmosphere: Graphite furnaces often operate in a vacuum or under a protective gas atmosphere to prevent oxidation and contamination of the materials being processed. This is crucial for maintaining the integrity and properties of high-purity materials.
- High-Temperature Capability: These furnaces can reach extremely high temperatures, making them suitable for processes that require thermal conditions beyond the capabilities of conventional furnaces.
-
Applications:
- Melting and Alloy Production: Graphite furnaces are used to melt metals and create alloys, where precise temperature control is necessary to achieve the desired material properties.
- Sintering and Foaming: They are employed in sintering processes, where powdered materials are heated to form a solid mass, and in foaming, where gases are introduced to create porous structures.
- Research and Development: Graphite furnaces are essential in laboratories for studying high-temperature reaction kinetics, material behavior under extreme conditions, and the properties of solid electrolytes.
-
Advantages of Using Graphite Furnaces:
- High Thermal Conductivity: Graphite has excellent thermal conductivity, allowing for uniform heating and efficient temperature control.
- Chemical Stability: Graphite is chemically inert at high temperatures, making it suitable for processing reactive materials without contamination.
- Durability: Graphite components are durable and can withstand the harsh conditions of high-temperature environments, reducing maintenance and replacement costs.
-
Challenges and Considerations:
- Material Compatibility: Not all materials are suitable for processing in graphite furnaces, especially those that react with carbon at high temperatures.
- Cost: Graphite furnaces can be expensive to operate and maintain due to the high energy requirements and the need for specialized components like thermocouples and pyrometers.
- Operational Complexity: The need for precise temperature control and the use of vacuum or protective atmospheres add complexity to the operation of graphite furnaces, requiring skilled personnel and advanced control systems.
In summary, a graphite furnace measures temperature using thermocouples or pyrometers to ensure precise control over high-temperature processes. It is used in various applications, including melting, sintering, and material research, often in a vacuum or protective atmosphere to maintain material integrity. The furnace's design and operational environment make it a valuable tool in industries requiring high-temperature material processing and research.
Summary Table:
Aspect | Details |
---|---|
Primary Function | High-temperature processes: melting, sintering, material testing |
Temperature Measurement | Thermocouples (direct-contact) or pyrometers (non-contact) |
Operational Environment | Vacuum or protective atmosphere to prevent oxidation and contamination |
Applications | Melting, alloy production, sintering, foaming, and material research |
Advantages | High thermal conductivity, chemical stability, durability |
Challenges | Material compatibility, high cost, operational complexity |
Ready to elevate your high-temperature processes? Contact our experts today to find the perfect graphite furnace for your needs!