Inerting is a critical process used in various industrial applications, particularly in heat treatment furnaces and fire/explosion prevention engineering. It involves replacing or purging the atmosphere within a system (such as a furnace or container) with inert gases like nitrogen or argon. This process serves two primary purposes: (1) preventing oxidation of materials during heat treatment, and (2) reducing the risk of fire or explosion by eliminating flammable or reactive elements such as oxygen, water, or flammable gases. By creating an oxygen-deficient or non-reactive environment, inerting ensures both the quality of the treated materials and the safety of the operation.
Key Points Explained:
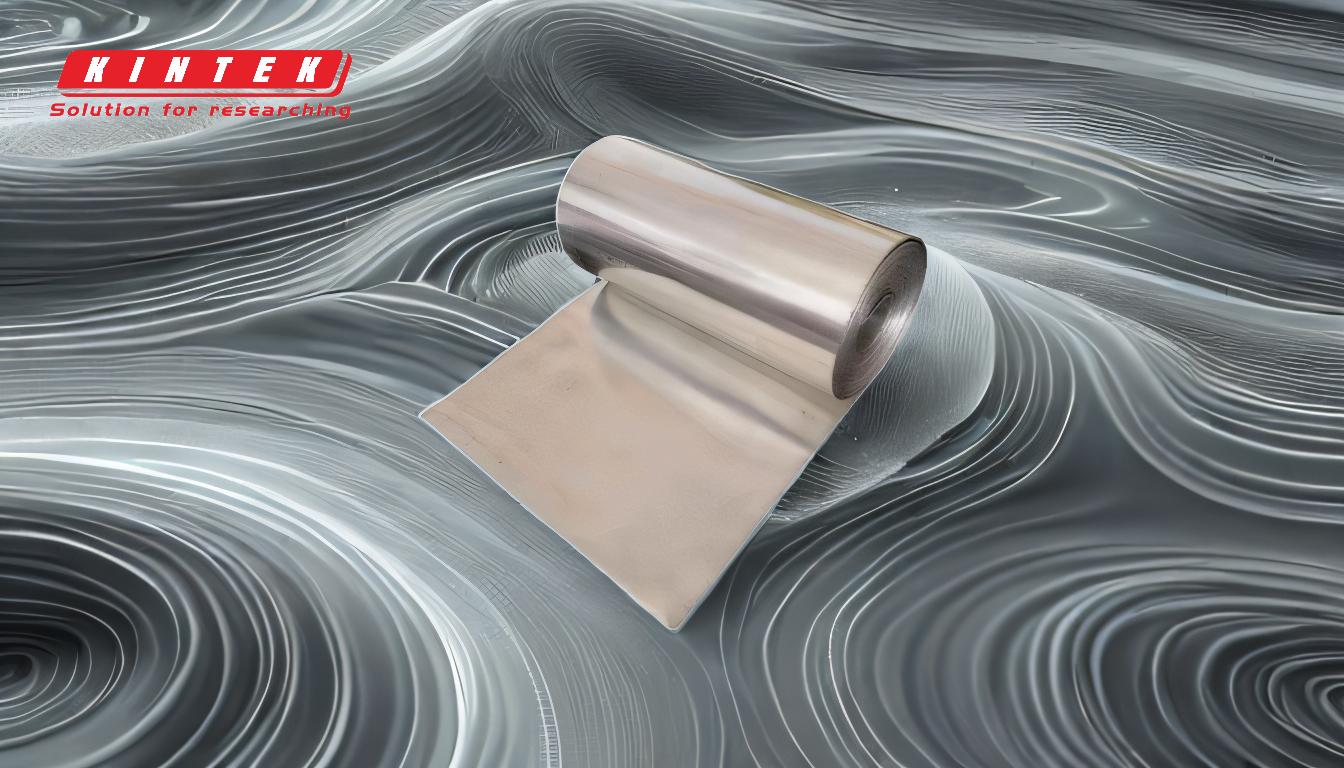
-
Definition of Inerting:
- Inerting refers to the process of introducing inert gases (e.g., nitrogen or argon) into a system to displace or purge unwanted materials, such as oxygen, water, or flammable gases.
- It is commonly used in heat treatment furnaces and fire/explosion prevention systems to create a safe and controlled environment.
-
Purpose of Inerting:
- Preventing Oxidation: In heat treatment furnaces, inerting reduces the risk of oxidation of the materials being treated. Oxidation can degrade the quality of the treated components, leading to defects or failures.
- Safety Measures: Inerting acts as a safety measure by removing flammable or reactive elements (e.g., oxygen, water, or flammable gases) from the system. This minimizes the risk of fire or explosion, especially in closed systems like containers or process vessels.
-
Applications of Inerting:
- Heat Treatment Furnaces: Inerting is used to maintain a controlled atmosphere during heat treatment processes. This ensures that the materials being treated are not exposed to reactive elements that could compromise their integrity.
- Fire and Explosion Prevention: Inerting is employed in closed systems (e.g., storage tanks, pipelines, or process vessels) to create an oxygen-deficient environment, making the atmosphere non-ignitable and reducing the risk of fire or explosion.
-
Inert Gases Used:
- Nitrogen: Widely used due to its availability, cost-effectiveness, and inert properties. Nitrogen is effective in displacing oxygen and other reactive gases.
- Argon: Used in applications requiring a higher level of inertness, such as in specialized heat treatment processes or where nitrogen may react with certain materials.
-
Benefits of Inerting:
- Enhanced Material Quality: By preventing oxidation and contamination, inerting ensures that the treated materials retain their desired properties and performance.
- Improved Safety: Inerting significantly reduces the risk of fire or explosion, protecting both personnel and equipment.
- Process Control: Maintaining a controlled atmosphere allows for precise heat treatment processes, leading to consistent and high-quality results.
-
Considerations for Implementing Inerting:
- System Design: The design of the inerting system must ensure proper gas distribution and complete displacement of unwanted materials.
- Gas Selection: The choice of inert gas (e.g., nitrogen or argon) depends on the specific application and the materials involved.
- Monitoring and Control: Continuous monitoring of the atmosphere within the system is essential to maintain the desired inert conditions and ensure safety.
-
Challenges and Limitations:
- Cost: The cost of inert gases and the equipment required for inerting can be significant, especially for large-scale operations.
- Gas Purity: The purity of the inert gas must be maintained to ensure effective inerting. Contaminants in the gas can compromise the process.
- System Leaks: Any leaks in the system can allow oxygen or other reactive elements to enter, reducing the effectiveness of inerting.
In summary, inerting is a vital process in industrial applications, offering both quality and safety benefits. By understanding its principles, applications, and challenges, equipment and consumable purchasers can make informed decisions to optimize their operations.
Summary Table:
Aspect | Details |
---|---|
Definition | Replacing system atmosphere with inert gases (e.g., nitrogen, argon). |
Purpose | - Prevent oxidation in heat treatment. - Reduce fire/explosion risks. |
Applications | - Heat treatment furnaces. - Fire/explosion prevention systems. |
Inert Gases | - Nitrogen (cost-effective). - Argon (higher inertness). |
Benefits | - Enhanced material quality. - Improved safety. - Precise process control. |
Considerations | - System design. - Gas selection. - Monitoring and control. |
Challenges | - Cost. - Gas purity. - System leaks. |
Optimize your industrial processes with inerting solutions—contact our experts today!