The size of the product in a ball mill is influenced by a variety of factors, including the size and hardness of the particles being ground, the milling conditions (such as mill speed, feed rate, and media filling level), and the desired product specifications. Smaller balls and longer grinding times are generally required to produce smaller particles. The final particle size is also affected by the number of grinding cycles and the residence time inside the mill. Additionally, the productivity of ball mills depends on factors like drum diameter, the ratio of drum diameter to length, physical-chemical properties of the feed material, ball filling and sizes, armor surface shape, rotation speed, milling fineness, and timely removal of the ground product.
Key Points Explained:
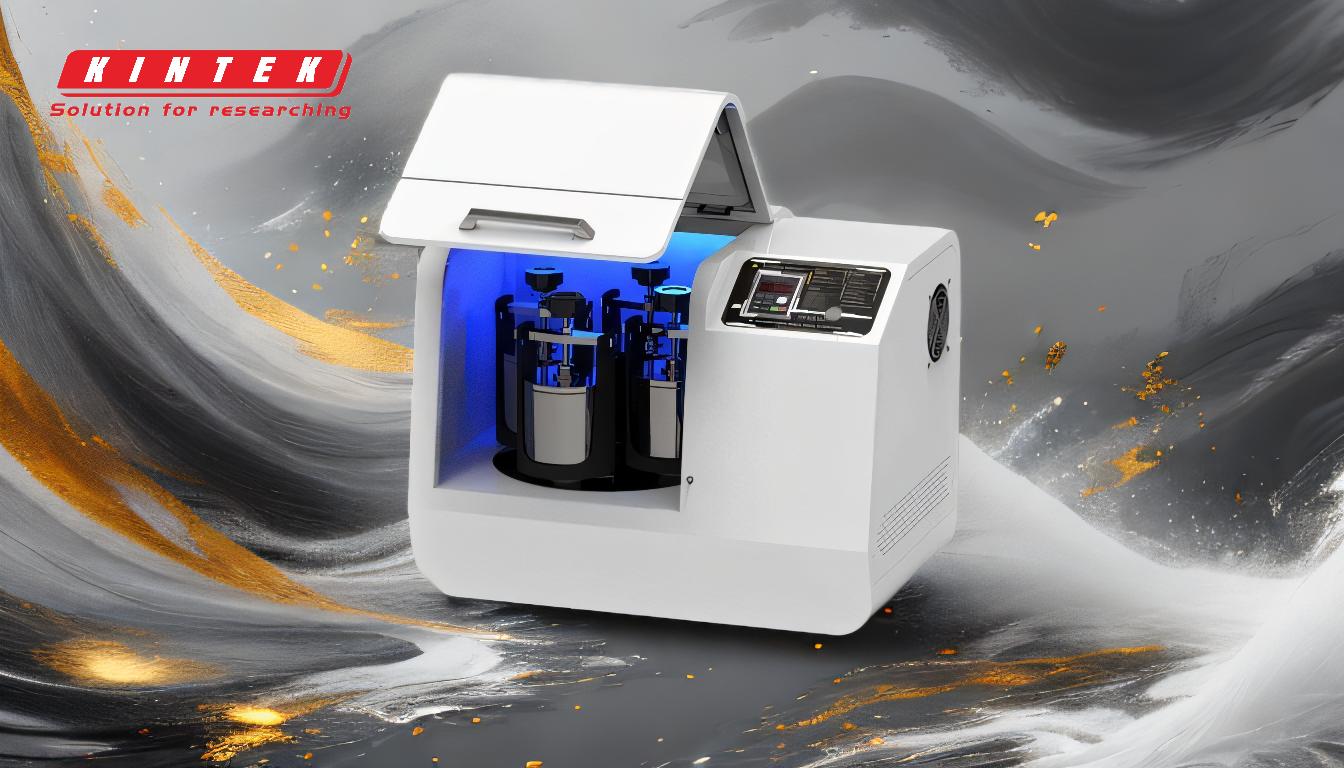
-
Size and Hardness of Particles Being Ground:
- The initial size and hardness of the particles significantly influence the final product size. Harder materials require more energy to break down, which can affect the grinding efficiency and the size of the resulting particles.
- Smaller particles generally require smaller grinding media (balls) and longer grinding times to achieve the desired fineness.
-
Milling Conditions:
- Mill Speed: The speed at which the mill rotates affects the impact and attrition forces on the particles. Optimal speed ensures efficient grinding without excessive wear on the mill components.
- Feed Rate: The rate at which material is fed into the mill can influence the residence time and the degree of grinding. A higher feed rate may reduce the residence time, leading to coarser particles.
- Media Filling Level: The amount of grinding media (balls) in the mill affects the grinding efficiency. An optimal filling level ensures sufficient impact and attrition forces for effective grinding.
-
Desired Product Specifications:
- The target particle size and distribution are crucial in determining the grinding parameters. Smaller particles require finer grinding, which can be achieved by adjusting the milling conditions and using smaller grinding media.
-
Number of Grinding Cycles and Residence Time:
- The number of times the material passes through the grinding zone and the time it spends in the mill (residence time) directly affect the degree of size reduction. Longer residence times and more grinding cycles generally result in finer particles.
-
Physical-Chemical Properties of Feed Material:
- The properties of the material being ground, such as its brittleness, moisture content, and chemical composition, can influence the grinding efficiency and the final particle size. Brittle materials tend to break more easily, while moist materials may require different grinding conditions.
-
Ball Filling and Sizes:
- The size and number of grinding balls in the mill affect the grinding efficiency. Smaller balls are generally used for finer grinding, while larger balls are used for coarser grinding. The filling ratio (percentage of mill volume filled with grinding media) also plays a crucial role in determining the grinding efficiency.
-
Armor Surface Shape:
- The shape and design of the mill's interior surface (armor) can influence the grinding process. A well-designed armor surface can enhance the grinding efficiency by optimizing the impact and attrition forces.
-
Rotation Speed of the Cylinder:
- The rotation speed of the mill cylinder affects the movement of the grinding media and the material. Optimal rotation speed ensures that the grinding media cascade and impact the material effectively, leading to efficient size reduction.
-
Timely Removal of Ground Product:
- Efficient removal of the ground product from the mill is essential to prevent over-grinding and to maintain consistent product quality. Timely removal ensures that the material does not spend excessive time in the mill, which could lead to unnecessary energy consumption and wear.
In summary, the size of the product in a ball mill is influenced by a combination of factors related to the material being ground, the milling conditions, and the desired product specifications. Understanding and optimizing these factors can help achieve the desired particle size and improve the overall efficiency of the grinding process.
Summary Table:
Factor | Impact on Product Size |
---|---|
Size and Hardness of Particles | Harder materials require more energy; smaller particles need smaller balls and longer time |
Mill Speed | Optimal speed ensures efficient grinding without excessive wear |
Feed Rate | Higher feed rates may reduce residence time, leading to coarser particles |
Media Filling Level | Optimal filling ensures sufficient impact and attrition forces |
Desired Product Specifications | Smaller particles require finer grinding and smaller media |
Number of Grinding Cycles | More cycles and longer residence time result in finer particles |
Physical-Chemical Properties | Brittle and moist materials affect grinding efficiency and final size |
Ball Filling and Sizes | Smaller balls for finer grinding; larger balls for coarser grinding |
Armor Surface Shape | Well-designed armor enhances grinding efficiency |
Rotation Speed | Optimal speed ensures effective material impact and grinding |
Timely Removal of Ground Product | Prevents over-grinding and maintains consistent quality |
Optimize your ball mill process for better results—contact our experts today!