Melting aluminum requires furnaces that can handle its relatively low melting point (660°C or 1220°F) while ensuring efficiency, temperature control, and minimal contamination. The most commonly used furnaces for melting aluminum include crucible furnaces, induction furnaces, and reverberatory furnaces. Each type has unique advantages depending on the scale of operation, energy efficiency requirements, and the desired purity of the molten aluminum. Crucible furnaces, often gas or oil-fired, are popular for small to medium-scale operations due to their simplicity and cost-effectiveness. Induction furnaces are preferred for their precision and energy efficiency, while reverberatory furnaces are suitable for large-scale industrial applications. The choice of furnace depends on factors like production volume, energy source availability, and specific application requirements.
Key Points Explained:
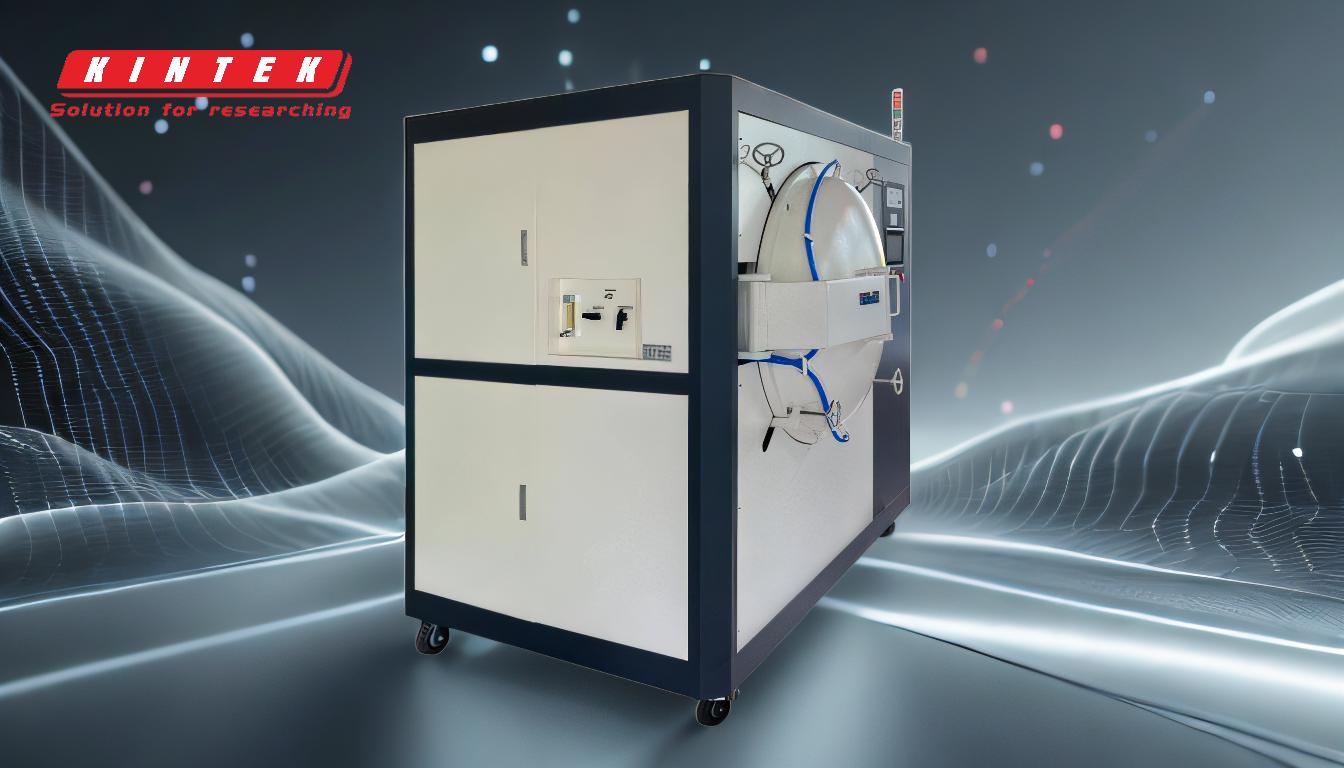
-
Crucible Furnaces for Aluminum Melting
- Crucible furnaces are widely used for melting aluminum, especially in small to medium-scale operations.
- These furnaces use gas or oil as fuel, making them cost-effective and easy to operate.
- The aluminum is placed in a crucible, which is heated directly or indirectly, ensuring controlled melting with minimal contamination.
- Tilting crucible furnaces are particularly useful for pouring molten aluminum into molds, as they allow precise control over the pouring process.
-
Induction Furnaces for Precision and Efficiency
- Induction furnaces are highly efficient and use electromagnetic induction to generate heat directly within the aluminum, reducing energy loss.
- They are ideal for applications requiring high purity and precise temperature control, such as in aerospace or automotive industries.
- Induction furnaces can melt aluminum quickly and are suitable for both small and large-scale operations.
- Their ability to operate without direct flame contact minimizes contamination, making them a preferred choice for high-quality aluminum production.
-
Reverberatory Furnaces for Large-Scale Operations
- Reverberatory furnaces are commonly used in large-scale industrial settings for melting aluminum.
- These furnaces use a flame to heat the aluminum indirectly, with the heat reflecting off the furnace walls to melt the metal.
- They are capable of handling large volumes of aluminum, making them suitable for foundries and recycling facilities.
- However, they may require more energy compared to induction furnaces and can be less efficient for smaller operations.
-
Advantages of Induction Furnaces Over Traditional Methods
- Induction furnaces are more powerful and energy-efficient than traditional furnaces, as they generate heat directly within the metal.
- They offer faster melting times and better temperature uniformity, which is crucial for maintaining aluminum quality.
- The absence of direct flame contact reduces oxidation and contamination, ensuring higher purity of the molten aluminum.
-
Considerations for Choosing the Right Furnace
- Production Volume: For small-scale operations, crucible furnaces are cost-effective, while reverberatory furnaces are better suited for large-scale production.
- Energy Efficiency: Induction furnaces are the most energy-efficient option, making them ideal for high-precision applications.
- Contamination Control: Induction and muffle furnaces offer better contamination control, which is critical for high-purity aluminum.
- Cost and Maintenance: Crucible furnaces are generally cheaper to install and maintain, while induction furnaces may have higher upfront costs but lower operational expenses.
-
Specialized Furnaces for High-Purity Applications
- For applications requiring extremely high purity, such as in electronics or aerospace, specialized furnaces like vacuum or muffle furnaces may be used.
- These furnaces prevent direct flame contact and reduce contamination, ensuring the aluminum meets stringent quality standards.
In summary, the choice of furnace for melting aluminum depends on the specific requirements of the operation, including production volume, energy efficiency, and contamination control. Crucible furnaces are ideal for small-scale operations, induction furnaces offer precision and efficiency, and reverberatory furnaces are suitable for large-scale industrial applications. Understanding the strengths and limitations of each type of furnace is essential for selecting the right equipment for melting aluminum.
Summary Table:
Furnace Type | Best For | Key Features |
---|---|---|
Crucible Furnaces | Small to medium-scale operations | Cost-effective, easy to operate, minimal contamination, precise pouring control |
Induction Furnaces | High-purity applications | Energy-efficient, fast melting, precise temperature control, minimal contamination |
Reverberatory Furnaces | Large-scale industrial use | Handles large volumes, indirect heating, suitable for foundries and recycling |
Need help choosing the right furnace for melting aluminium? Contact our experts today for personalized advice!