Sieve analysis is a widely used method for determining the particle size distribution of granular materials. However, it is not without its challenges and limitations. One common error in sieve analysis is the improper handling of dry particles, which can lead to inaccurate results. This error is particularly significant because sieve analysis is only effective with dry particles, and any moisture present can cause particles to clump together, skewing the size distribution. Additionally, the method's reliance on a limited number of sieves (typically up to 8) can restrict the resolution of the particle size distribution, making it difficult to detect subtle variations in particle size. The minimum measurement limit of 50 µm further complicates the analysis, as finer particles may not be accurately captured. Finally, the process can be time-consuming, especially when dealing with large sample sizes or materials that require extended sieving times.
Key Points Explained:
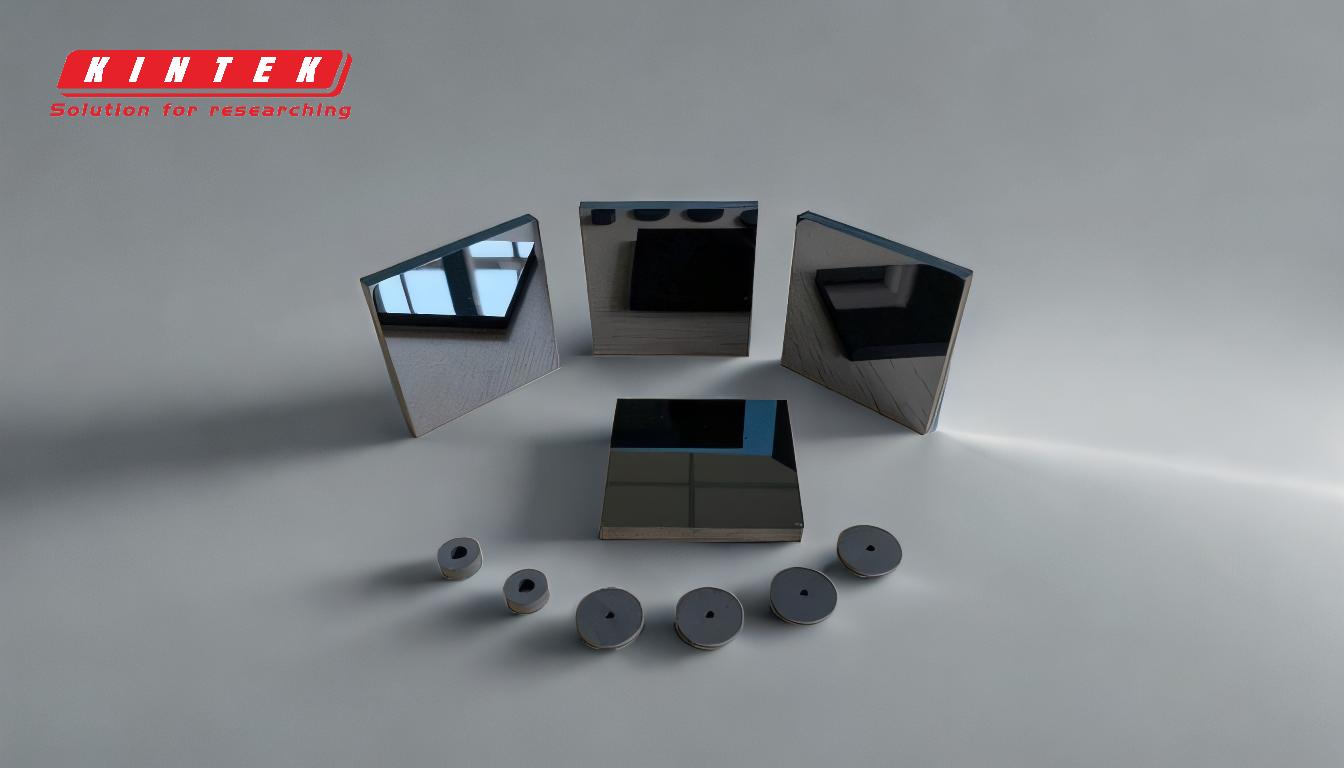
-
Improper Handling of Dry Particles:
- Explanation: Sieve analysis is only effective with dry particles. Moisture can cause particles to clump together, leading to inaccurate size distribution results.
- Impact: This error can significantly skew the results, as clumped particles may be incorrectly classified as larger than they actually are.
- Mitigation: Ensure that the sample is thoroughly dried before analysis. Use a drying oven if necessary to remove any residual moisture.
-
Limited Number of Sieves:
- Explanation: Typically, sieve analysis uses up to 8 sieves, which limits the resolution of the particle size distribution.
- Impact: This limitation can make it difficult to detect subtle variations in particle size, especially in materials with a wide range of particle sizes.
- Mitigation: Consider using a larger number of sieves or alternative methods like laser diffraction for higher resolution.
-
Minimum Measurement Limit:
- Explanation: Sieve analysis has a minimum measurement limit of 50 µm, meaning finer particles may not be accurately captured.
- Impact: This can result in an incomplete understanding of the particle size distribution, particularly for materials with a significant proportion of fine particles.
- Mitigation: For materials with fine particles, consider using complementary techniques such as sedimentation or laser diffraction to capture the full range of particle sizes.
-
Time-Consuming Process:
- Explanation: Sieve analysis can be a time-consuming process, especially with large sample sizes or materials that require extended sieving times.
- Impact: This can lead to inefficiencies in the laboratory, particularly when high throughput is required.
- Mitigation: Optimize the sieving process by using mechanical shakers or automated systems to reduce the time required for analysis.
-
Operator Error:
- Explanation: Human error, such as incorrect sieve stacking or inconsistent shaking, can lead to inaccurate results.
- Impact: Operator error can introduce variability and reduce the reliability of the results.
- Mitigation: Provide thorough training for operators and consider using automated systems to minimize human error.
-
Sample Preparation:
- Explanation: Inadequate sample preparation, such as insufficient mixing or representative sampling, can lead to biased results.
- Impact: This can result in a non-representative particle size distribution, affecting the overall analysis.
- Mitigation: Ensure proper sample preparation techniques are followed, including thorough mixing and representative sampling.
By addressing these common errors and implementing the suggested mitigations, the accuracy and reliability of sieve analysis can be significantly improved. This will ensure that the particle size distribution data obtained is both accurate and representative of the material being analyzed.
Summary Table:
Error | Impact | Mitigation |
---|---|---|
Improper handling of dry particles | Moisture causes clumping, skewing results | Thoroughly dry samples before analysis |
Limited number of sieves | Reduces resolution, making subtle size variations hard to detect | Use more sieves or alternative methods like laser diffraction |
Minimum measurement limit (50 µm) | Finer particles may not be captured | Use sedimentation or laser diffraction for fine particles |
Time-consuming process | Inefficient for large samples or materials requiring extended sieving | Optimize with mechanical shakers or automated systems |
Operator error | Human errors like incorrect stacking or shaking reduce reliability | Train operators and use automated systems |
Inadequate sample preparation | Non-representative sampling leads to biased results | Ensure proper mixing and representative sampling |
Need help improving your sieve analysis accuracy? Contact our experts today for tailored solutions!