A continuous reactor is a type of chemical reactor designed to operate with a constant flow of reactants and products, allowing for continuous processing rather than batch-by-batch production. This system is highly efficient for industrial applications, as it can handle large volumes of reactants and offers advantages such as reduced material usage, lower costs, and faster reaction times. Continuous reactors are versatile and can operate under various conditions, including high temperatures and pressures. They often incorporate advanced technologies, such as impellers or agitators, to ensure uniform mixing and higher-quality outcomes. However, they require careful monitoring to avoid accidents and ensure optimal performance.
Key Points Explained:
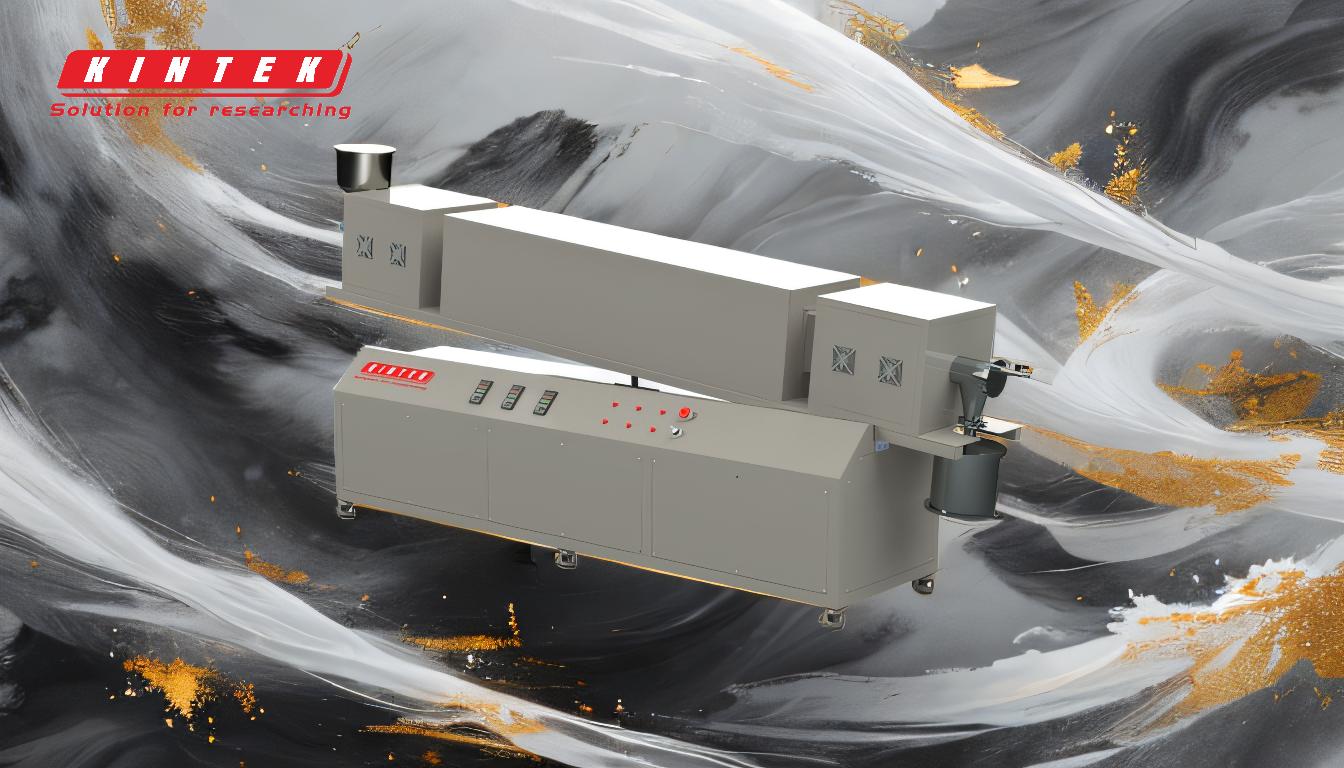
-
Definition and Functionality of Continuous Reactors:
- Continuous reactors are designed to process reactants in a steady flow, enabling continuous production rather than batch processing.
- They are ideal for industrial settings where large volumes of reactants need to be handled efficiently.
- Unlike batch reactors, continuous reactors allow for the addition of reactants on a rolling basis, ensuring uninterrupted operation.
-
Advantages of Continuous Reactors:
- Cost Efficiency: Continuous reactors reduce material usage, leading to lower manufacturing costs.
- Higher Efficiency: Advanced technologies enable rapid screening of reaction conditions, making it easier to optimize processes and improve yields.
- Versatility: These reactors are not limited by factors such as temperature, time, or reactant type, making them suitable for a wide range of chemical processes.
- Improved Quality: Continuous reactors, such as Continuous Stirred-Tank Reactors (CSTRs), use impellers or agitators to ensure uniform mixing, resulting in higher-quality outcomes.
-
Types of Continuous Reactors:
- Continuous Stirred-Tank Reactors (CSTRs): These reactors use an impeller or agitator to mix ingredients thoroughly, ensuring uniform reactions and faster processing times.
- Continuous Flow Reactors: These reactors eliminate challenges associated with traditional batch reactors, offering higher yields and lower production costs.
- Specialized Reactors: Continuous reactors can also include high-pressure reactors, glass-lined reactors, and chemical reactors, each tailored for specific industrial applications.
-
Industrial Applications and Considerations:
- Continuous reactors are widely used in industries requiring high-volume production, such as pharmaceuticals, petrochemicals, and food processing.
- They require careful monitoring to prevent accidents and ensure consistent product quality.
- Their ability to handle large volumes and operate under various conditions makes them a preferred choice for scalable manufacturing processes.
-
Comparison with Batch Reactors:
- Continuous reactors offer faster reaction times and higher throughput compared to batch reactors.
- They are more efficient in terms of material usage and energy consumption, making them cost-effective for large-scale production.
- Batch reactors, on the other hand, are better suited for small-scale or specialized processes where precise control over reaction conditions is required.
-
Future Trends and Innovations:
- Advances in continuous reactor technology are driving improvements in process efficiency, safety, and environmental sustainability.
- Integration with automation and real-time monitoring systems is enhancing the reliability and performance of continuous reactors.
- The development of modular and portable continuous reactors is expanding their applicability to smaller-scale and on-site production needs.
By understanding these key points, equipment and consumable purchasers can make informed decisions about whether continuous reactors are suitable for their specific industrial needs.
Summary Table:
Aspect | Details |
---|---|
Definition | Reactors designed for steady flow of reactants, enabling continuous production. |
Advantages | Cost efficiency, higher efficiency, versatility, improved quality. |
Types | CSTRs, Continuous Flow Reactors, Specialized Reactors (e.g., high-pressure). |
Applications | Pharmaceuticals, petrochemicals, food processing. |
Comparison with Batch | Faster reaction times, higher throughput, cost-effective for large-scale. |
Future Trends | Automation, real-time monitoring, modular and portable designs. |
Ready to optimize your industrial processes? Contact us today to learn more about continuous reactors!