A graphite furnace is a high-temperature heating device that utilizes graphite as a key component due to its excellent thermal conductivity, high-temperature resistance, and chemical stability. It is widely used in various industrial and scientific applications, such as graphitization, sintering, annealing, and material synthesis. The furnace operates by heating materials placed inside a graphite tube or chamber, often in a vacuum or protective atmosphere to prevent oxidation or contamination. Its versatility makes it suitable for processes like ceramic firing, carbon nanotube preparation, and high-temperature material testing.
Key Points Explained:
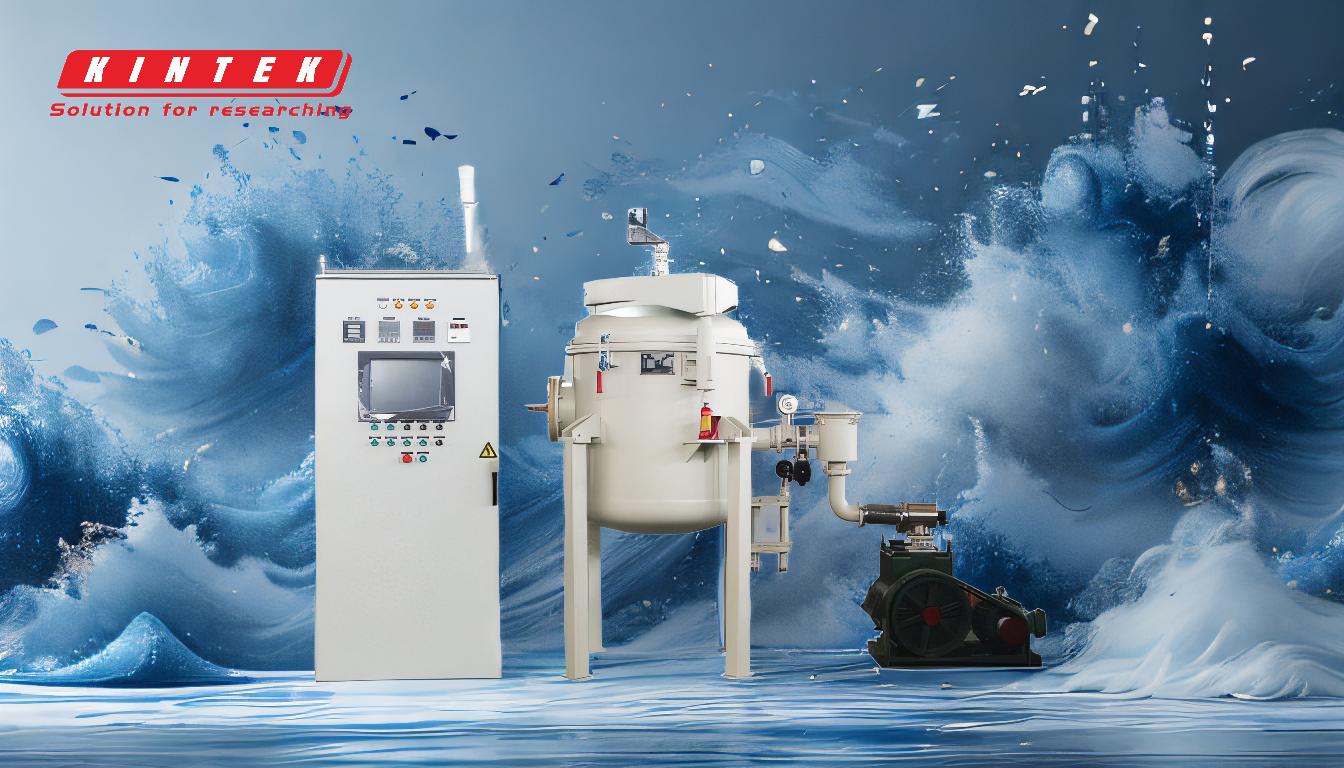
-
Definition and Purpose of a Graphite Furnace
- A graphite furnace is a specialized heating device designed to achieve high temperatures, often exceeding 2000°C, for processing materials.
- It is primarily used for applications requiring controlled heating environments, such as vacuum or protective atmospheres, to prevent material degradation or unwanted chemical reactions.
- The furnace is particularly valued for its ability to handle processes like graphitization, sintering, and annealing, which are critical in material science and industrial manufacturing.
-
Key Components and Design
- Graphite Tubes: The core component of a graphite tube furnace, these tubes provide excellent thermal conductivity and high-temperature resistance.
- Heating Mechanism: The furnace heats materials by placing them inside the graphite tube and applying heat through electrical resistance or induction.
- Atmosphere Control: Many graphite furnaces operate in a vacuum or inert gas environment (e.g., argon or nitrogen) to prevent oxidation and ensure process integrity.
-
Applications of Graphite Furnaces
- Graphitization: Used to convert carbon-based materials into graphite, a process critical for producing electrodes, batteries, and other carbon-based products.
- Sintering: Employed to compact and form solid materials by applying heat and pressure, commonly used in ceramics and metal powder processing.
- Annealing: A heat treatment process to relieve internal stresses and improve material properties, often applied to metals and glass.
- Material Synthesis: Used for growing graphene, carbon nanotubes, and other advanced materials.
- Ceramic Firing and Brazing: Essential for creating high-strength ceramics and joining materials with high-temperature alloys.
- Degassing and Carbonization: Processes to remove impurities or convert organic materials into carbon structures.
-
Advantages of Graphite Furnaces
- High-Temperature Capability: Graphite furnaces can achieve extremely high temperatures, making them suitable for advanced material processing.
- Thermal Efficiency: Graphite's excellent thermal conductivity ensures uniform heating and energy efficiency.
- Chemical Stability: Graphite is resistant to many chemicals, making it ideal for processes involving reactive materials.
- Versatility: The furnace can handle a wide range of applications, from industrial manufacturing to scientific research.
-
Types of Graphite Furnaces
- Graphite Tube Furnaces: Designed with graphite tubes for heating samples or workpieces, commonly used in material synthesis and heat treatment.
- Graphite Resistance Furnaces: Utilize graphite heating elements to generate high temperatures, widely used in graphitization and sintering.
- Vacuum Graphite Furnaces: Operate in a vacuum environment to prevent contamination and oxidation, ideal for high-purity material processing.
-
Industrial and Scientific Relevance
- Graphite furnaces play a critical role in industries such as aerospace, electronics, and energy, where high-performance materials are required.
- In research, they are used for investigating reaction kinetics, high-temperature material properties, and advanced material synthesis.
-
Considerations for Purchasers
- Temperature Range: Ensure the furnace meets the required temperature specifications for your application.
- Atmosphere Control: Choose a furnace with appropriate vacuum or gas control capabilities based on your process needs.
- Durability and Maintenance: Evaluate the quality of graphite components and the ease of maintenance to ensure long-term reliability.
- Energy Efficiency: Consider the furnace's energy consumption and heating efficiency to optimize operational costs.
In summary, a graphite furnace is a versatile and essential tool for high-temperature material processing, offering unmatched thermal performance and chemical stability. Its applications span across industries and research fields, making it a valuable investment for anyone involved in advanced material development or industrial manufacturing.
Summary Table:
Aspect | Details |
---|---|
Key Components | Graphite tubes, heating mechanism, atmosphere control |
Applications | Graphitization, sintering, annealing, material synthesis, ceramic firing |
Advantages | High-temperature capability, thermal efficiency, chemical stability |
Types | Graphite tube, resistance, and vacuum furnaces |
Industrial Relevance | Aerospace, electronics, energy, and advanced material research |
Purchasing Factors | Temperature range, atmosphere control, durability, energy efficiency |
Ready to elevate your material processing? Contact us today to find the perfect graphite furnace for your needs!