Injection molding is a highly efficient manufacturing process that offers several advantages, particularly in terms of speed, cost-effectiveness, and precision. It is especially beneficial for producing small parts with complex shapes and tight tolerances. The process significantly reduces curing time compared to alternative methods, making it faster and more economical for high-volume production. Additionally, injection molding ensures consistent shrinkage and high repeatability, which is crucial for maintaining product quality and precision. Once the initial setup is complete, the process can produce a large volume of parts per hour, making it ideal for mass production.
Key Points Explained:
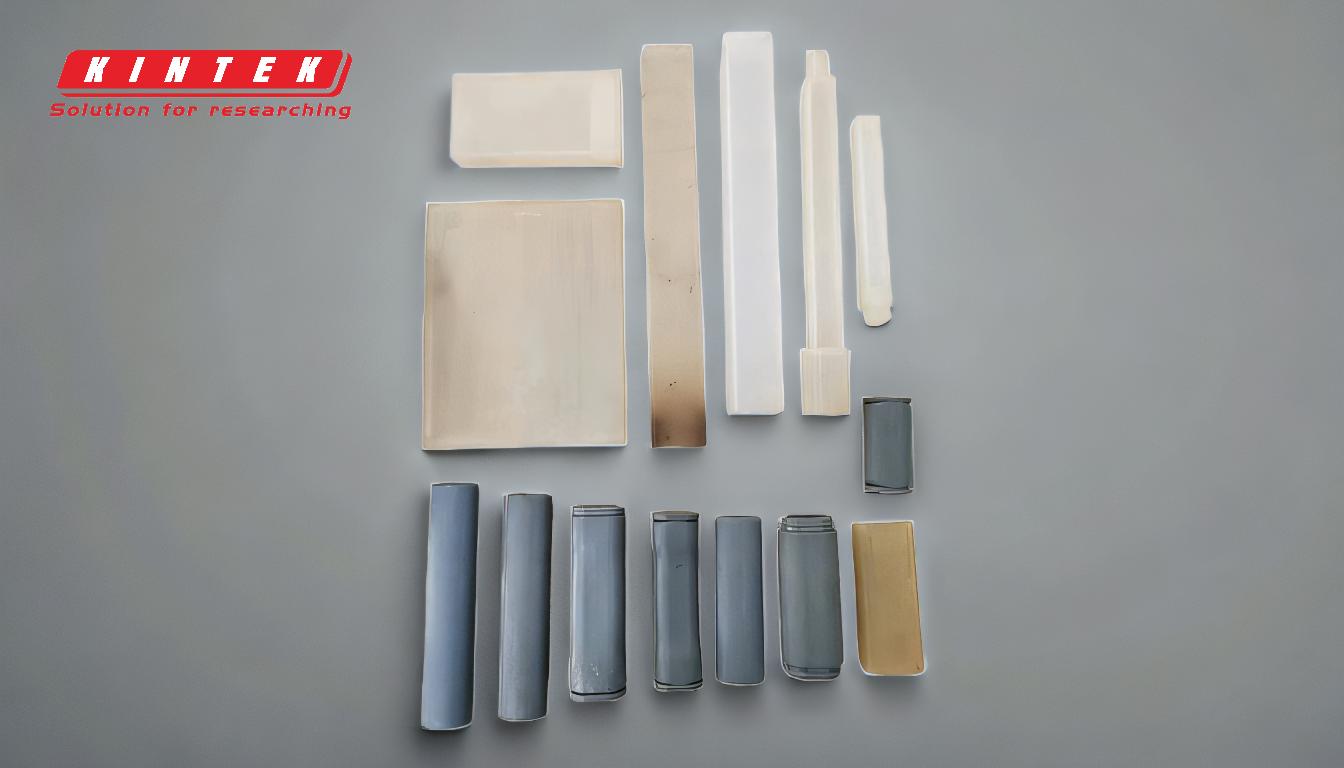
-
Reduced Curing Time:
- Injection molding significantly reduces the curing time compared to other molding methods like compression and transfer molding. The molding cycle in injection molding is about 10 seconds, whereas alternative methods can take 10-20 minutes. This reduction in time leads to faster production rates and lower labor costs.
-
Cost-Effectiveness:
- The process is more cost-effective due to its speed and efficiency. By reducing the time required for each molding cycle, injection molding minimizes labor costs and increases throughput. Additionally, the ability to produce a large volume of parts per hour further enhances its cost-effectiveness.
-
Production of Complex Shapes:
- Injection molding allows for the production of small parts with complex shapes and close tolerances. This is particularly beneficial for industries that require intricate designs and precise dimensions. The process ensures that even the most complex shapes can be produced with high accuracy.
-
Consistent Shrinkage:
- One of the key advantages of injection molding is its ability to produce parts with consistent shrinkage. This consistency is crucial for maintaining the dimensional accuracy and quality of the final product. Consistent shrinkage ensures that each part meets the required specifications, reducing the need for post-production adjustments.
-
High Repeatability:
- Injection molding is a highly repeatable process, meaning that each part produced is virtually identical to the last. This repeatability is essential for mass production, where consistency and quality are paramount. The process ensures that every part meets the same high standards, reducing the risk of defects and increasing overall product reliability.
-
Versatility in Materials:
- Injection molding can be used with a wide range of materials, including various plastics and elastomers like liquid silicone rubber. This versatility allows manufacturers to choose the most suitable material for their specific application, ensuring that the final product meets the desired performance criteria.
-
High Volume Production:
- Once the initial setup is complete, injection molding can produce a large volume of parts per hour. This makes it an ideal choice for mass production, where high output and efficiency are critical. The ability to produce a high volume of parts quickly and consistently is one of the primary reasons why injection molding is widely used in various industries.
In summary, injection molding offers numerous advantages, including reduced curing time, cost-effectiveness, the ability to produce complex shapes, consistent shrinkage, high repeatability, material versatility, and high-volume production capabilities. These benefits make it a preferred choice for manufacturers looking to produce high-quality parts efficiently and economically.
Summary Table:
Advantage | Description |
---|---|
Reduced Curing Time | Molding cycle takes ~10 seconds, compared to 10-20 minutes in alternative methods. |
Cost-Effectiveness | Minimizes labor costs and increases throughput for high-volume production. |
Complex Shapes & Tolerances | Produces small parts with intricate designs and precise dimensions. |
Consistent Shrinkage | Ensures dimensional accuracy and reduces post-production adjustments. |
High Repeatability | Produces virtually identical parts, ensuring consistency and quality. |
Material Versatility | Compatible with various plastics and elastomers for diverse applications. |
High Volume Production | Ideal for mass production with large volumes of parts per hour. |
Ready to enhance your manufacturing process? Contact us today to learn how injection molding can benefit your business!