A PVD (Physical Vapor Deposition) machine is a specialized equipment used to deposit thin films or coatings onto substrates through physical processes. Unlike chemical vapor deposition machine (CVD), which relies on chemical reactions, PVD involves the physical transformation of a solid or liquid material into a vapor, which then condenses onto a substrate to form a thin film. PVD is widely used in industries such as optics, electronics, and manufacturing to enhance surface properties like wear resistance, hardness, and oxidation resistance. It is particularly valued for its ability to produce high-quality, durable coatings with precise control over thickness and composition.
Key Points Explained:
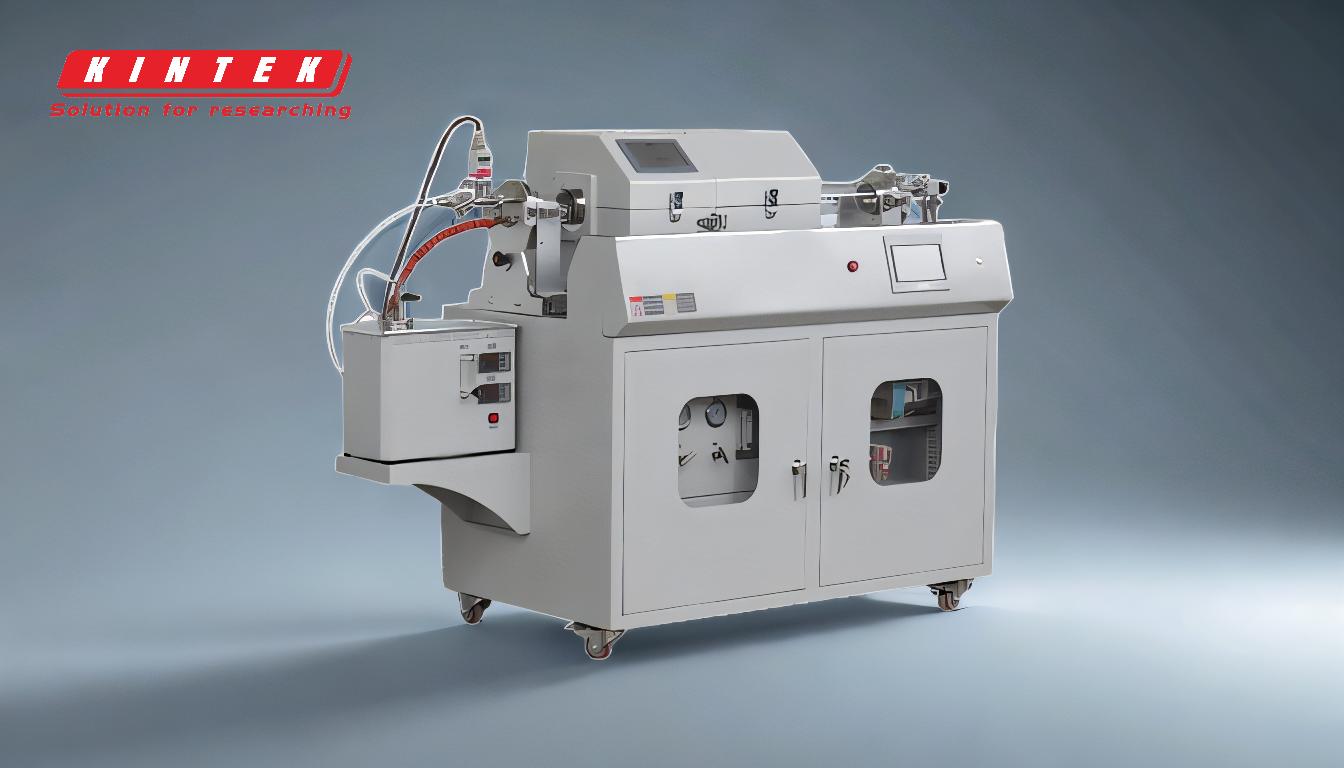
-
Definition and Process of PVD:
- PVD stands for Physical Vapor Deposition, a process where a solid or liquid material is vaporized in a vacuum and then deposited onto a substrate to form a thin film.
- The process involves physical methods such as sputtering, evaporation, or ion plating, rather than chemical reactions. This makes PVD distinct from CVD, which relies on chemical precursors and reactions.
-
Applications of PVD:
- Optics: PVD is used to create highly sophisticated mirrors and coated glasses. Protective, reflective, or absorbing layers can be deposited on optical components like lenses and prisms, which are essential in laser systems and optical instruments.
- Manufacturing: PVD coatings are applied to improve wear resistance, hardness, and oxidation resistance of materials, extending their lifespan and performance.
- Electronics: PVD is used to deposit thin films in semiconductor manufacturing and other electronic applications.
-
Comparison with CVD:
- While PVD uses physical processes to deposit materials, CVD involves chemical reactions between precursors to form thin films. CVD is often used for creating polycrystalline silicon films in integrated circuits, whereas PVD is preferred for applications requiring precise control over coating properties, such as in optics and wear-resistant coatings.
-
Advantages of PVD:
- Precision: PVD allows for precise control over film thickness and composition, making it ideal for high-tech applications.
- Durability: Coatings produced by PVD are highly durable and resistant to wear, oxidation, and corrosion.
- Versatility: PVD can be used with a wide range of materials, including metals, ceramics, and composites.
-
Limitations of PVD:
- Complexity: The process requires a vacuum environment and specialized equipment, making it more complex and costly compared to some other coating methods.
- Material Limitations: Not all materials can be easily vaporized or deposited using PVD, which can limit its applicability in certain scenarios.
-
PVD in Modern Technology:
- PVD is integral to the production of advanced optical components, such as those used in lasers and high-precision instruments. It is also critical in the development of durable coatings for industrial tools and machinery, enhancing their performance and longevity.
By understanding the principles and applications of PVD, purchasers of equipment and consumables can make informed decisions about its use in their specific industries, ensuring optimal performance and cost-effectiveness.
Summary Table:
Aspect | Details |
---|---|
Definition | Physical Vapor Deposition (PVD) involves vaporizing materials in a vacuum to form thin films. |
Process | Uses sputtering, evaporation, or ion plating to deposit materials. |
Applications | Optics (mirrors, lenses), electronics (semiconductors), manufacturing (wear-resistant coatings). |
Advantages | Precise control, durable coatings, versatile material compatibility. |
Limitations | Requires vacuum environment, higher complexity, and cost. |
Interested in how a PVD machine can benefit your industry? Contact us today for expert advice!