A reducing atmosphere in a furnace is a gaseous environment that facilitates chemical reactions by removing oxygen or adding hydrogen, thereby preventing oxidation and promoting reduction. This type of atmosphere is crucial in processes like heat treatment, where it helps achieve specific material properties by controlling the chemical reactions on the surface of the workpiece. For instance, hydrogen in a controlled furnace atmosphere can decarburize steel and reduce iron oxide to iron, altering the material's characteristics. Additionally, a uniform atmosphere ensures consistent carbon concentration in carburizing workpieces, preventing local carburizing or decarburizing during quenching. The atmosphere also plays a role in heat transfer, acting as a thermal conductor or heat load, and can be replaced by other gaseous mediums to facilitate surface protection finishes.
Key Points Explained:
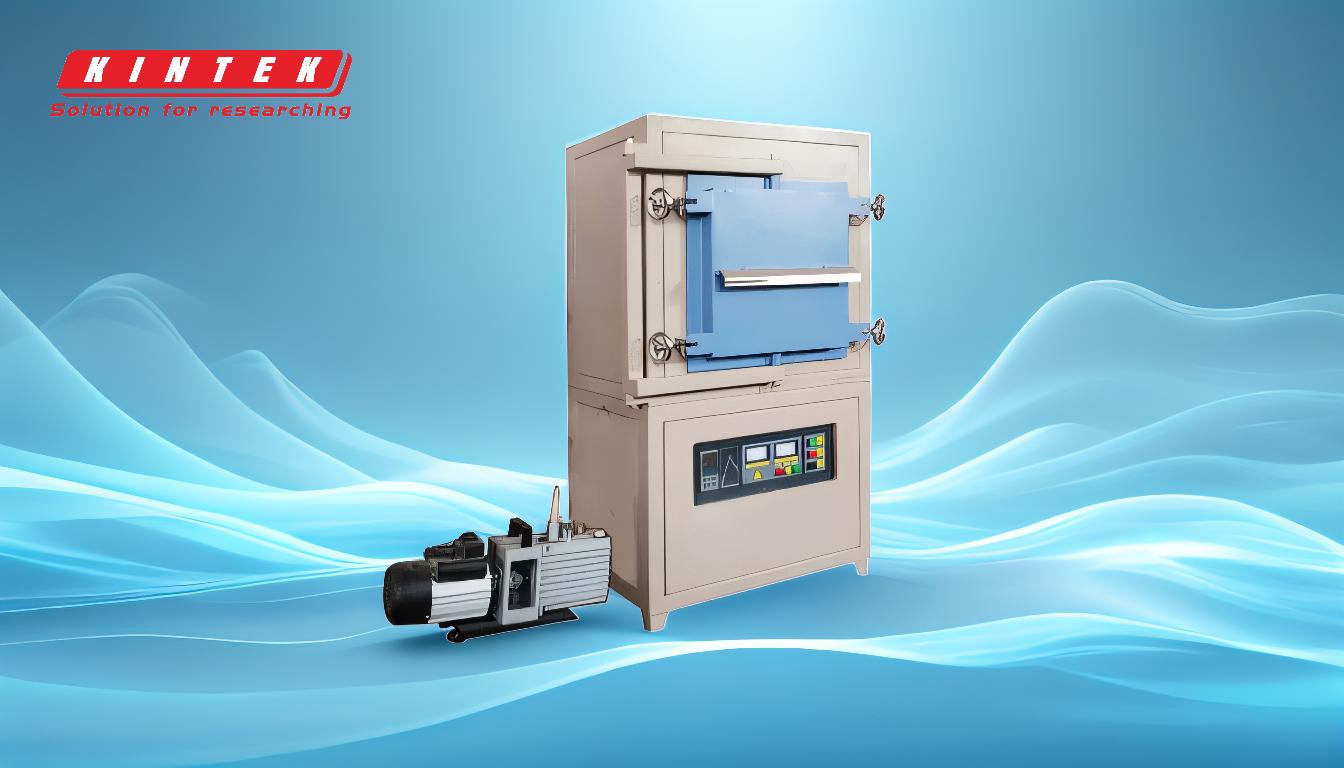
-
Definition of a Reducing Atmosphere:
- A reducing atmosphere is a gaseous environment in a furnace that promotes reduction reactions by either removing oxygen or introducing hydrogen. This prevents oxidation and facilitates processes like decarburization and surface layer alteration.
-
Role in Heat Treatment Processes:
- In heat treatment, a reducing atmosphere is used to achieve specific material properties. For example, hydrogen can decarburize steel and reduce iron oxide to iron, which is essential for certain applications.
-
Uniform Atmosphere for Consistency:
- A uniform atmosphere ensures consistent carbon concentration in carburizing workpieces. This prevents issues like local carburizing or decarburizing during quenching, which can affect the material's properties.
-
Atmosphere as a Thermal Conductor:
- The atmosphere in a furnace can function as a heat load or thermal conductor, convecting thermal energies from the furnace walls to the workpiece. This helps in maintaining uniform furnace temperature and accelerating heat transfer.
-
Replacement with Other Gaseous Mediums:
- The atmosphere can be replaced by a second gaseous medium to facilitate the formation of different surface protection finishes. This chemically alters the surface layer of the workpiece, providing specific properties like corrosion resistance or hardness.
-
Vacuum Atmosphere for Oxygen-Free Environments:
- In some cases, a vacuum atmosphere is required to achieve a complete absence of oxygen or other elements. Different levels of vacuum pressure (rough, fine, high, and ultra-high) are achieved using various vacuum pumps, depending on the application.
By understanding these key points, one can better appreciate the importance of a reducing atmosphere in furnace operations, particularly in achieving desired material properties and ensuring process consistency.
Summary Table:
Key Aspect | Description |
---|---|
Definition | A gaseous environment that removes oxygen or adds hydrogen to prevent oxidation. |
Role in Heat Treatment | Achieves specific material properties like decarburization and surface alteration. |
Uniform Atmosphere | Ensures consistent carbon concentration, preventing local carburizing issues. |
Thermal Conductor | Acts as a heat load or conductor, maintaining uniform furnace temperatures. |
Gaseous Medium Replacement | Replaced with other gases to create surface protection finishes. |
Vacuum Atmosphere | Used for oxygen-free environments with varying vacuum pressure levels. |
Discover how a reducing atmosphere can optimize your furnace processes—contact our experts today!