Thermally activated Chemical Vapor Deposition (CVD) is a process used to deposit thin films of materials onto a substrate by utilizing thermal energy to drive chemical reactions in the gas phase. This method involves introducing gaseous precursors into a reaction chamber, where heat activates the chemical reactions that result in the deposition of a solid material on the substrate. The process is widely used in industries such as semiconductors, optics, and coatings, due to its ability to produce high-quality, uniform films with precise control over thickness and composition. The thermal activation ensures that the reactions occur at the substrate surface, allowing for the formation of dense, adherent films.
Key Points Explained:
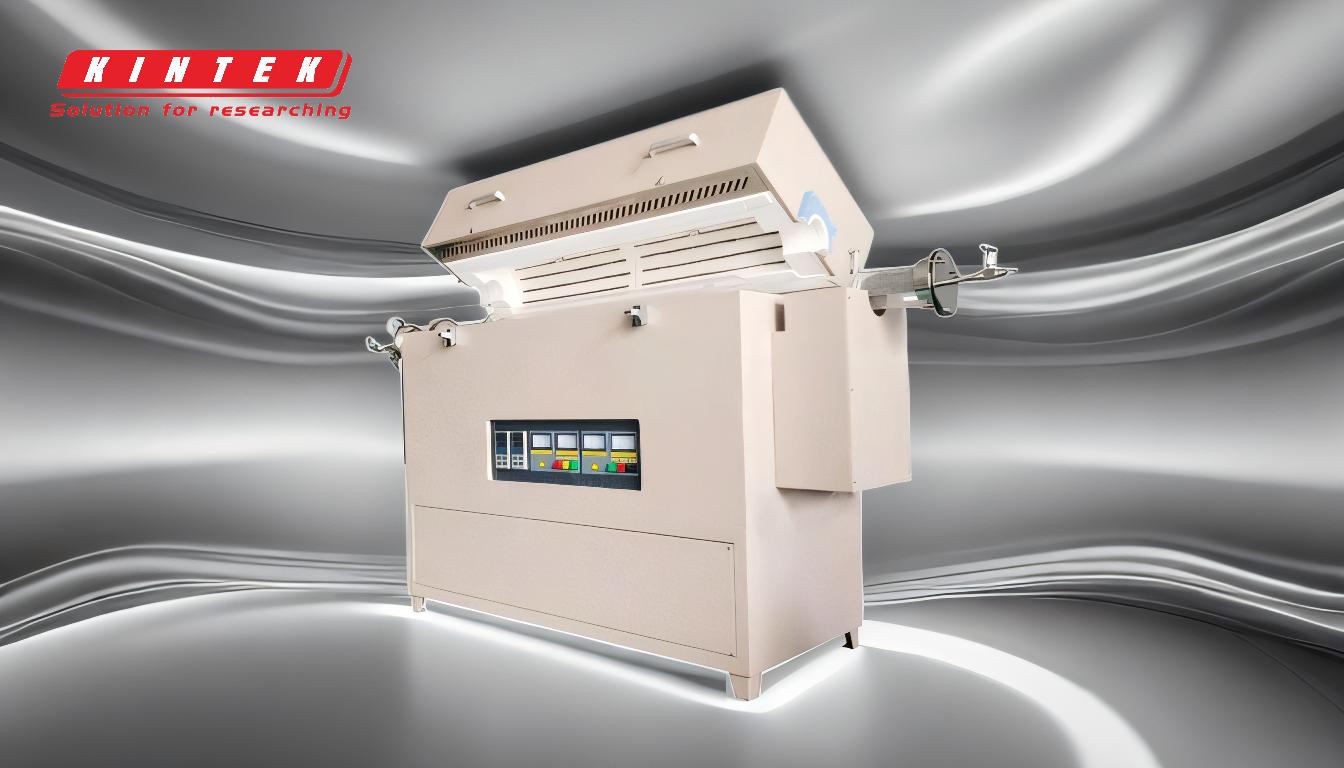
-
Definition of Thermally Activated CVD:
- Thermally activated CVD is a process where gaseous precursors are introduced into a reaction chamber and thermally activated to deposit thin films on a substrate. The heat provides the energy needed for the chemical reactions to occur, leading to the formation of a solid film on the substrate.
-
Process Components:
- Gas Delivery System: Supplies the gaseous precursors to the reaction chamber.
- Reacting Chamber: The environment where the chemical reactions take place.
- Substrate Loading Mechanism: Holds and positions the substrate within the chamber.
- Energy Supplier: Provides the thermal energy needed to activate the chemical reactions.
-
Thermal Activation:
- The thermal energy in CVD is crucial as it drives the chemical reactions necessary for film deposition. The substrate temperature is carefully controlled to ensure optimal reaction conditions, which can affect the quality and properties of the deposited film.
-
Vacuum Environment:
- CVD processes often occur in a vacuum to control the pressure and reduce contamination. The vacuum environment also helps in maintaining the purity of the deposited film by minimizing the presence of unwanted gases.
-
Applications of Thermally Activated CVD:
- Semiconductors: Used for depositing thin films of silicon, silicon nitride, and other materials essential for semiconductor devices.
- Optics: Applied in the production of anti-reflective coatings and other optical films.
- Coatings: Utilized for protective and functional coatings on various materials.
-
Advantages of Thermally Activated CVD:
- High-Quality Films: Produces uniform, dense, and adherent films with precise control over thickness and composition.
- Versatility: Can be used to deposit a wide range of materials, including metals, ceramics, and polymers.
- Scalability: Suitable for both small-scale laboratory research and large-scale industrial production.
-
Comparison with Short Path Vacuum Distillation:
- While both processes involve the use of vacuum environments, they serve different purposes. Thermally activated CVD is focused on depositing thin films, whereas short path vacuum distillation is used for separating and purifying compounds by exploiting differences in their boiling points under reduced pressure.
-
Challenges and Considerations:
- Temperature Control: Precise control of the substrate temperature is critical to ensure the desired film properties.
- Gas Flow and Pressure: Managing the flow rates and pressures of the gaseous precursors is essential for consistent film quality.
- Contamination: Maintaining a clean vacuum environment is necessary to prevent impurities from affecting the film.
In summary, thermally activated CVD is a sophisticated technique for depositing high-quality thin films through the use of thermal energy to drive chemical reactions in a controlled environment. Its applications span various industries, and it offers significant advantages in terms of film quality and versatility. Understanding the process components, thermal activation, and the role of vacuum environments is crucial for optimizing the CVD process for specific applications.
Summary Table:
Aspect | Details |
---|---|
Definition | A process using thermal energy to deposit thin films via chemical reactions. |
Key Components | Gas delivery system, reacting chamber, substrate loading, energy supplier. |
Applications | Semiconductors, optics, protective coatings. |
Advantages | High-quality films, versatility, scalability. |
Challenges | Precise temperature control, gas flow management, contamination prevention. |
Discover how thermally activated CVD can enhance your processes—contact our experts today!