Thin film adhesion refers to the strength of the bond between a thin film and its substrate, which is critical for ensuring the durability, reliability, and functionality of the thin film in various applications. Adhesion is influenced by factors such as surface preparation, material compatibility, and deposition techniques. Poor adhesion can lead to delamination, reduced performance, or failure of the thin film in applications like semiconductors, displays, and medical devices. Understanding and optimizing adhesion is essential for achieving desired mechanical, electrical, or optical properties in thin films.
Key Points Explained:
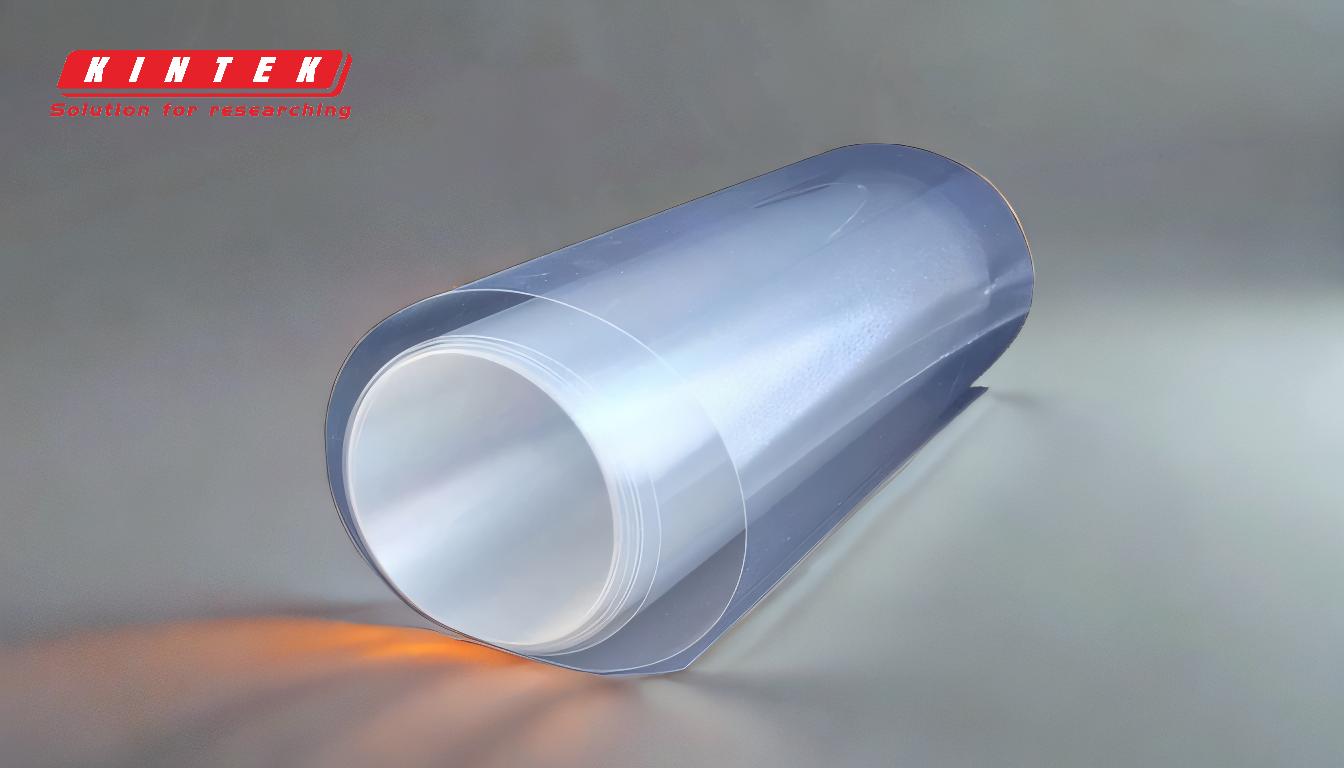
-
Definition of Adhesion in Thin Films:
- Adhesion refers to the bonding strength between the thin film and the substrate it is deposited on. It is a measure of how well the thin film sticks to the substrate under mechanical, thermal, or environmental stress.
- Strong adhesion ensures the thin film remains intact and functional during its operational lifespan.
-
Importance of Adhesion:
- Adhesion is critical for the performance and durability of thin films in applications such as semiconductors, displays, and medical devices.
- Poor adhesion can lead to delamination, cracking, or peeling, which compromises the functionality of the thin film and the device it is part of.
-
Factors Influencing Adhesion:
- Surface Preparation: Proper cleaning and treatment of the substrate surface (e.g., plasma cleaning, chemical etching) enhance adhesion by removing contaminants and creating a reactive surface.
- Material Compatibility: The chemical and physical properties of both the thin film and substrate must be compatible to ensure strong bonding.
- Deposition Techniques: Methods like physical vapor deposition (PVD), chemical vapor deposition (CVD), and atomic layer deposition (ALD) can influence adhesion by controlling the deposition rate, temperature, and energy.
- Interfacial Layer: The formation of an interfacial layer (e.g., oxide layer) can either improve or hinder adhesion, depending on the materials and conditions.
-
Measurement of Adhesion:
- Adhesion strength can be measured using techniques such as scratch testing, peel testing, and pull-off testing.
- These methods evaluate the force required to separate the thin film from the substrate, providing quantitative data on adhesion quality.
-
Applications and Implications:
- In semiconductors, strong adhesion ensures reliable electrical connections and prevents device failure.
- In displays, adhesion affects the durability and optical performance of coatings.
- In medical devices, adhesion is crucial for biocompatibility and long-term functionality.
-
Challenges and Solutions:
- Challenges: Achieving consistent adhesion across large areas or complex geometries can be difficult. Environmental factors like humidity and temperature can also affect adhesion.
- Solutions: Advanced surface treatments, optimized deposition parameters, and the use of adhesion-promoting layers (e.g., primers or tie layers) can improve adhesion.
-
Future Trends:
- Research is focused on developing new materials and deposition techniques to enhance adhesion in emerging applications like flexible electronics and nanotechnology.
- Innovations in surface characterization and adhesion testing are also advancing the understanding of thin film adhesion mechanisms.
By addressing these key points, manufacturers and researchers can optimize thin film adhesion, ensuring the reliability and performance of thin films in a wide range of applications.
Summary Table:
Key Aspect | Details |
---|---|
Definition | Bonding strength between thin film and substrate. |
Importance | Ensures durability, reliability, and functionality in applications. |
Influencing Factors | Surface preparation, material compatibility, deposition techniques. |
Measurement Techniques | Scratch testing, peel testing, pull-off testing. |
Applications | Semiconductors, displays, medical devices. |
Challenges | Consistent adhesion, environmental factors. |
Solutions | Advanced surface treatments, optimized deposition, adhesion-promoting layers. |
Future Trends | New materials, deposition techniques, and advanced testing methods. |
Optimize your thin film adhesion for superior performance—contact our experts today!