Atomic Layer Deposition (ALD) is a highly precise and controlled thin-film deposition technique used extensively in semiconductor manufacturing and other advanced industries. It involves the sequential introduction of two or more precursor materials into a reaction chamber, where they chemically react with the substrate surface to form ultra-thin, uniform layers. The process is self-limiting, meaning each reaction cycle deposits a single atomic layer, ensuring exceptional thickness control and conformality. ALD is particularly valued for its ability to produce high-quality films on complex geometries, nanoparticles, and high-aspect-ratio structures, making it indispensable for applications like nanomaterial fabrication, biomedical devices, and semiconductor process technologies.
Key Points Explained:
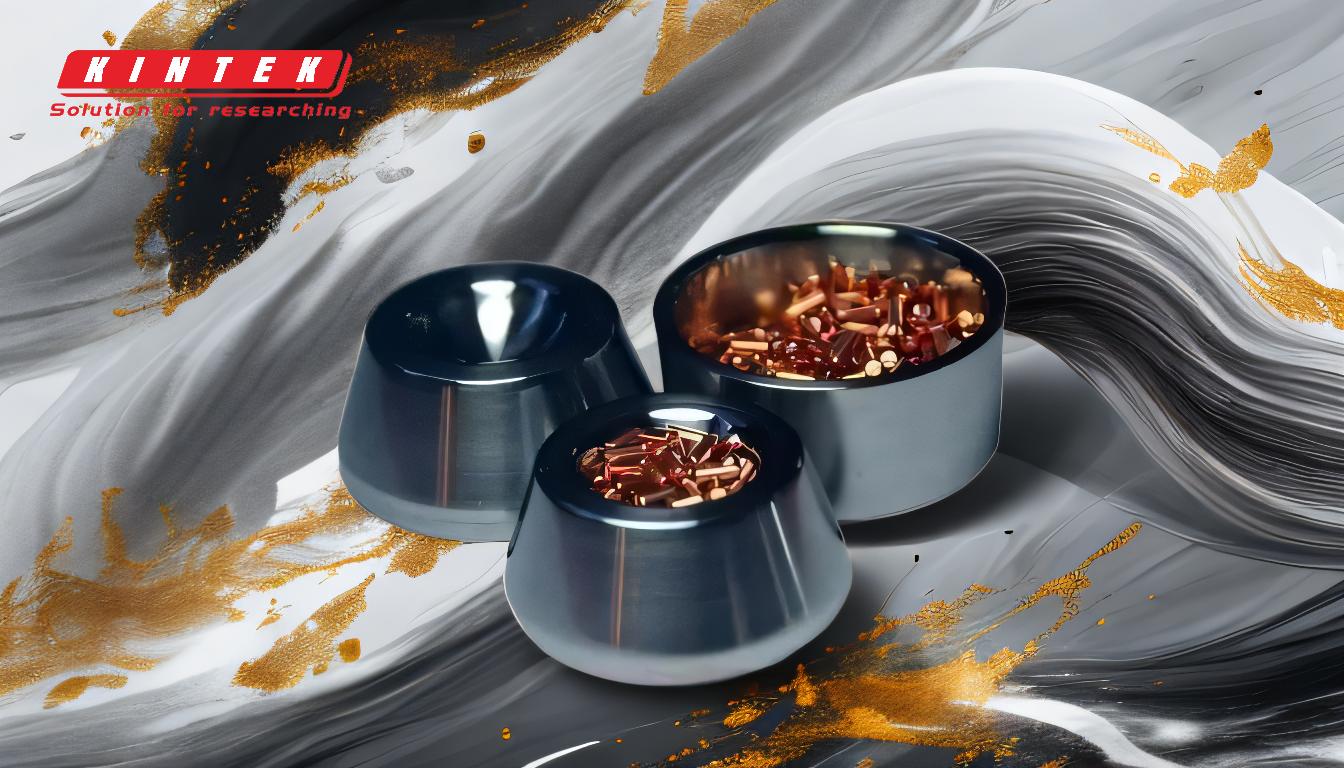
-
Sequential and Self-Limiting Process:
- ALD operates by introducing two or more precursor materials into the reaction chamber in a sequential manner.
- The first precursor adsorbs onto the substrate surface, forming a chemically-bound monolayer.
- The second precursor is then introduced, reacting with the first to create a thin film layer.
- Each reaction cycle is self-limiting, meaning it stops once the surface is fully saturated, ensuring atomic-level precision.
-
Precision and Uniformity:
- ALD is renowned for its ability to deposit films with exceptional uniformity and conformality.
- The process can achieve film thicknesses as low as a few angstroms per cycle, with predictable growth rates.
- This precision is critical for applications requiring ultra-thin films, such as semiconductor devices and nanomaterials.
-
Conformality on Complex Structures:
- ALD excels at coating complex geometries, including high-aspect-ratio features, nanoparticles, and curved surfaces.
- The technique can achieve conformal coverage even on structures with aspect ratios as high as 2000:1, ensuring uniform film deposition across all surfaces.
-
Process Steps:
- Precursor Introduction: The first precursor is introduced into the chamber, where it forms a monolayer on the substrate.
- Purge: Excess precursor and by-products are removed through evacuation and purging.
- Reactant Introduction: The second precursor is introduced, reacting with the adsorbed monolayer to form the desired film.
- Purge: The chamber is purged again to remove any remaining reactants or by-products.
- This cycle is repeated until the desired film thickness is achieved.
-
Applications in Semiconductor Industry:
- ALD is widely used in semiconductor manufacturing for depositing high-k dielectrics, gate oxides, and diffusion barriers.
- Its ability to produce uniform, ultra-thin films is essential for the miniaturization and performance enhancement of modern electronic devices.
-
Advantages Over Other Deposition Methods:
- Compared to techniques like Chemical Vapor Deposition (CVD), ALD offers superior control over film thickness and conformality.
- It is particularly advantageous for depositing films on nanostructures and complex geometries where other methods may fail.
-
Challenges and Expertise:
- While ALD provides exceptional control, it requires precise monitoring and expertise to optimize precursor selection, reaction conditions, and cycle parameters.
- The process can be slower than other deposition methods due to its sequential nature, but the trade-off is unmatched precision and quality.
-
Versatility in Materials:
- ALD can deposit a wide range of materials, including oxides, nitrides, metals, and polymers.
- This versatility makes it suitable for diverse applications, from semiconductor fabrication to biomedical engineering.
-
Scalability and Repeatability:
- ALD is highly repeatable, with predictable growth rates and consistent film properties across multiple cycles.
- The process can be scaled for industrial applications, making it a reliable choice for high-volume production.
-
Future Prospects:
- As semiconductor devices continue to shrink, ALD will play an increasingly critical role in enabling the next generation of technologies.
- Ongoing research is focused on expanding the range of materials and applications for ALD, further enhancing its utility in advanced manufacturing.
In summary, ALD is a cornerstone technology in modern semiconductor processes, offering unparalleled precision, uniformity, and conformality. Its ability to deposit ultra-thin films on complex structures makes it indispensable for advancing nanotechnology and semiconductor device fabrication.
Summary Table:
Key Aspect | Description |
---|---|
Process | Sequential, self-limiting chemical reactions for atomic-level precision. |
Precision & Uniformity | Achieves film thicknesses as low as a few angstroms with predictable growth. |
Conformality | Coats complex geometries, including high-aspect-ratio structures (up to 2000:1). |
Applications | Semiconductors, nanomaterials, biomedical devices, and more. |
Advantages | Superior thickness control, conformality, and versatility in material deposition. |
Challenges | Requires expertise and precise monitoring; slower than some methods. |
Future Prospects | Critical for next-gen semiconductor technologies and advanced manufacturing. |
Unlock the potential of ALD for your projects—contact our experts today to learn more!