Physical Vapor Deposition (PVD) is a widely used technique in various industries for coating surfaces with thin films of materials. One of the most common examples of a PVD process is sputter deposition, which is extensively used in both decorative and functional applications. This method involves bombarding a target material with high-energy ions, causing atoms to be ejected from the target and deposited onto a substrate, forming a thin, uniform film. Sputter deposition is valued for its ability to produce high-quality, durable coatings with excellent adhesion and uniformity, making it suitable for applications ranging from electronics to automotive components.
Key Points Explained:
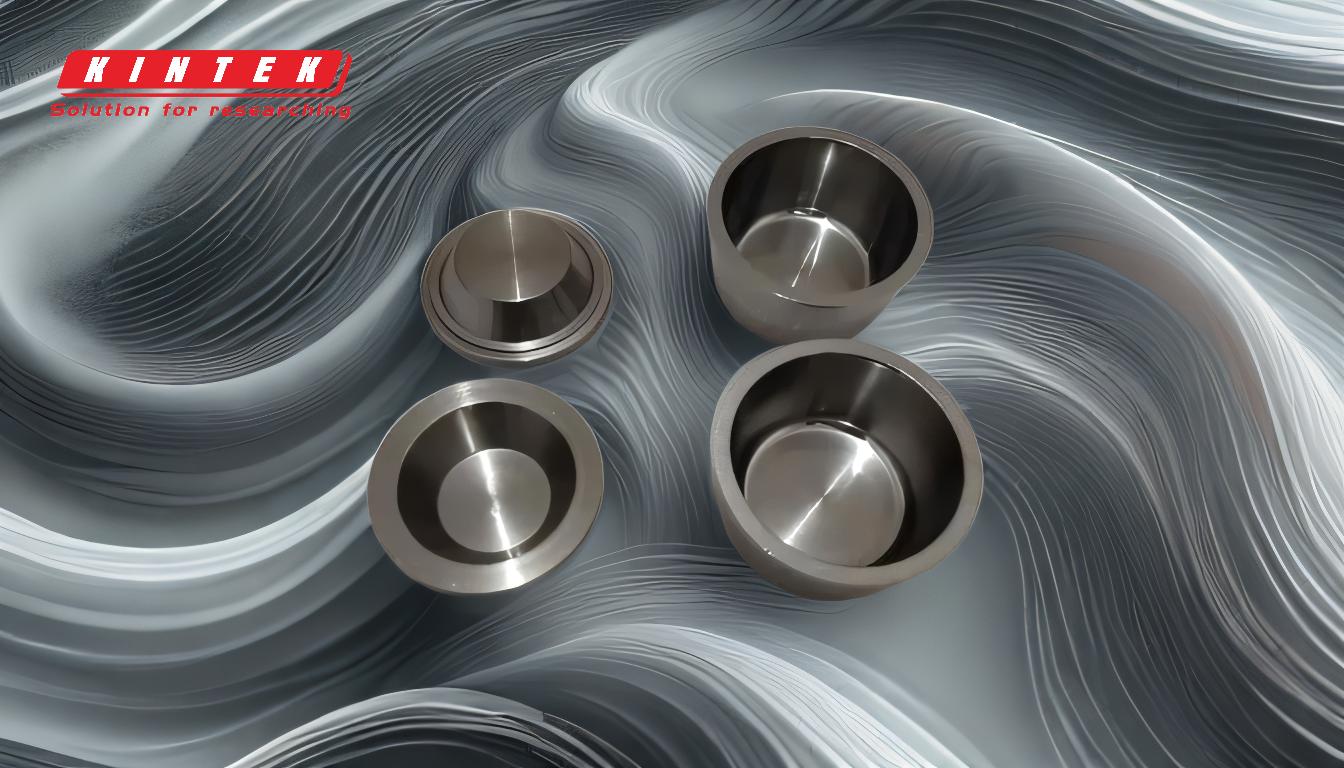
-
What is Sputter Deposition?
- Sputter deposition is a PVD process where a target material is bombarded with high-energy ions (usually argon ions) in a vacuum chamber. This bombardment ejects atoms from the target, which then travel through the vacuum and deposit onto a substrate, forming a thin film.
- The process is highly controllable, allowing for precise thickness and composition of the deposited film.
-
Types of Sputter Deposition
- Magnetron Sputtering: This is a common variant of sputter deposition where a magnetic field is used to enhance the ionization of the gas and increase the efficiency of the process. It is widely used in industries for producing high-quality coatings.
- Reactive Sputtering: In this method, a reactive gas (such as oxygen or nitrogen) is introduced into the vacuum chamber, allowing the formation of compound films (e.g., oxides or nitrides) on the substrate.
- Ion Beam Sputtering: This technique uses a focused ion beam to sputter the target material, offering even greater control over the deposition process and resulting in extremely pure and uniform films.
-
Applications of Sputter Deposition
- Electronics: Sputter deposition is used to create thin films for semiconductors, integrated circuits, and displays. It is essential for depositing conductive, insulating, and protective layers.
- Decorative Coatings: The process is used to apply durable, aesthetically pleasing coatings on items like watches, jewelry, and automotive trim.
- Optical Coatings: Sputter deposition is employed to produce anti-reflective, reflective, and protective coatings for lenses, mirrors, and other optical components.
- Functional Coatings: It is used to deposit wear-resistant, corrosion-resistant, and low-friction coatings on tools, machine parts, and medical devices.
-
Advantages of Sputter Deposition
- High-Quality Films: The process produces films with excellent adhesion, uniformity, and purity.
- Versatility: It can deposit a wide range of materials, including metals, alloys, ceramics, and compounds.
- Scalability: Sputter deposition can be scaled up for industrial production while maintaining high precision.
-
Comparison to Other PVD Processes
- Thermal Evaporation: While simpler and faster, thermal evaporation is less versatile and produces films with lower adhesion and uniformity compared to sputter deposition.
- Cathodic Arc Deposition: This method is efficient for depositing hard coatings but can produce droplets that affect film quality, unlike sputter deposition, which offers smoother films.
- Electron-Beam PVD: This process is highly precise but requires more complex equipment and is less suitable for large-scale production compared to sputter deposition.
-
Recent Advancements in Sputter Deposition
- High-Power Impulse Magnetron Sputtering (HiPIMS): This advanced technique uses short, high-power pulses to achieve better control over film properties, such as density and adhesion.
- Multi-Layer Deposition: Modern sputtering systems can deposit multiple layers of different materials in a single process, enabling the creation of complex, multi-functional coatings.
In summary, sputter deposition is a prime example of a PVD process, offering versatility, precision, and high-quality results. Its widespread use in industries ranging from electronics to decorative coatings underscores its importance as a key technology in modern manufacturing and materials science.
Summary Table:
Aspect | Details |
---|---|
Process | Bombarding target material with high-energy ions in a vacuum chamber. |
Types | Magnetron Sputtering, Reactive Sputtering, Ion Beam Sputtering. |
Applications | Electronics, Decorative Coatings, Optical Coatings, Functional Coatings. |
Advantages | High-quality films, versatility, scalability. |
Recent Advancements | HiPIMS, Multi-Layer Deposition. |
Discover how sputter deposition can enhance your projects—contact our experts today!