An inert atmosphere in a confined space refers to an environment where reactive gases, particularly oxygen, are replaced with non-reactive gases like nitrogen or carbon dioxide. This process is done to eliminate the risk of fire, explosion, or oxidation, which can damage products or materials within the space. Inert atmospheres are commonly used in industrial settings, laboratories, and furnaces to protect sensitive materials, prevent spoilage, or ensure safety during operations. The choice of inert gas and the method of creating the atmosphere depend on the specific application and the desired outcome, such as preventing combustion or maintaining product integrity.
Key Points Explained:
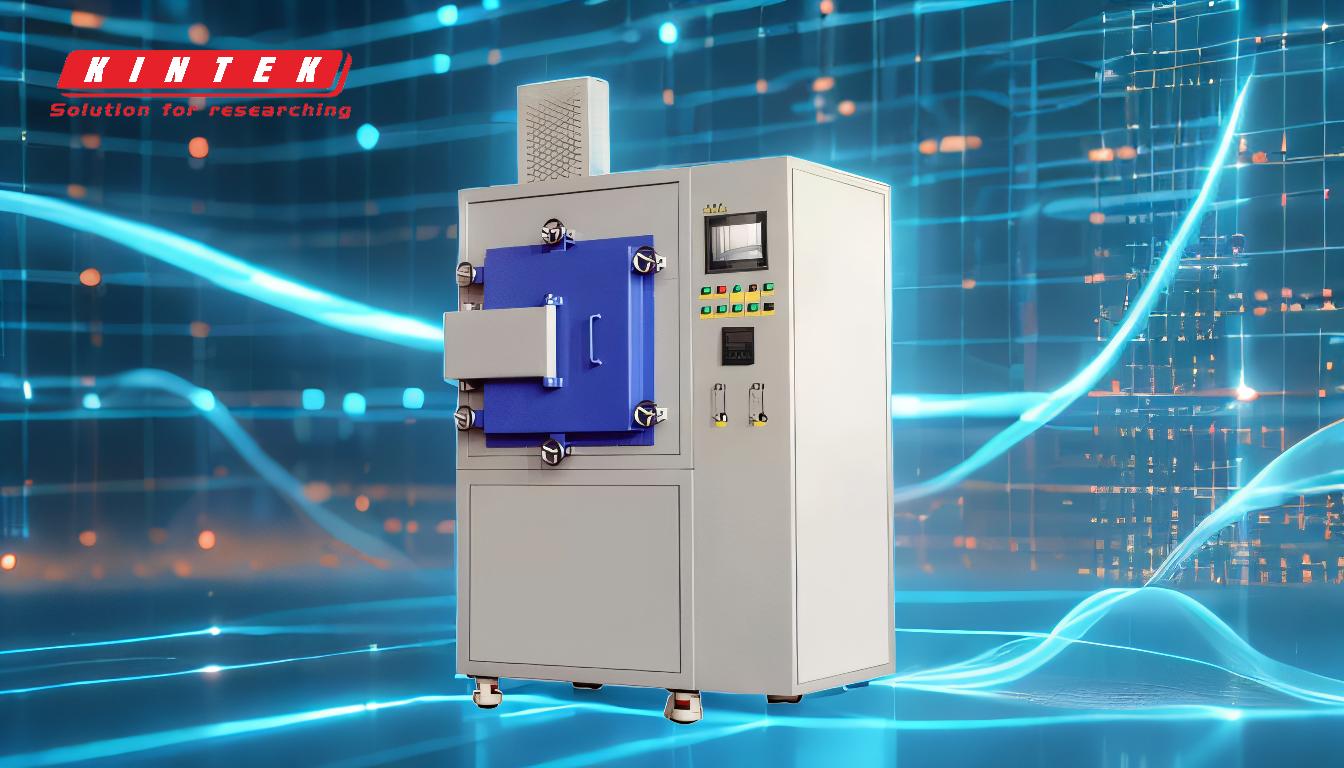
-
Definition of an Inert Atmosphere:
- An inert atmosphere is created by replacing reactive gases, especially oxygen, with non-reactive gases like nitrogen (N₂) or carbon dioxide (CO₂).
- This environment is designed to prevent chemical reactions such as oxidation, combustion, or spoilage.
-
Purpose of an Inert Atmosphere:
- Fire and Explosion Prevention: By removing oxygen, the risk of fire or explosion is significantly reduced, as combustion requires oxygen.
- Oxidation Prevention: Inert atmospheres protect materials, such as metals or organic products, from reacting with oxygen, which can lead to corrosion, spoilage, or degradation.
- Safety in Confined Spaces: Inerting a confined space ensures that hazardous conditions, such as the accumulation of combustible gases, are mitigated.
-
Common Applications:
- Industrial Furnaces: Inert atmospheres are used in heat treatment processes to protect metals and ceramics from oxidation. Nitrogen and argon are commonly used gases.
- Laboratories: Sensitive samples that can be damaged by oxygen exposure are stored or processed in inert atmospheres.
- Food Preservation: Inert gases are used to extend the shelf life of perishable products by preventing oxidation and spoilage.
- Organic Fertilizer Storage: Inerting prevents self-heating and spontaneous combustion of organic materials.
-
Methods of Creating an Inert Atmosphere:
- Gas Purging: Reactive gases are displaced by flushing the confined space with inert gases like nitrogen or argon.
- Vacuum and Gas Replacement: In some cases, a vacuum is first created using a pump, and then inert gas is introduced to fill the space, ensuring minimal oxygen presence.
- Continuous Monitoring: Maintaining an inert atmosphere often requires continuous monitoring and adjustment of gas levels to ensure safety and effectiveness.
-
Key Considerations:
- Gas Selection: The choice of inert gas depends on the application. Nitrogen is widely used due to its cost-effectiveness and non-reactivity, while argon is preferred for high-temperature processes.
- Safety Protocols: Understanding why a space has been inerted is crucial for safe entry and operation. For example, reintroducing oxygen into a space with organic materials could create a fire hazard.
- Equipment Requirements: Specialized equipment, such as inert atmosphere furnaces, may be required to maintain precise control over temperature and gas composition.
-
Benefits of an Inert Atmosphere:
- Enhanced Safety: Reduces the risk of fire, explosion, and hazardous chemical reactions.
- Product Protection: Prevents spoilage, corrosion, or degradation of sensitive materials.
- Process Efficiency: Improves the quality and consistency of industrial processes, such as heat treatment or sample analysis.
By understanding the concept of an inert atmosphere and its applications, equipment and consumable purchasers can make informed decisions about the gases and systems required for their specific needs. This knowledge also ensures compliance with safety standards and enhances operational efficiency.
Summary Table:
Aspect | Details |
---|---|
Definition | Replaces reactive gases (e.g., oxygen) with non-reactive gases like N₂ or CO₂. |
Purpose | Prevents fire, explosion, oxidation, and spoilage. |
Applications | Industrial furnaces, labs, food preservation, organic fertilizer storage. |
Methods | Gas purging, vacuum and gas replacement, continuous monitoring. |
Key Considerations | Gas selection, safety protocols, equipment requirements. |
Benefits | Enhanced safety, product protection, improved process efficiency. |
Need help creating an inert atmosphere for your application? Contact our experts today to get started!