Autoclave testing is a critical process used to validate the effectiveness of an autoclave in sterilizing equipment and materials. It ensures that the autoclave operates correctly, reaching the necessary temperature, pressure, and duration to eliminate harmful microorganisms. This process is essential in microbiological and biomedical laboratories, healthcare facilities, and industries where sterilization is required. Autoclave testing involves verifying that the autoclave can consistently achieve the conditions needed for sterilization, such as 121°C (250°F) at 15-20 minutes under high pressure. It also ensures compliance with safety and quality standards, confirming that biological waste and equipment are decontaminated effectively.
Key Points Explained:
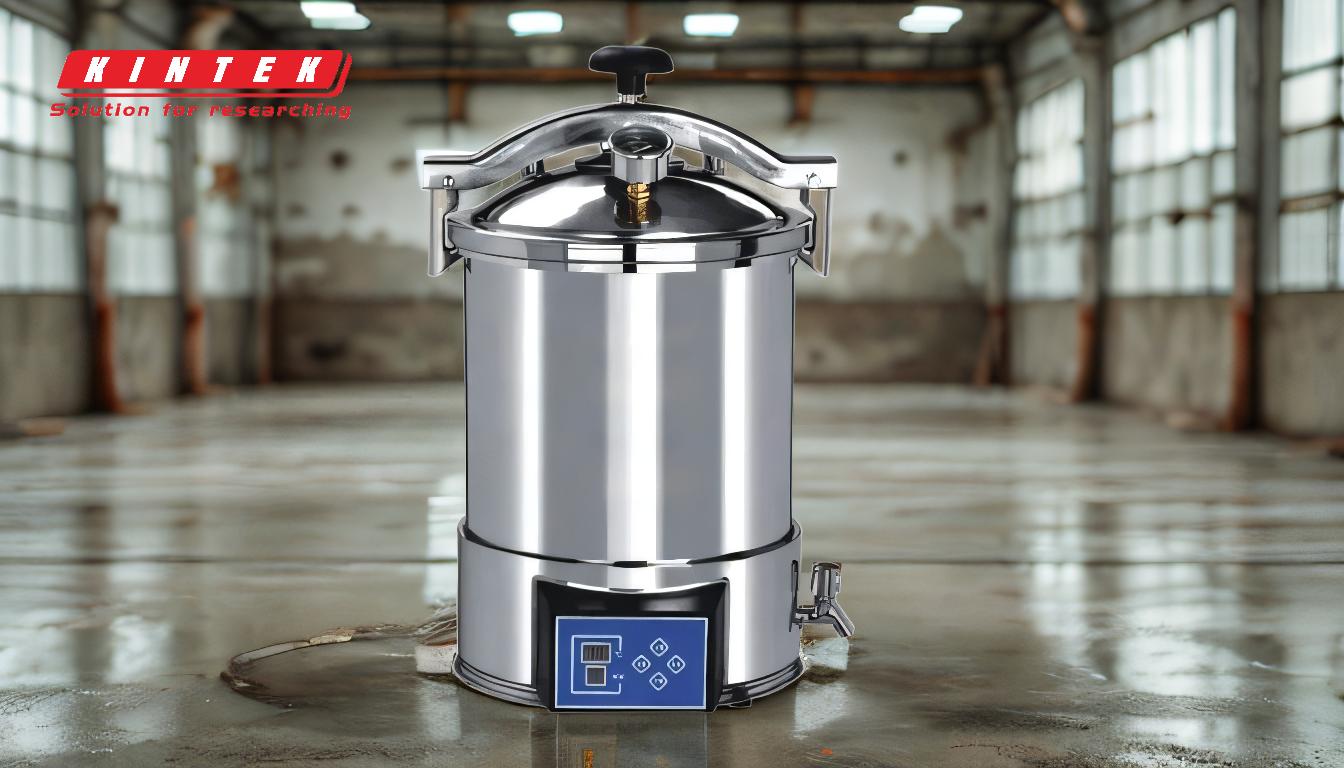
-
Definition and Purpose of Autoclave Testing:
- Autoclave testing is the process of validating whether an autoclave can achieve the required sterilization conditions, including temperature, pressure, and time.
- Its primary purpose is to ensure that the autoclave effectively kills microorganisms, such as bacteria, viruses, and spores, to meet safety and regulatory standards.
- This testing is crucial in environments like laboratories, hospitals, and pharmaceutical facilities, where sterilization is critical to prevent contamination and ensure safety.
-
How Autoclave Testing Works:
- Temperature and Pressure Validation: Autoclave testing verifies that the machine reaches and maintains the recommended temperature (typically 121°C or 250°F) and pressure for the required duration (15-20 minutes).
- Load Testing: Different types of loads (e.g., liquids, solids, or mixed materials) may require adjustments in sterilization time. Testing ensures that all items in the load are uniformly sterilized.
- Biological Indicators: These are often used in testing to confirm sterilization. Biological indicators contain heat-resistant spores that are killed only when the autoclave reaches the correct conditions.
- Chemical Indicators: These are used to monitor whether the autoclave has reached the necessary temperature and pressure. They change color when the required conditions are met.
-
Steps in Autoclave Testing:
- Preparation: Load the autoclave with materials to be sterilized, ensuring proper placement to allow steam penetration.
- Cycle Selection: Choose the appropriate sterilization program based on the load type (e.g., liquids, solids, or biohazardous waste).
- Monitoring: Use biological and chemical indicators to track the sterilization process.
- Cooling and Drying: After the sterilization cycle, allow the load to cool and dry if necessary.
- Verification: Check the indicators to confirm that the sterilization conditions were met.
-
Importance of Autoclave Testing:
- Safety Compliance: Ensures that the autoclave meets regulatory and safety standards, particularly in handling biohazardous waste.
- Sterilization Efficacy: Confirms that the autoclave can effectively kill microorganisms, preventing contamination in sensitive environments.
- Equipment Longevity: Regular testing helps identify potential issues with the autoclave, ensuring its proper functioning and extending its lifespan.
- Quality Assurance: Provides confidence that sterilization processes are reliable and consistent, which is critical in research, healthcare, and manufacturing.
-
Challenges in Autoclave Testing:
- Variable Loads: Different materials and load sizes may require adjustments in sterilization time and temperature, making testing more complex.
- Indicator Reliability: Biological and chemical indicators must be accurate and reliable to ensure valid test results.
- Maintenance Requirements: Regular testing requires proper maintenance of the autoclave to prevent malfunctions and ensure consistent performance.
-
Applications of Autoclave Testing:
- Laboratories: Used to sterilize lab equipment, media, and biohazardous waste.
- Healthcare: Ensures the sterilization of surgical instruments and medical devices.
- Pharmaceuticals: Validates the sterilization of equipment and materials used in drug manufacturing.
- Food Industry: Used to sterilize equipment and packaging materials to prevent contamination.
In summary, autoclave testing is a vital process that ensures the effectiveness and reliability of autoclaves in sterilizing equipment and materials. By validating temperature, pressure, and sterilization time, it guarantees compliance with safety standards and prevents contamination in critical environments. Regular testing and maintenance are essential to maintain the autoclave's performance and ensure consistent, high-quality sterilization.
Summary Table:
Key Aspect | Details |
---|---|
Purpose | Validates autoclave effectiveness in killing microorganisms. |
Conditions | 121°C (250°F) at 15-20 minutes under high pressure. |
Indicators | Biological and chemical indicators confirm sterilization. |
Applications | Labs, healthcare, pharmaceuticals, and food industry. |
Challenges | Variable loads, indicator reliability, and maintenance requirements. |
Importance | Ensures safety compliance, sterilization efficacy, and equipment longevity. |
Ensure your autoclave meets safety standards—contact us today for expert guidance!