When comparing ceramic and diamond coatings, the choice depends on the specific application requirements. Diamond coatings are known for their exceptional hardness, thermal conductivity, and chemical inertness, making them ideal for high-performance applications like cutting tools and wear-resistant surfaces. Ceramic coatings, on the other hand, offer good hardness, thermal stability, and corrosion resistance, often at a lower cost. Diamond coatings can be tailored for specific properties by adjusting deposition parameters, but they are generally more expensive and complex to produce. Ceramic coatings are more versatile and cost-effective for a broader range of applications. The decision ultimately hinges on balancing performance needs, budget, and application specifics.
Key Points Explained:
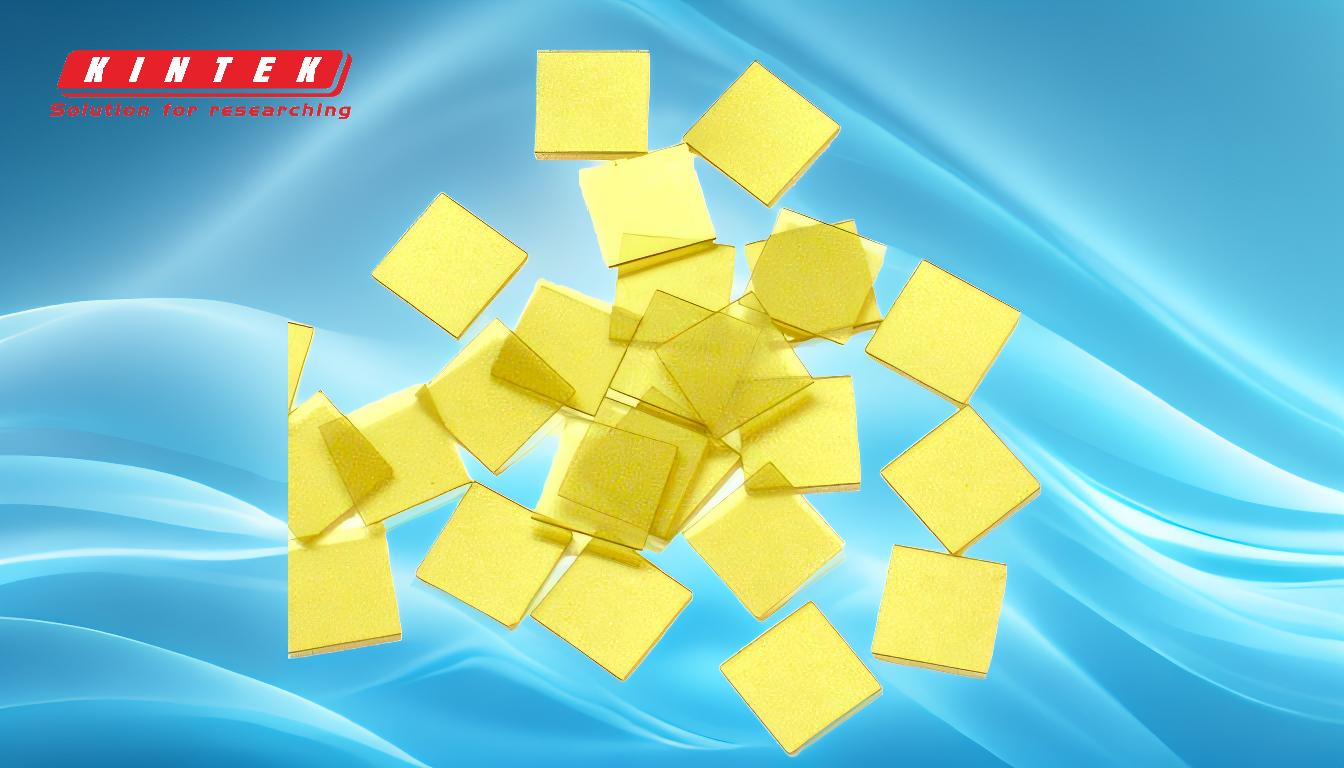
-
Hardness and Wear Resistance:
- Diamond coatings are among the hardest materials known, making them superior for applications requiring extreme wear resistance, such as cutting tools and industrial machinery.
- Ceramic coatings also offer high hardness but generally fall short of diamond's performance in terms of wear resistance.
-
Thermal Conductivity:
- Diamond coatings have excellent thermal conductivity, which is crucial for applications where heat dissipation is critical, such as in electronic components or high-speed machining.
- Ceramic coatings typically have lower thermal conductivity, which can be a limitation in high-temperature environments.
-
Chemical Inertness:
- Diamond coatings are chemically inert, making them resistant to corrosion and chemical attack, ideal for harsh environments like chemical processing equipment.
- Ceramic coatings also offer good chemical resistance but may not match the inertness of diamond in highly corrosive conditions.
-
Cost and Manufacturing Complexity:
- Diamond coatings are more expensive and complex to produce, requiring precise control over deposition parameters and gas phase composition.
- Ceramic coatings are generally more cost-effective and easier to manufacture, making them suitable for a wider range of applications where extreme performance is not required.
-
Versatility:
- Ceramic coatings are more versatile, offering a range of properties that can be tailored for various applications, from thermal barriers to corrosion protection.
- Diamond coatings, while superior in specific high-performance applications, are less versatile due to their higher cost and manufacturing complexity.
-
Application-Specific Considerations:
- For high-performance applications like cutting tools, aerospace components, or electronic devices, diamond coatings may be the better choice due to their superior hardness and thermal conductivity.
- For more general-purpose applications, such as automotive parts or consumer goods, ceramic coatings may be more appropriate due to their balance of performance, cost, and ease of manufacturing.
In summary, the choice between ceramic and diamond coatings depends on the specific requirements of the application, including performance needs, budget constraints, and manufacturing considerations. Diamond coatings excel in high-performance, demanding environments, while ceramic coatings offer a more cost-effective and versatile solution for a broader range of applications.
Summary Table:
Property | Diamond Coatings | Ceramic Coatings |
---|---|---|
Hardness | Extremely high, ideal for wear resistance | High, but less than diamond |
Thermal Conductivity | Excellent, suitable for heat dissipation | Lower, may limit high-temperature performance |
Chemical Inertness | Highly resistant to corrosion and chemical attack | Good resistance, but less effective in highly corrosive environments |
Cost | Expensive and complex to produce | Cost-effective and easier to manufacture |
Versatility | Limited to high-performance applications | Versatile, suitable for a wide range of applications |
Best Applications | Cutting tools, aerospace components, electronic devices | Automotive parts, consumer goods, general-purpose applications |
Need help choosing between ceramic and diamond coatings? Contact our experts today for tailored advice!