Biochar is a carbon-rich material produced through the pyrolysis of organic biomass in the absence of oxygen. It is typically obtained during slow pyrolysis, where biomass is heated at lower temperatures (around 400°C) for several hours, resulting in biochar and bio-gas. The process involves drying and mechanically preparing the biomass before pyrolysis. Biochar is lightweight, porous, and has the ability to absorb contaminants, nutrients, water, gases, and odors. Its properties depend on factors like the type of biomass, pyrolysis temperature, residence time, and conditioning. It is used for carbon sequestration, as a fossil coal substitute, and as an additive in materials like concrete and plastics.
Key Points Explained:
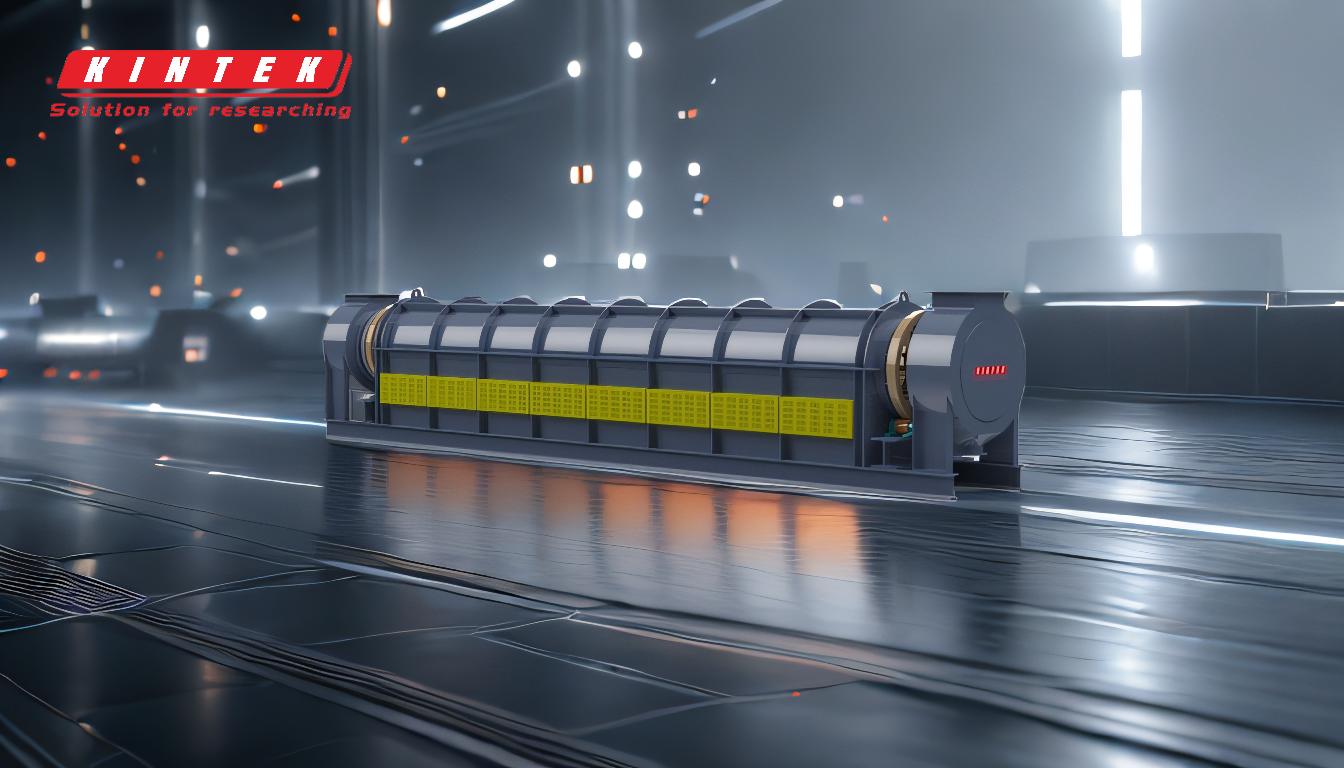
-
Definition and Production Process:
- Biochar is a carbon-rich, black material produced through pyrolysis, a process where organic biomass is heated in the absence of oxygen.
- It is primarily obtained during slow pyrolysis, which involves lower temperatures (around 400°C) and longer residence times (several hours).
- The biomass is first dried and mechanically comminuted (reduced in size) before undergoing pyrolytic decomposition.
-
Pyrolysis Conditions:
- Pyrolysis occurs at temperatures ranging from 300-900°C, depending on the process type (slow, fast, or gasification).
- Slow pyrolysis, the most common method for biochar production, emphasizes lower temperatures and longer processing times, maximizing biochar yield.
- The energy required for the process can be self-sustained by combusting the gaseous byproducts (bio-gas) generated during pyrolysis.
-
Properties of Biochar:
- Biochar is lightweight and porous, making it highly effective for sorbing contaminants, nutrients, water, gases, and odors.
- Its properties are influenced by factors such as:
- The type of biomass used (e.g., wood, agricultural residues, sludge).
- Pyrolysis temperature and residence time.
- Post-pyrolysis conditioning.
-
Applications of Biochar:
- Carbon Sequestration: Biochar is stable and can store carbon for hundreds to thousands of years, helping mitigate climate change.
- Fossil Coal Replacement: It can be used as a renewable alternative to fossil coal in energy production.
- Additive in Materials: Biochar is incorporated into materials like concrete and plastics to enhance their properties.
- Soil Amendment: It improves soil fertility, water retention, and nutrient availability in agricultural applications.
-
Distinction Between Biochar and Char:
- Biochar is typically made from virgin (clean) biomass, while char can also be produced from contaminated materials like treated wood or sludge.
- Both materials share similar properties but differ in their source materials and potential applications.
-
Factors Influencing Biochar Quality:
- The quality and functionality of biochar depend on:
- Biomass Type: Different feedstocks (e.g., wood, crop residues) yield biochar with varying properties.
- Pyrolysis Technology: Slow, fast, or gasification methods produce biochar with distinct characteristics.
- Temperature and Residence Time: Higher temperatures and shorter residence times reduce biochar yield but may enhance certain properties.
- Conditioning: Post-pyrolysis treatments can further refine biochar for specific applications.
- The quality and functionality of biochar depend on:
By understanding these key points, purchasers of equipment and consumables can make informed decisions about the production and use of biochar, ensuring optimal results for their specific needs.
Summary Table:
Aspect | Details |
---|---|
Definition | Carbon-rich material from pyrolysis of organic biomass in oxygen-free conditions. |
Production Process | Slow pyrolysis at ~400°C, drying, and mechanical preparation of biomass. |
Properties | Lightweight, porous, absorbs contaminants, nutrients, water, gases, odors. |
Applications | Carbon sequestration, fossil coal substitute, additive in materials, soil amendment. |
Key Factors | Biomass type, pyrolysis temperature, residence time, conditioning. |
Ready to explore biochar solutions for your needs? Contact us today to learn more!