Chemical deposition techniques, particularly Chemical Vapor Deposition (CVD), are advanced processes used to create thin films and coatings on substrates. These techniques involve the transport of gaseous reactants to a substrate surface, where chemical reactions occur to form a solid film. The process is highly versatile and can be tailored to produce materials with specific properties, making it essential in industries such as semiconductors, optics, and protective coatings. CVD methods vary based on pressure, temperature, and the use of additional energy sources like plasma or lasers, allowing for precise control over film characteristics.
Key Points Explained:
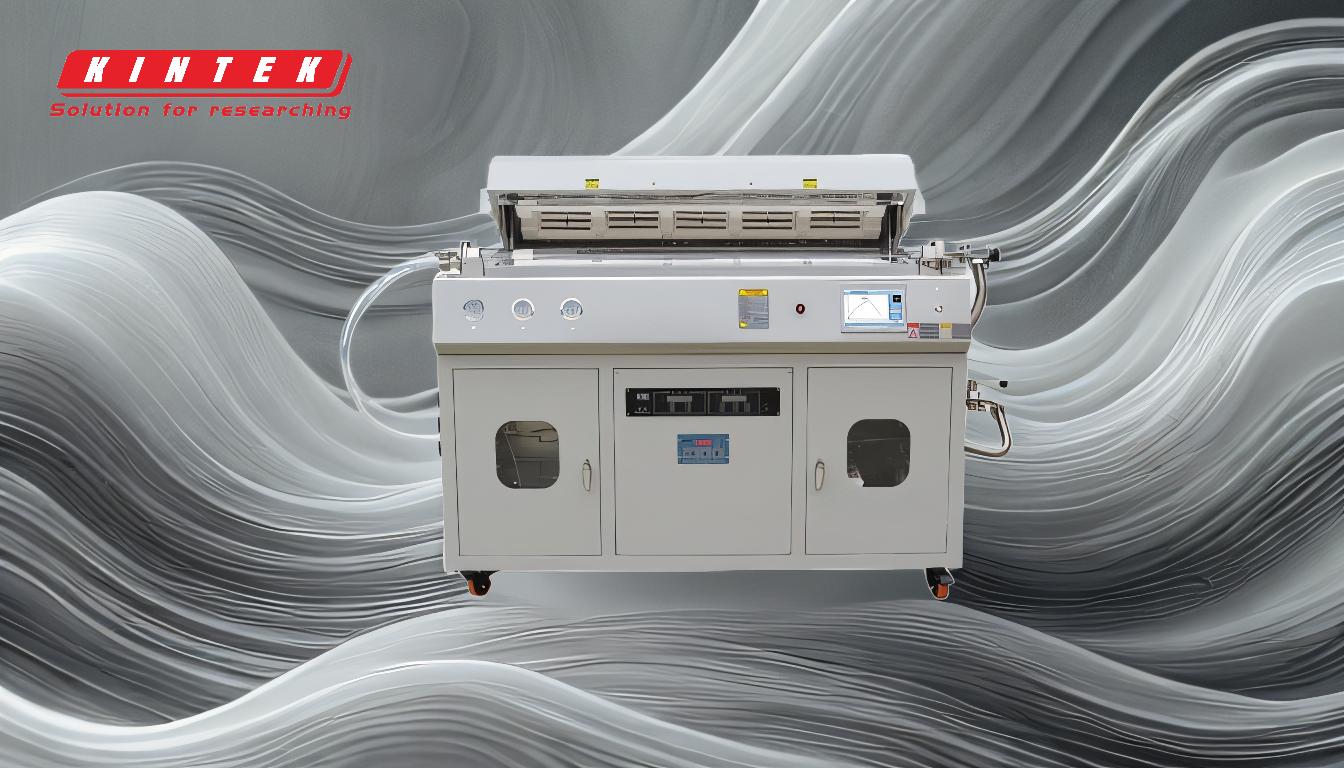
-
Fundamental Steps of CVD:
- Transport of Reactants: Gaseous reactants are transported to the reaction chamber via convection or diffusion.
- Gas Phase Reactions: Chemical reactions in the gas phase produce reactive species and by-products.
- Surface Adsorption: Reactants adsorb onto the substrate surface, either chemically or physically.
- Surface Reactions: Heterogeneous reactions on the substrate surface lead to the formation of a solid film.
- Desorption and Removal: Volatile by-products desorb and are removed from the reactor.
-
Types of CVD Methods:
- Atmospheric Pressure CVD (APCVD): Operates at atmospheric pressure, suitable for large-scale production.
- Low Pressure CVD (LPCVD): Conducted at reduced pressures, offering better film uniformity and step coverage.
- Ultrahigh Vacuum CVD (UHVCVD): Performed under ultrahigh vacuum conditions, ideal for high-purity films.
- Laser Induced CVD (LICVD): Uses laser energy to initiate reactions, enabling localized deposition.
- Metal-Organic CVD (MOCVD): Employs metal-organic precursors, commonly used for compound semiconductors.
- Plasma Enhanced CVD (PECVD): Utilizes plasma to enhance reaction rates at lower temperatures.
-
Chemical Transport Method:
- Involves the transport of a volatile compound to the substrate, where it decomposes or reacts to form the desired film.
-
Pyrolysis Method:
- A thermal decomposition process where a precursor vapor decomposes into atoms and molecules upon heating, depositing the film on the substrate.
-
Synthesis Reaction Method:
- Involves chemical reactions between different gaseous species to form the film, often requiring precise control of reactant concentrations and temperatures.
-
Sputtering as a Deposition Technique:
- Although not a CVD method, sputtering is another deposition technique where atoms are ejected from a target material and deposited onto a substrate. This process is typically conducted in a vacuum and is used for creating thin films of metals and alloys.
-
Applications of CVD:
- Semiconductors: CVD is crucial for depositing thin films in semiconductor device fabrication.
- Optics: Used to create anti-reflective coatings and other optical films.
- Protective Coatings: Provides wear-resistant and corrosion-resistant coatings for various materials.
By understanding these key points, one can appreciate the complexity and versatility of chemical deposition techniques, particularly CVD, in modern material science and engineering.
Summary Table:
Aspect | Details |
---|---|
Fundamental Steps | Transport of reactants, gas phase reactions, surface adsorption, reactions, desorption. |
Types of CVD Methods | APCVD, LPCVD, UHVCVD, LICVD, MOCVD, PECVD. |
Key Techniques | Chemical transport, pyrolysis, synthesis reaction, sputtering. |
Applications | Semiconductors, optics, protective coatings. |
Discover how chemical deposition techniques can transform your projects—contact us today!