Chemical vapor deposition (CVD) is a widely used method for synthesizing carbon nanotubes (CNTs), offering structural controllability and cost-effectiveness. The process involves thermal treatments, gas-phase rearrangement, and catalyst deposition, typically using methane as a carbon precursor and a metal catalyst like copper. It operates at high temperatures (around 1000 °C), where carbon precursors decompose and form carbon species that nucleate into CNTs. CVD is the dominant commercial method for CNT production, surpassing traditional techniques like laser ablation and arc discharge. However, the process requires careful management of material and energy consumption to minimize environmental impacts, such as greenhouse gas emissions and ecotoxicity.
Key Points Explained:
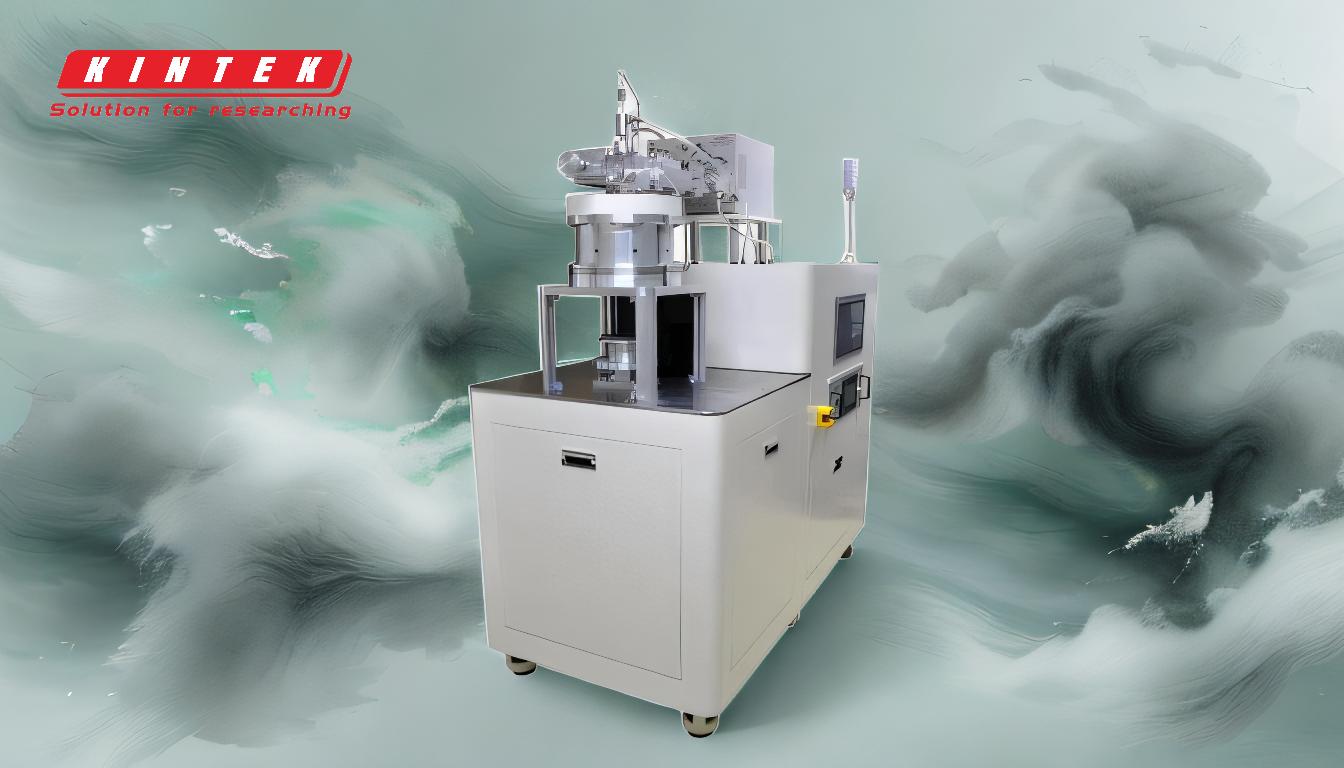
-
What is Chemical Vapor Deposition (CVD)?
Chemical vapor deposition is a process used to fabricate thin films and coatings, including carbon nanotubes (CNTs). It involves the decomposition of carbon precursors (e.g., methane) on a catalyst surface at high temperatures, leading to the formation of carbon species that nucleate into CNTs. This method is highly versatile and applicable across various industries, including electronics, materials science, and energy. -
How CVD Works for CNT Synthesis
- Precursor and Catalyst: Methane is commonly used as the carbon precursor, while metals like copper or nickel serve as catalysts.
- High-Temperature Process: The reaction occurs at temperatures around 1000 °C, where the carbon precursor adsorbs onto the catalyst surface, decomposes, and forms carbon species.
- Nucleation and Growth: These carbon species nucleate and grow into CNTs, with the catalyst playing a crucial role in controlling the structure and quality of the nanotubes.
-
Advantages of CVD for CNT Production
- Structural Controllability: CVD allows precise control over the diameter, length, and alignment of CNTs, making it suitable for various applications.
- Cost-Effectiveness: Compared to traditional methods like laser ablation and arc discharge, CVD is more scalable and economically viable for large-scale production.
- Versatility: CVD can be adapted to use different carbon precursors and catalysts, enabling the synthesis of CNTs with tailored properties.
-
Environmental and Economic Considerations
- Material and Energy Consumption: The synthesis process requires significant energy and materials, which can lead to environmental impacts such as greenhouse gas emissions.
- Ecotoxicity: The life cycle ecotoxicity of CNTs is influenced by the synthesis process, emphasizing the need for sustainable practices, such as using green feedstocks (e.g., carbon dioxide or methane pyrolysis).
- Waste Management: Efficient use of catalysts and precursors can reduce waste and improve the overall sustainability of the process.
-
Comparison with Traditional Methods
- Laser Ablation and Arc Discharge: These methods were historically used for CNT synthesis but are less cost-effective and scalable compared to CVD.
- Emerging Techniques: New approaches, such as using carbon dioxide captured by electrolysis or methane pyrolysis, aim to enhance sustainability and reduce environmental impacts.
-
Applications of CVD-Synthesized CNTs
- Electronics: CNTs are used in transistors, sensors, and conductive films due to their excellent electrical properties.
- Energy Storage: CNTs are incorporated into batteries and supercapacitors to improve performance.
- Composites: CVD-synthesized CNTs are used to reinforce polymers, ceramics, and metals, enhancing their mechanical and thermal properties.
-
Challenges and Future Directions
- Scalability: While CVD is scalable, further optimization is needed to reduce costs and improve yield.
- Environmental Impact: Developing greener synthesis methods and minimizing energy consumption are critical for sustainable CNT production.
- Quality Control: Ensuring consistent quality and properties of CNTs remains a challenge, particularly for high-performance applications.
In summary, chemical vapor deposition is a highly effective and versatile method for synthesizing carbon nanotubes, offering structural controllability and cost-effectiveness. However, addressing environmental and economic challenges is essential for the sustainable growth of this technology.
Summary Table:
Aspect | Details |
---|---|
Process | Decomposition of carbon precursors (e.g., methane) on a catalyst surface. |
Temperature | Operates at ~1000 °C. |
Key Components | Methane (precursor), copper/nickel (catalyst). |
Advantages | Structural controllability, cost-effectiveness, versatility. |
Applications | Electronics, energy storage, composites. |
Challenges | Scalability, environmental impact, quality control. |
Discover how CVD can revolutionize your CNT production—contact our experts today!