Chemical Vapor Deposition (CVD) in a vacuum is a sophisticated process used to deposit thin, high-quality films or coatings onto a substrate. It involves introducing gaseous precursor materials into a vacuum chamber, where they undergo chemical reactions, decompose, and form a solid layer on the substrate. The vacuum environment ensures controlled conditions, such as low pressure and precise temperature, which are critical for achieving uniform and high-performance coatings. CVD is widely used in industries like semiconductors, optics, and aerospace due to its ability to produce durable, precise, and high-purity materials.
Key Points Explained:
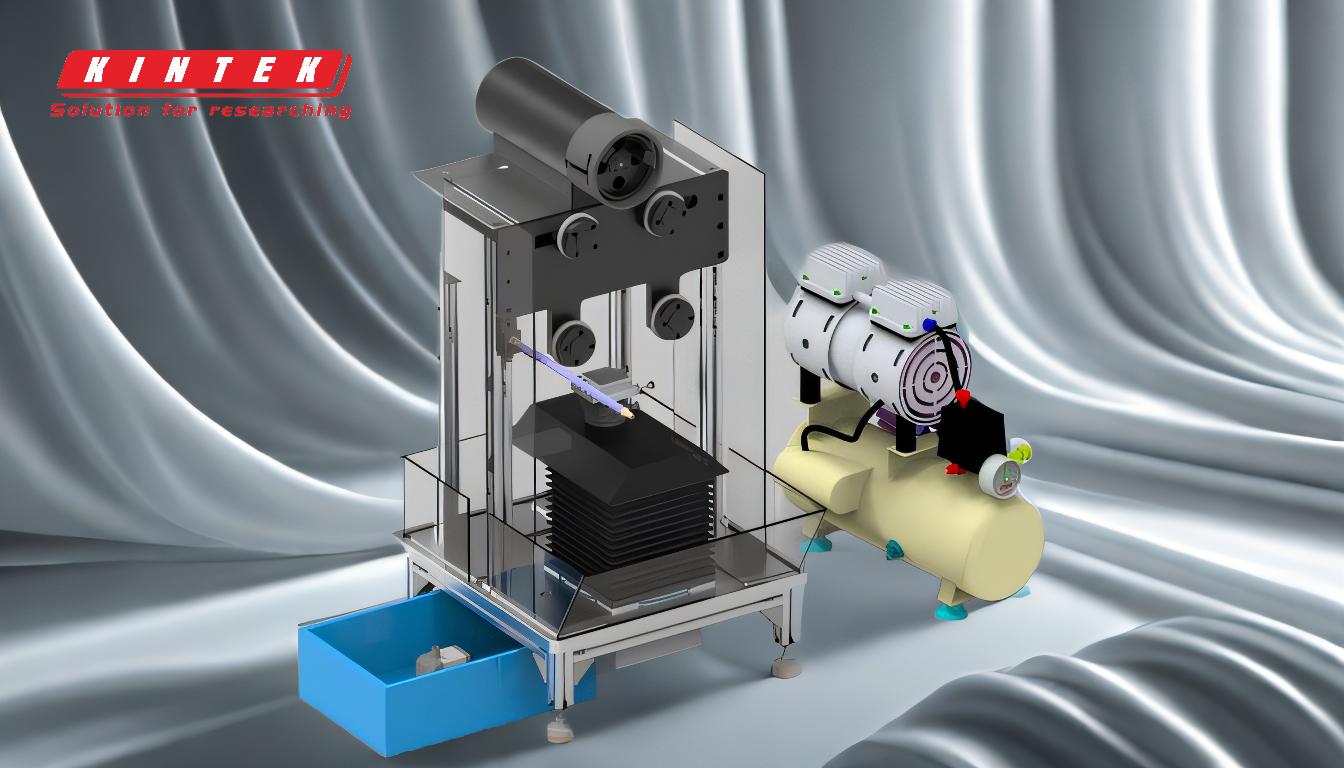
-
Definition and Purpose of CVD in a Vacuum:
- Chemical Vapor Deposition (CVD) is a process where gaseous precursors chemically react or decompose on a substrate to form a solid, thin film.
- The vacuum environment is essential for maintaining controlled conditions, such as low pressure and precise temperature, which are critical for achieving high-quality, uniform coatings.
- This method is widely used in industries like semiconductors, optics, and aerospace for creating durable, precise, and high-purity materials.
-
Key Components of the CVD Process:
- Precursor Gases: Volatile materials that are vaporized and introduced into the reaction chamber. These gases are the source of the deposition material.
- Substrate: The surface on which the thin film is deposited. It can be made of various materials, such as silicon wafers, metals, or ceramics.
- Vacuum Chamber: A sealed environment where the process occurs. The vacuum ensures minimal contamination and precise control over reaction conditions.
- Heat Source: High temperatures are often required to vaporize the precursors and facilitate chemical reactions.
- By-product Removal System: Volatile by-products generated during the process are removed from the chamber to maintain the purity of the deposited layer.
-
Mechanism of CVD in a Vacuum:
- The precursor gases are introduced into the vacuum chamber, where they are vaporized and transported to the substrate.
- Chemical reactions, such as decomposition or surface reactions, occur on the substrate, leading to the formation of a solid layer.
- The vacuum environment reduces the presence of unwanted contaminants and allows for precise control over the deposition process.
- The resulting thin film is typically dense, uniform, and adheres strongly to the substrate.
-
Types of CVD Processes:
- Atmospheric Pressure CVD (APCVD): Operates at normal atmospheric pressure, suitable for high-throughput applications.
- Low-Pressure CVD (LPCVD): Conducted under reduced pressure, providing better uniformity and control over film properties.
- Plasma-Enhanced CVD (PECVD): Uses plasma to enhance chemical reactions, allowing for lower temperatures and faster deposition rates.
- Laser-Assisted CVD (LACVD): Employs laser irradiation to locally heat the substrate, enabling precise and localized deposition.
- Metal-Organic CVD (MOCVD): Uses metal-organic compounds as precursors, often employed in the production of semiconductor materials.
-
Advantages of CVD in a Vacuum:
- High-Quality Films: Produces dense, uniform, and high-purity coatings with excellent adhesion to the substrate.
- Versatility: Can deposit a wide range of materials, including metals, ceramics, and semiconductors.
- Precision: Allows for precise control over film thickness and composition, making it ideal for advanced applications.
- Scalability: Suitable for both small-scale research and large-scale industrial production.
-
Applications of CVD in a Vacuum:
- Semiconductor Industry: Used to deposit thin films for integrated circuits, transistors, and other electronic components.
- Optics: Produces anti-reflective coatings, mirrors, and lenses with high optical performance.
- Aerospace: Creates protective coatings for turbine blades and other high-stress components.
- Medical Devices: Deposits biocompatible coatings on implants and surgical tools.
- Energy: Used in the production of solar cells and fuel cells.
-
Challenges and Considerations:
- Cost: CVD equipment and precursor materials can be expensive, making the process less economical for some applications.
- Complexity: Requires precise control over process parameters, such as temperature, pressure, and gas flow rates.
- Safety: Handling volatile and potentially hazardous precursor gases necessitates strict safety protocols.
- Environmental Impact: Some precursor materials and by-products may be harmful, requiring proper disposal and mitigation measures.
By understanding these key points, a purchaser of equipment or consumables can make informed decisions about implementing CVD processes, ensuring they meet specific application requirements and industry standards.
Summary Table:
Key Aspect | Details |
---|---|
Definition | Deposits thin films via chemical reactions of gaseous precursors in a vacuum. |
Key Components | Precursor gases, substrate, vacuum chamber, heat source, by-product removal. |
Mechanism | Gases react on the substrate under controlled vacuum conditions. |
Types of CVD | APCVD, LPCVD, PECVD, LACVD, MOCVD. |
Advantages | High-quality, versatile, precise, and scalable. |
Applications | Semiconductors, optics, aerospace, medical devices, energy. |
Challenges | High cost, complexity, safety concerns, environmental impact. |
Discover how CVD in a vacuum can elevate your production—contact our experts today!