Chemical vapor deposition (CVD) is a sophisticated process used to deposit thin films of materials onto substrates through chemical reactions in the vapor phase. It is widely applied in industries such as electronics, cutting tools, and solar cell manufacturing, where precise and high-quality coatings are essential. The process involves the activation of gaseous reactants, which then undergo a chemical reaction to form a solid deposit on a substrate. This technique requires a high level of skill and is capable of producing coatings on various materials, including glass, metals, and ceramics. CVD is particularly valued for its ability to create uniform and durable thin films, making it indispensable in advanced manufacturing and material science.
Key Points Explained:
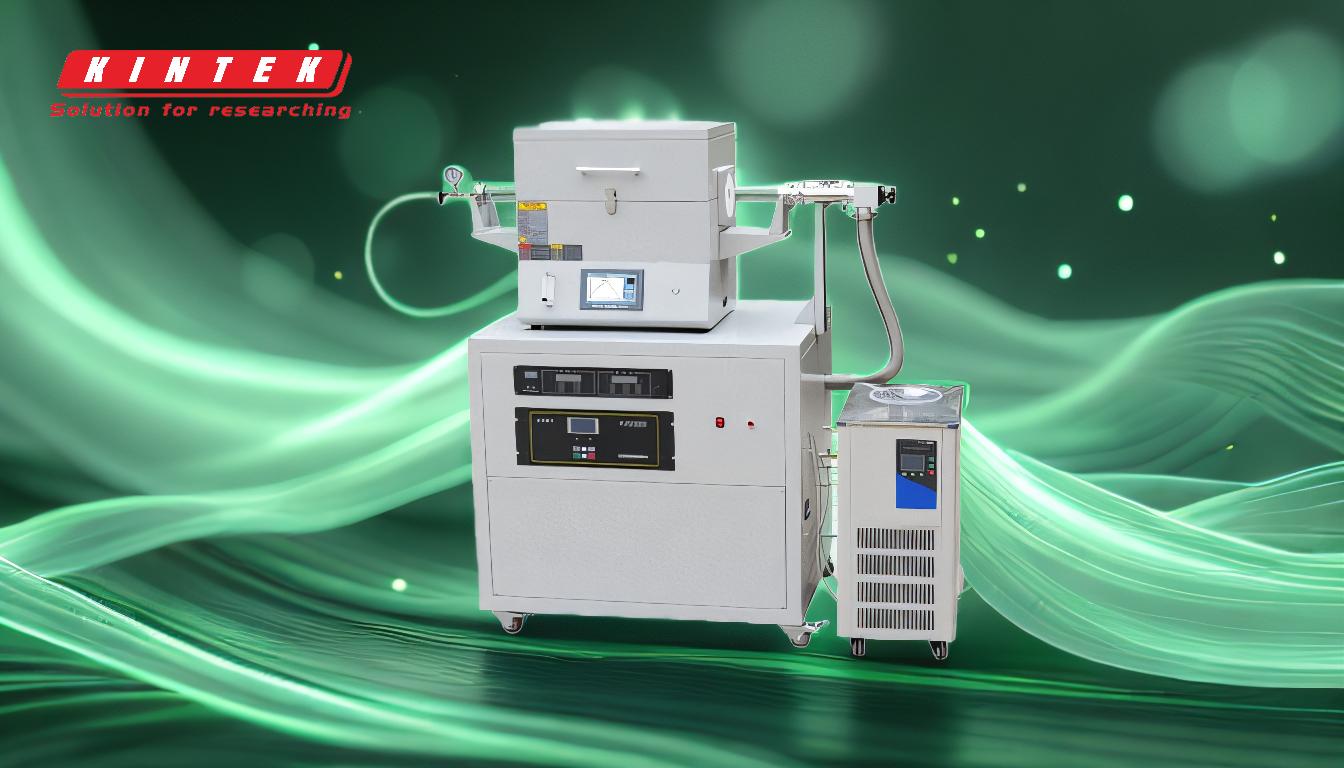
-
Definition and Purpose of Chemical Vapor Deposition (CVD):
- CVD is a process used to deposit thin films of materials onto a substrate through chemical reactions in the vapor phase. This method is essential in industries where precise and high-quality coatings are required, such as in electronics, cutting tools, and solar cell manufacturing. chemical vapor deposition is particularly valued for its ability to create uniform and durable thin films, making it indispensable in advanced manufacturing and material science.
-
Industries and Applications:
- Electronics: CVD is used to deposit thin films on semiconductors, which are critical for the fabrication of electronic devices.
- Cutting Tools: The process is employed to coat cutting tools with materials that prevent corrosion and wear, enhancing their durability and performance.
- Solar Cells: In the manufacture of thin-film solar cells, CVD is used to deposit photovoltaic materials on a substrate, which is essential for converting sunlight into electricity.
-
Materials and Substrates:
- CVD can be used to deposit thin films on a wide range of base materials, including glass, metals, and ceramics. This versatility makes it a valuable technique in various industries.
- The process requires a high level of skill to ensure the quality and uniformity of the deposited films.
-
Chemical Transport Method:
- In the chemical transport method, the substance constituting the thin film reacts with another solid or liquid substance in the source area to generate gas. This gas is then transported to the growth area at a certain temperature, where the required material is generated through the opposite thermal reaction.
- The forward reaction is the thermal reaction of the transport process, and the reverse reaction is the thermal reaction of the crystal growth process.
-
Energy Sources for CVD:
- The energy required for the chemical reaction in CVD can be supplied by various sources, including heat, light, or electric discharge. This flexibility allows for the customization of the process to suit different materials and applications.
-
Historical Use and Evolution:
- Historically, CVD has been used for the fabrication of thin films composed of inorganic materials. Over time, the process has evolved and expanded to include a broader range of materials and applications, reflecting advancements in technology and material science.
In summary, chemical vapor deposition is a versatile and essential process in modern manufacturing and material science. Its ability to produce high-quality, uniform thin films on various substrates makes it a critical technique in industries ranging from electronics to renewable energy. The process's reliance on chemical reactions in the vapor phase, combined with the need for precise control and high skill levels, underscores its importance in producing advanced materials and coatings.
Summary Table:
Aspect | Details |
---|---|
Definition | A process to deposit thin films via chemical reactions in the vapor phase. |
Applications | Electronics, cutting tools, solar cells. |
Materials | Glass, metals, ceramics. |
Energy Sources | Heat, light, electric discharge. |
Key Benefit | Produces uniform, durable thin films for advanced manufacturing. |
Discover how CVD can revolutionize your manufacturing process—contact our experts today!