Chemical vapor deposition (CVD) of metals is a sophisticated process used to deposit thin, high-quality metal layers onto a substrate. This technique involves introducing a gaseous precursor into a reaction chamber, where it undergoes a chemical reaction, often facilitated by heat, plasma, or laser assistance. The resulting metal atoms or molecules are then deposited onto the substrate, forming a uniform and durable coating. CVD is widely used in industries such as electronics, aerospace, and manufacturing due to its ability to produce high-purity, dense, and well-adhered metal films. Despite its high reaction temperatures, advancements in plasma and laser-assisted CVD have made it more accessible for temperature-sensitive substrates.
Key Points Explained:
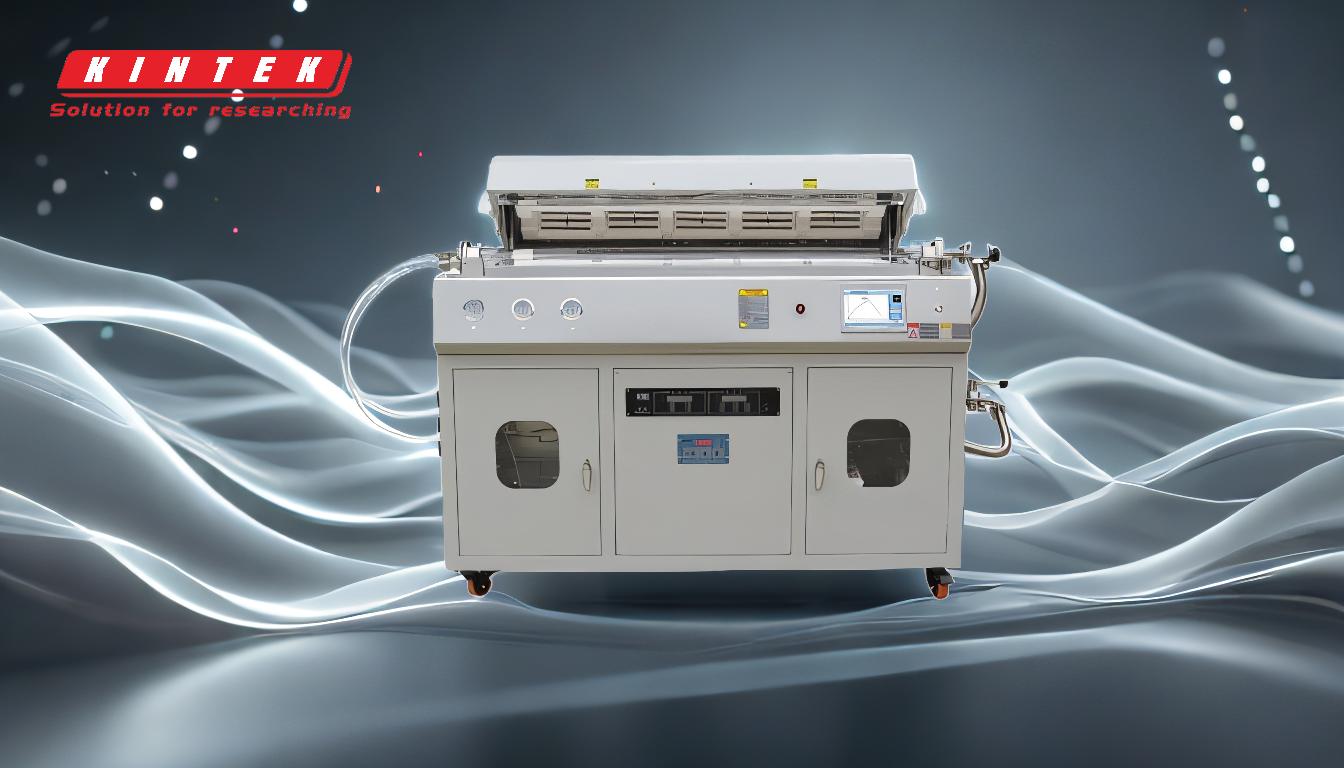
-
Definition of Chemical Vapor Deposition (CVD) of Metals:
- CVD is a process where metal atoms or molecules are deposited onto a substrate through a chemical reaction involving gaseous precursors. The substrate is often heated to enhance the deposition process, resulting in a thin, uniform metal layer. This method is particularly useful for creating high-performance coatings in industries such as semiconductors, optics, and aerospace.
-
Process Mechanism:
- In CVD, a metal-containing gas or vapor is introduced into a reaction chamber. The gas reacts either thermally or through plasma/laser assistance, breaking down into metal atoms or molecules. These particles then adhere to the substrate, forming a thin film. The process can be tailored to achieve specific properties such as corrosion resistance, abrasion resistance, or high purity.
-
Advantages of CVD for Metal Deposition:
- Versatility: CVD can deposit a wide range of metals, including refractory metals like tungsten and titanium, as well as noble metals like gold and platinum.
- Uniformity: The process provides excellent coverage, even on complex or intricate surfaces, ensuring a consistent coating.
- High Purity: CVD produces films with minimal impurities, making it ideal for applications requiring high material quality.
- Durability: The deposited films are highly durable, capable of withstanding extreme temperatures and stress environments.
- Controllability: By adjusting parameters such as temperature, pressure, and gas composition, the properties of the deposited film can be precisely controlled.
-
Challenges and Limitations:
- High Reaction Temperatures: Traditional CVD processes often require temperatures between 850-1100°C, which can limit the choice of substrate materials.
- Cost and Complexity: While CVD is relatively affordable compared to other deposition methods, the equipment and operational costs can still be significant.
- Substrate Compatibility: Certain substrates may not withstand the high temperatures or chemical environments required for CVD, necessitating the use of plasma or laser-assisted techniques to lower the deposition temperature.
-
Applications of CVD in Metal Deposition:
- Electronics: CVD is extensively used in the semiconductor industry to deposit metal layers for interconnects, barriers, and contacts.
- Aerospace: The process is employed to create protective coatings on turbine blades and other high-stress components.
- Optics: CVD is used to deposit reflective and anti-reflective coatings on optical components.
- Medical Devices: Metal coatings produced by CVD are used in implants and surgical tools due to their biocompatibility and durability.
-
Innovations in CVD Technology:
- Plasma-Assisted CVD (PACVD): This variant uses plasma to lower the reaction temperature, making it suitable for temperature-sensitive substrates.
- Laser-Assisted CVD (LACVD): By using laser energy, this method enables precise control over the deposition process, allowing for localized coating and patterning.
- Atomic Layer Deposition (ALD): A related technique, ALD, offers even greater control over film thickness and uniformity, though it is typically slower than CVD.
-
Comparison with Other Deposition Methods:
- Physical Vapor Deposition (PVD): Unlike CVD, PVD relies on physical processes like evaporation or sputtering to deposit materials. While PVD can produce high-quality films, it often lacks the conformal coverage and versatility of CVD.
- Electroplating: This method involves depositing metal ions from a solution onto a substrate. While cost-effective, electroplating generally produces less pure and less durable coatings compared to CVD.
In conclusion, chemical vapor deposition of metals is a highly effective and versatile technique for creating thin, high-quality metal films. Despite its challenges, ongoing advancements in CVD technology continue to expand its applications and improve its accessibility for a wide range of industries.
Summary Table:
Aspect | Details |
---|---|
Definition | Deposits metal layers via chemical reactions using gaseous precursors. |
Process Mechanism | Gas reacts thermally or with plasma/laser assistance to form metal films. |
Advantages | Versatile, uniform, high purity, durable, and controllable. |
Challenges | High temperatures, cost, and substrate compatibility limitations. |
Applications | Electronics, aerospace, optics, and medical devices. |
Innovations | Plasma-assisted CVD, laser-assisted CVD, and atomic layer deposition (ALD). |
Comparison with PVD | CVD offers better conformal coverage and versatility than PVD. |
Comparison with Electroplating | CVD provides higher purity and durability than electroplating. |
Learn how CVD can elevate your metal coating processes—contact our experts today!