Chemical vapor deposition (CVD) is a sophisticated and widely used manufacturing process for creating thin films on substrates. It involves the use of vacuum technology to deposit materials onto a surface through chemical reactions in a gaseous phase. The process is highly controlled and involves multiple steps, including the transport of gaseous reactants to the substrate, adsorption, surface reactions, and desorption of by-products. CVD is distinct from physical vapor deposition (PVD) as it relies on chemical reactions rather than physical processes like evaporation or sputtering. This method is essential in various industries, including electronics, optics, and coatings, due to its ability to produce high-quality, uniform thin films.
Key Points Explained:
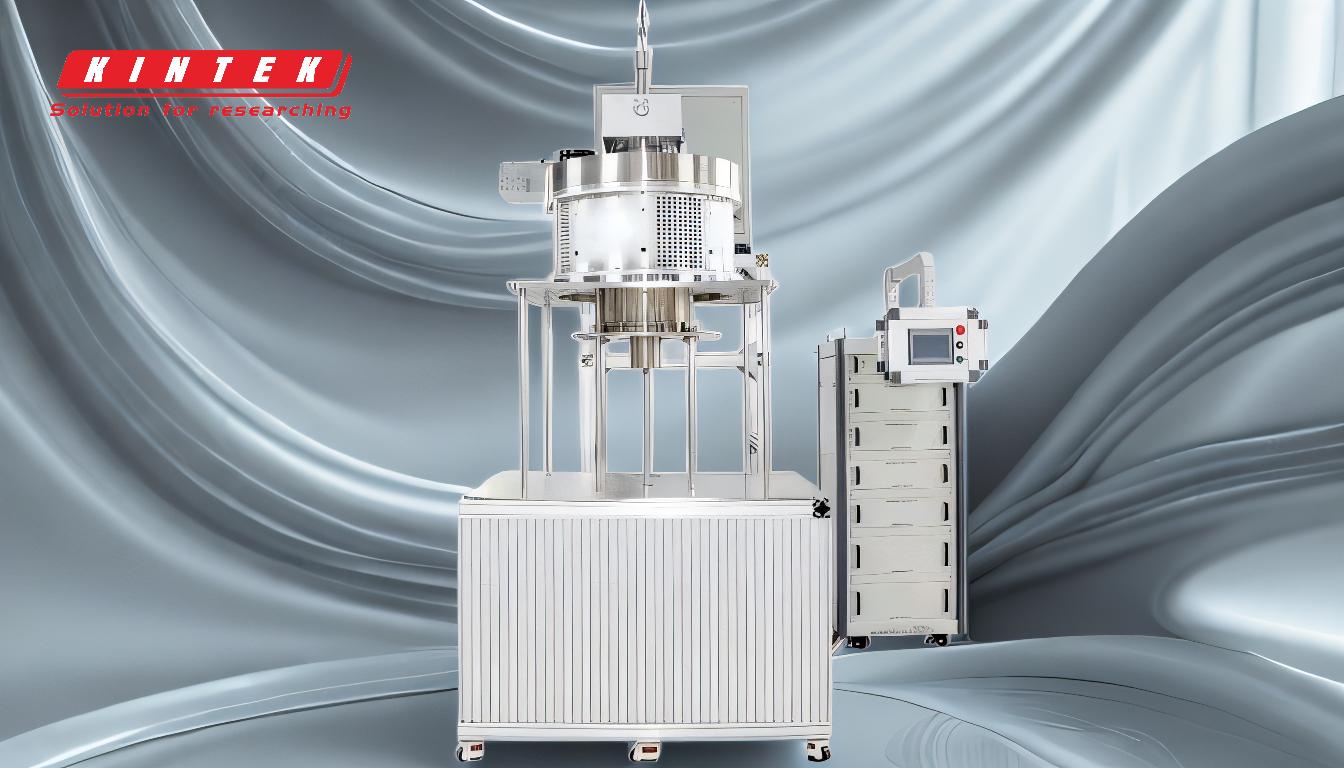
-
Definition of Chemical Vapor Deposition (CVD):
- CVD is a process where a thin solid film is formed on a substrate through chemical reactions in the vapor phase. This involves the use of gaseous precursors that react on the substrate surface to form the desired material.
-
Steps Involved in CVD:
- Transport of Gaseous Reactants: The gaseous species containing the reactants are transported to the substrate surface.
- Adsorption: The gaseous species adsorb onto the substrate surface.
- Surface Reactions: Chemical reactions occur on the substrate surface, leading to the formation of the thin film.
- Desorption: The by-products of the reaction and any unreacted species desorb from the surface and are transported away.
-
Comparison with Physical Vapor Deposition (PVD):
- Unlike PVD, which uses physical processes like evaporation or sputtering, CVD relies on chemical reactions to deposit materials. This allows for more complex and varied material compositions and structures.
-
Applications of CVD:
- CVD is used in various industries to create thin films for electronics (e.g., semiconductors), optics (e.g., anti-reflective coatings), and protective coatings (e.g., wear-resistant coatings).
-
Advantages of CVD:
- Uniformity: CVD can produce highly uniform thin films, even on complex geometries.
- Versatility: A wide range of materials can be deposited using CVD, including metals, ceramics, and polymers.
- High Purity: The process can achieve high-purity films due to the controlled environment and chemical reactions.
-
Challenges in CVD:
- High Temperatures: Many CVD processes require high temperatures, which can limit the types of substrates that can be used.
- Complexity: The process involves multiple steps and parameters that need to be carefully controlled, making it more complex than some other deposition methods.
-
Types of CVD Processes:
- Atmospheric Pressure CVD (APCVD): Conducted at atmospheric pressure, suitable for large-scale production.
- Low-Pressure CVD (LPCVD): Conducted at reduced pressures, allowing for better control over film properties.
- Plasma-Enhanced CVD (PECVD): Uses plasma to enhance the chemical reactions, allowing for lower temperatures.
In summary, the chemical vapor deposition process is a critical technology for the fabrication of thin films in various industries. Its ability to produce high-quality, uniform coatings through controlled chemical reactions makes it indispensable for applications requiring precise material properties.
Summary Table:
Aspect | Details |
---|---|
Definition | A process forming thin films via chemical reactions in the vapor phase. |
Steps | Transport, adsorption, surface reactions, desorption. |
Comparison with PVD | Relies on chemical reactions, not physical processes like evaporation. |
Applications | Electronics, optics, protective coatings. |
Advantages | Uniformity, versatility, high purity. |
Challenges | High temperatures, complexity. |
Types of CVD | APCVD, LPCVD, PECVD. |
Interested in leveraging CVD for your applications? Contact our experts today to learn more!