Chemical vapor deposition (CVD) is a process used to create thin films or nanoparticles by depositing a solid material onto a substrate through chemical reactions in the vapor phase. This method is highly versatile, allowing for the production of ultra-thin, pure, and dense films or particles. It is widely used in industries such as electronics, where it is essential for creating electrical circuits. Despite its many advantages, such as high deposition rates, uniform coating, and the ability to coat complex shapes, CVD does have limitations, including high reaction temperatures that can be unsuitable for certain substrates. However, advancements like plasma or laser-assisted technologies have helped mitigate these limitations by reducing the required temperatures.
Key Points Explained:
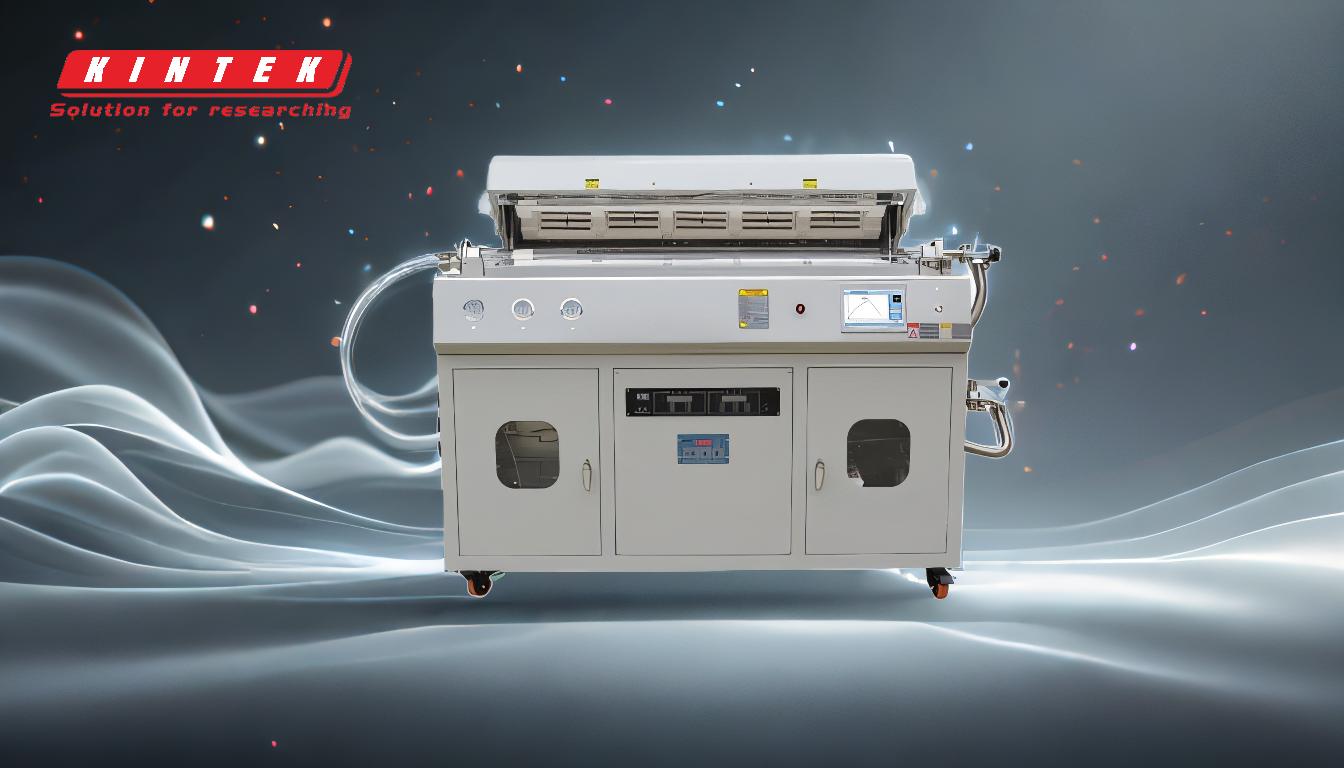
-
Definition of Chemical Vapor Deposition (CVD):
- CVD is a thin-film deposition process where a solid film is formed on a heated substrate through chemical reactions in the vapor phase. The depositing species can be atoms, molecules, or a combination of both. This process is crucial for creating highly pure and dense materials, making it ideal for applications in electronics and nanotechnology.
-
Process Mechanism:
- In CVD, a precursor material is vaporized in a vacuum chamber, often using a heat source. The vaporized material then undergoes a chemical reaction, leading to the deposition of a solid film on the substrate. The process can be controlled precisely, allowing for the creation of ultra-thin layers, which are essential for applications like electrical circuits.
-
Advantages of CVD:
- High Purity and Density: CVD produces materials with high purity and density, which are critical for many industrial applications.
- Uniform Coating: The process allows for uniform coating, even on complex shapes, due to its non-line-of-sight nature.
- Versatility: CVD is highly versatile, relying on chemical reactions that can be tailored to produce a wide range of materials.
- Scalability: The process is easily scalable, making it suitable for both laboratory and industrial applications.
- Control Over Deposition: Full control over the timing and conditions of the deposition process allows for precise material properties.
-
Limitations of CVD:
- High Reaction Temperatures: Traditional CVD processes require high temperatures (850-1100°C), which can be incompatible with certain substrate materials.
- Mitigation Techniques: Advances such as plasma or laser-assisted CVD have been developed to reduce the required deposition temperatures, making the process more accessible for temperature-sensitive materials.
-
Applications of CVD:
- Electronics: CVD is extensively used in the production of electrical circuits, where ultra-thin layers of materials are required.
- Nanotechnology: The ability to produce nanoparticles and thin films makes CVD a key technology in the field of nanotechnology.
- Coatings: CVD is used to apply protective or functional coatings to various materials, enhancing their properties.
-
Comparison with Other Deposition Methods:
- Unlike physical vapor deposition (PVD), which relies on physical processes like evaporation or sputtering, CVD involves chemical reactions. This distinction allows CVD to produce more complex and high-purity materials, though it often requires higher temperatures.
In summary, chemical vapor deposition is a powerful and versatile technique for creating thin films and nanoparticles with high purity and density. While it has some limitations, particularly related to high reaction temperatures, ongoing advancements continue to expand its applicability across various industries.
Summary Table:
Aspect | Details |
---|---|
Definition | CVD is a process to deposit thin films or nanoparticles via chemical reactions in the vapor phase. |
Process Mechanism | Precursor material is vaporized, reacts chemically, and deposits on a substrate. |
Advantages | High purity, uniform coating, versatility, scalability, and precise control. |
Limitations | High reaction temperatures (850-1100°C), mitigated by plasma/laser-assisted CVD. |
Applications | Electronics (circuits), nanotechnology (nanoparticles), and functional coatings. |
Comparison with PVD | CVD uses chemical reactions, producing higher purity materials than PVD. |
Discover how CVD can revolutionize your material production—contact our experts today!