Chemical vapor deposition (CVD) is a process used to create thin films or coatings on a substrate by exposing it to gaseous chemicals in a controlled environment. The gases react chemically on the substrate's surface, forming a solid material that adheres to it. This method is widely used in industries to enhance the durability, thermal properties, and friction resistance of materials. The process can occur under vacuum or at atmospheric pressure, depending on the specific application. CVD is versatile and can deposit a variety of materials, including metals, ceramics, and semiconductors, making it essential in manufacturing and technology.
Key Points Explained:
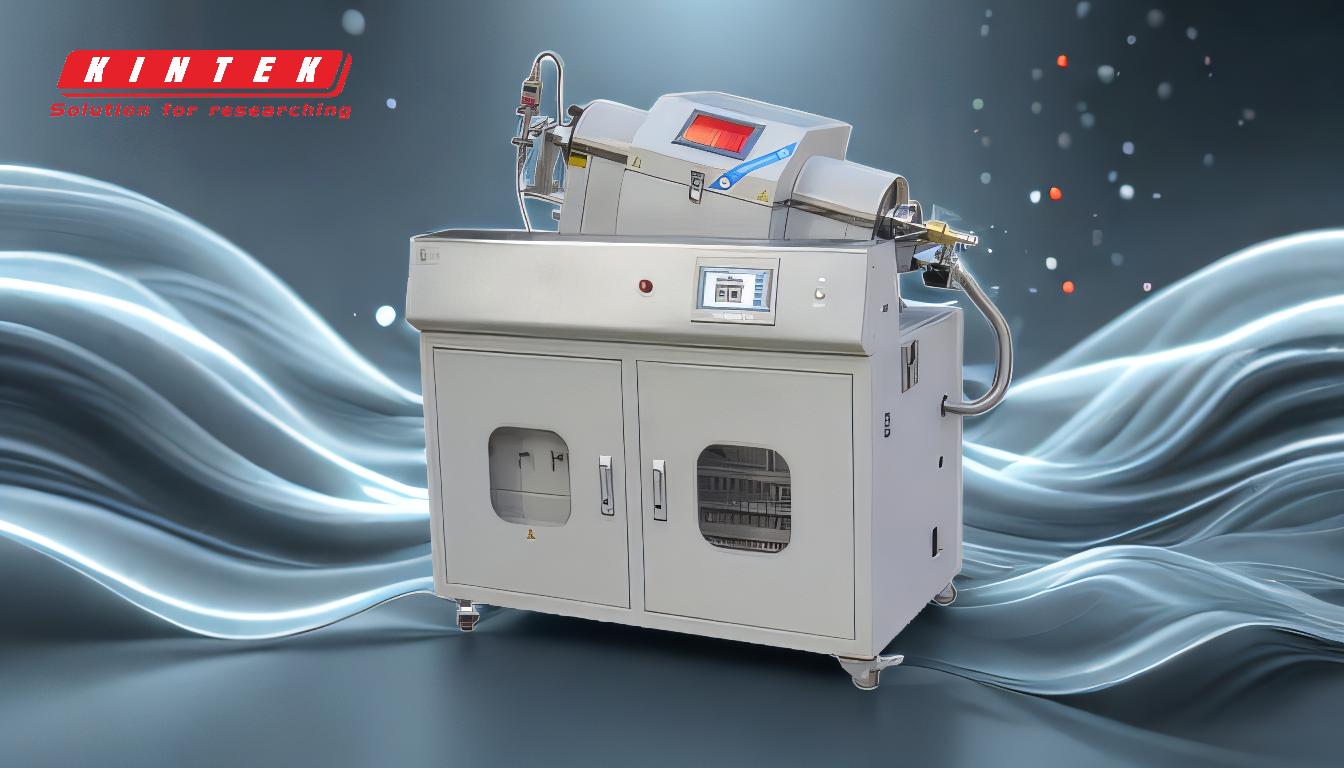
-
Definition of Chemical Vapor Deposition (CVD):
- CVD is a technique where a solid material is deposited onto a substrate through chemical reactions of gaseous precursors. The substrate is exposed to volatile compounds that react or decompose on its surface, forming a thin, solid layer.
-
Process Overview:
- The process involves three main steps:
- Introduction of Gaseous Precursors: The substrate is placed in a chamber, and gaseous chemicals are introduced.
- Chemical Reaction: The gases react or decompose on the heated substrate, forming a solid material.
- Deposition: The solid material adheres to the substrate, creating a thin film or coating.
- The process involves three main steps:
-
Types of CVD:
- Atmospheric Pressure CVD (APCVD): Conducted at normal atmospheric pressure, suitable for large-scale production.
- Low-Pressure CVD (LPCVD): Performed under reduced pressure, offering better uniformity and control.
- Plasma-Enhanced CVD (PECVD): Uses plasma to enhance chemical reactions, allowing deposition at lower temperatures.
-
Applications of CVD:
- Semiconductor Manufacturing: Used to deposit thin films of silicon, silicon dioxide, and other materials in microelectronics.
- Protective Coatings: Enhances the durability and wear resistance of tools and components.
- Optical Coatings: Deposits anti-reflective and reflective layers on lenses and mirrors.
- Solar Cells: Produces thin-film photovoltaic materials for solar energy applications.
-
Advantages of CVD:
- High Purity: Produces high-purity materials with excellent uniformity.
- Versatility: Can deposit a wide range of materials, including metals, ceramics, and polymers.
- Conformal Coatings: Ensures uniform coverage even on complex geometries.
-
Challenges and Limitations:
- High Temperatures: Some CVD processes require high temperatures, limiting the choice of substrates.
- Cost: Equipment and precursor gases can be expensive.
- Safety: Handling reactive gases requires strict safety measures.
-
Comparison with Other Deposition Methods:
- Physical Vapor Deposition (PVD): Unlike CVD, PVD involves physical processes like sputtering or evaporation to deposit materials.
- Atomic Layer Deposition (ALD): ALD offers better control at the atomic level but is slower compared to CVD.
-
Future Trends in CVD:
- Low-Temperature CVD: Development of processes that work at lower temperatures to expand the range of compatible substrates.
- Green CVD: Focus on using environmentally friendly precursors and reducing waste.
- Nanotechnology: CVD is increasingly used to fabricate nanomaterials for advanced applications.
By understanding these key points, one can appreciate the significance of CVD in modern technology and its potential for future innovations.
Summary Table:
Aspect | Details |
---|---|
Definition | A process to deposit thin films on substrates using chemical reactions of gases. |
Process Steps | 1. Introduce gaseous precursors. 2. Chemical reaction on substrate. 3. Deposition. |
Types of CVD | APCVD, LPCVD, PECVD |
Applications | Semiconductors, protective coatings, optical coatings, solar cells |
Advantages | High purity, versatility, conformal coatings |
Challenges | High temperatures, cost, safety concerns |
Future Trends | Low-temperature CVD, green CVD, nanotechnology applications |
Discover how CVD can revolutionize your manufacturing process—contact us today for expert guidance!