CVD (Chemical Vapor Deposition) coating is a versatile and advanced surface coating technology used to deposit thin films of materials onto substrates. It involves exposing a substrate to volatile precursors in a gaseous state, which react or decompose on the substrate surface to form a uniform and conformal coating. This process is widely used across industries for applications such as wear resistance, corrosion protection, high-temperature resistance, and semiconductor fabrication. CVD offers advantages like precise control over film properties, excellent adhesion, and the ability to deposit a wide range of materials, including metals, ceramics, and semiconductors. It is a dry chemical process that eliminates the challenges of wet chemical methods and enables the creation of chemically tailored surfaces for specific applications.
Key Points Explained:
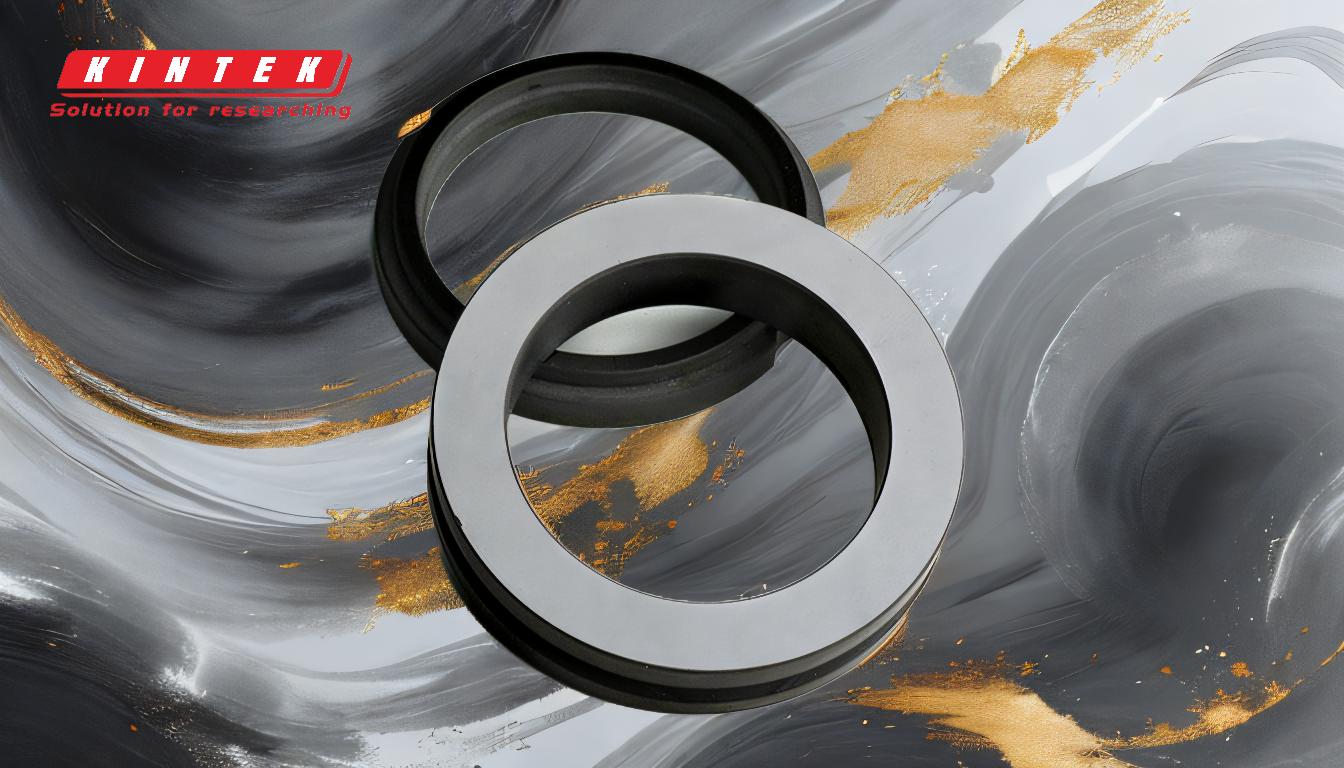
-
Definition of CVD Coating:
- CVD coating refers to the deposition of thin films on a substrate through a chemical reaction in the gas phase. The process involves exposing the substrate to volatile precursors that react or decompose on its surface to form the desired coating.
- This method is highly versatile and can be used to deposit a variety of materials, including metals, ceramics, and semiconductors.
-
Process Mechanism:
- In CVD, precursors in the vapor phase are introduced into a reaction chamber where they react or decompose on the substrate surface at elevated temperatures.
- The chemical reaction results in the deposition of a thin film, with key parameters such as deposition temperature, precursor flow rates, and pressure influencing the film's structure and morphology.
- CVD can be performed at both atmospheric and low pressures, depending on the specific application and desired film properties.
-
Advantages of CVD Coating:
- Conformal and Uniform Coatings: CVD provides highly uniform and conformal coatings, even on complex geometries, ensuring consistent coverage.
- Dry Chemical Process: Unlike wet chemical methods, CVD is a dry process, eliminating issues like solvent handling and waste disposal.
- Tailored Chemical Functionalities: CVD allows for the retention of specific chemical functionalities, enabling the creation of surfaces designed for specific applications, such as interactive, detection, or responsive systems.
- Excellent Adhesion: The coatings formed through CVD exhibit very high adhesive strength due to the chemical bonding between the film and the substrate.
-
Applications of CVD Coating:
- Wear and Corrosion Resistance: CVD is widely used to apply protective coatings that enhance wear resistance, corrosion resistance, and high-temperature protection.
- Semiconductor Fabrication: CVD is a key technology in the production of semiconductor devices, including integrated circuits and sensors.
- Optical and Structural Components: It is used in the fabrication of optical fibers for telecommunications and dense structural parts.
- Advanced Materials: CVD is employed in the production of composites like carbon-carbon and silicon carbide, as well as in powder production and catalyst manufacturing.
-
Materials Deposited by CVD:
- CVD can deposit a wide range of materials, including dielectric films (e.g., SiO2, Si3N4, PSG, BPSG, TEOS), semiconductor materials, metals, and metal-organic compounds.
- This versatility makes CVD suitable for diverse applications across multiple industries.
-
Process Parameters and Control:
- The properties of the deposited films, such as thickness, composition, and morphology, can be precisely controlled by adjusting parameters like temperature, pressure, and precursor flow rates.
- This level of control ensures repeatability and consistency in the coating process.
-
High-Temperature Operation:
- CVD processes typically operate at high temperatures, often around 1000 °C, which facilitates the chemical reactions necessary for film deposition.
- The high temperatures also contribute to the strong adhesion and durability of the coatings.
-
Repeatability and Step Coverage:
- CVD coating is known for its excellent repeatability, ensuring consistent results across multiple batches.
- It also provides superior step coverage, meaning it can uniformly coat surfaces with complex geometries or intricate features.
In summary, CVD coating is a highly effective and versatile technology for depositing thin films with precise control over their properties. Its applications span a wide range of industries, making it a critical process for advanced material fabrication and surface engineering.
Summary Table:
Aspect | Details |
---|---|
Definition | Deposition of thin films via chemical reaction in the gas phase. |
Process Mechanism | Precursors react/decompose on substrate surfaces at high temperatures. |
Advantages | Uniform coatings, dry process, tailored functionalities, excellent adhesion. |
Applications | Wear/corrosion resistance, semiconductors, optical fibers, advanced materials. |
Materials Deposited | Metals, ceramics, semiconductors, dielectric films. |
Key Parameters | Temperature, pressure, precursor flow rates. |
High-Temperature Range | Typically around 1000 °C. |
Repeatability | Ensures consistent results across batches. |
Discover how CVD coating can revolutionize your applications—contact our experts today!