CVD (Chemical Vapor Deposition) and PVD (Physical Vapor Deposition) are two advanced coating technologies used to create thin, high-purity, and dense films on substrates. While both methods are used for similar applications, they differ significantly in their processes, environmental impact, and suitability for specific use cases. CVD involves chemical reactions that produce new substances, operates at higher temperatures, and can create uniform coatings. PVD, on the other hand, relies on physical processes like vaporization and condensation, operates at lower temperatures, and is more environmentally friendly. The choice between CVD and PVD depends on factors such as temperature tolerance, material properties, and application requirements.
Key Points Explained:
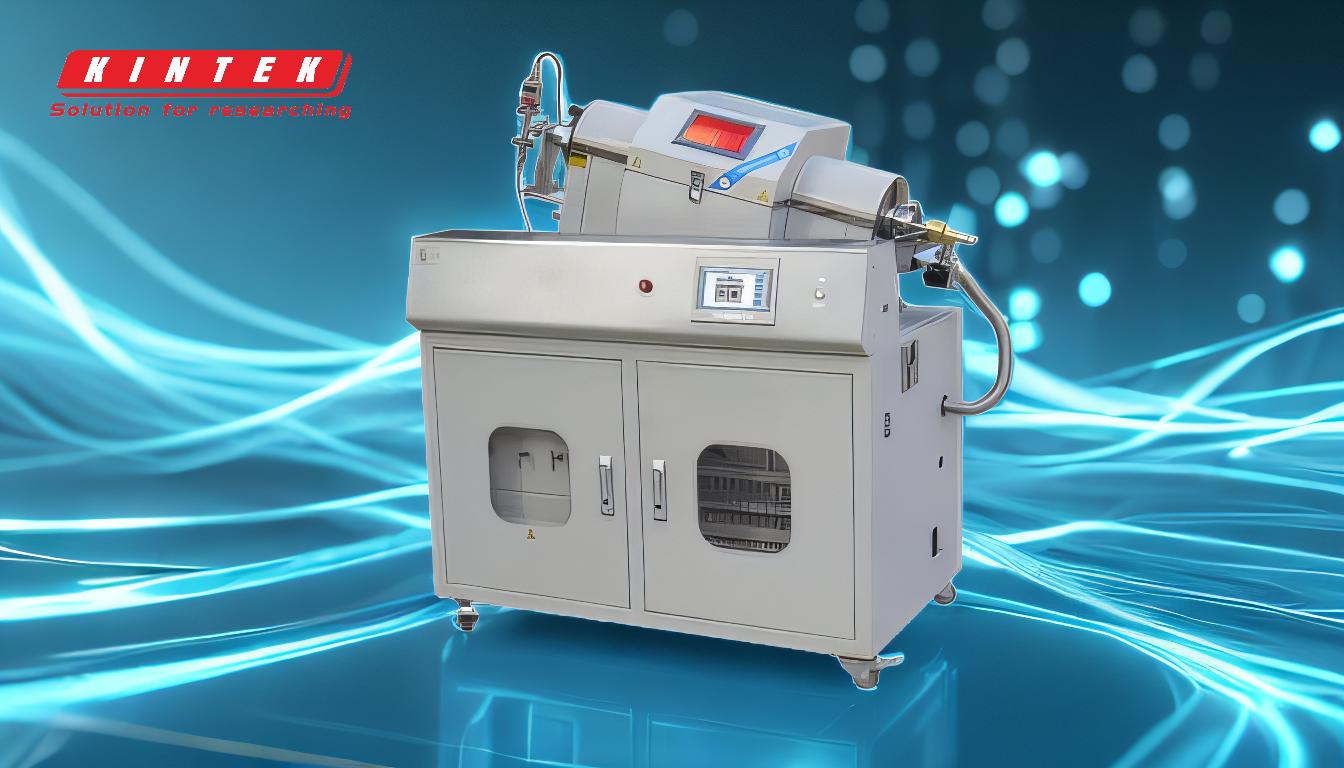
-
Fundamental Difference Between CVD and PVD:
- CVD involves chemical reactions where precursor gases react on the substrate surface to form a new material. This process consumes the reactants and produces byproducts, often requiring higher temperatures (400-1000°C).
- PVD uses physical methods such as sputtering or thermal evaporation to transform solid materials into a vapor state, which then condenses onto the substrate. No chemical reactions occur, making it a cleaner and more environmentally friendly process.
-
Process Characteristics:
-
CVD:
- Operates at elevated temperatures, which can limit its use with temperature-sensitive materials.
- Produces dense, pure, and uniform coatings with excellent thickness control.
- Involves a flowing gaseous state, allowing for uniform deposition on complex geometries.
-
PVD:
- Operates at lower temperatures, making it suitable for temperature-sensitive substrates.
- Creates extremely thin, durable, and clean coatings with high control over film properties like adhesion, hardness, and lubricity.
- Uses line-of-sight deposition, which can limit uniformity on complex shapes.
-
CVD:
-
Environmental and Safety Considerations:
-
CVD:
- Uses volatile chemicals that can produce harmful byproducts, requiring careful handling and disposal.
- Higher energy consumption due to elevated temperatures.
-
PVD:
- Safer and more environmentally friendly, as it does not involve hazardous chemicals or produce harmful gases.
- Lower energy consumption due to lower operating temperatures.
-
CVD:
-
Applications and Suitability:
-
CVD is preferred for applications requiring:
- High-purity coatings with uniform thickness.
- Dense and durable films for semiconductors, optics, and wear-resistant coatings.
-
PVD is favored for:
- Cutting tools and industrial applications where lower temperatures and cleaner processes are critical.
- Coatings requiring specific attributes like hardness, adhesion, or lubricity.
-
CVD is preferred for applications requiring:
-
Automation and Scalability:
- PVD is more easily automated, making it suitable for high-volume production.
- CVD processes can be more complex and less adaptable to automation due to the need for precise control of chemical reactions and gas flows.
-
Material Compatibility:
- CVD is limited by the high temperatures required, which may not be suitable for materials with low boiling points or temperature sensitivity.
- PVD is more versatile in terms of material compatibility, as it operates at lower temperatures and does not rely on chemical reactions.
In summary, while both CVD and PVD are effective for creating high-quality thin films, their differences in process mechanics, environmental impact, and application suitability make them better suited for specific use cases. CVD excels in creating uniform, dense coatings for high-temperature applications, whereas PVD is preferred for its cleaner, lower-temperature processes and adaptability to industrial automation.
Summary Table:
Aspect | CVD | PVD |
---|---|---|
Process | Chemical reactions producing new substances | Physical vaporization and condensation |
Temperature | High (400-1000°C) | Low |
Environmental Impact | Produces harmful byproducts; higher energy consumption | Cleaner; lower energy consumption |
Applications | High-purity, dense coatings for semiconductors, optics, and wear | Cutting tools, industrial applications, and specific film properties |
Automation | Less adaptable to automation | Easily automated for high-volume production |
Material Compatibility | Limited for temperature-sensitive materials | Versatile for a wide range of materials |
Need help choosing between CVD and PVD for your application? Contact our experts today!