Chemical Vapor Deposition (CVD) is a critical process in semiconductor manufacturing, used to deposit thin films of materials onto a substrate through chemical reactions of gaseous precursors. The process involves several steps, including the introduction and activation of reactants, surface reactions, and the removal of byproducts. Key parameters such as deposition temperature, pressure, and precursor flow rates significantly influence the quality and characteristics of the deposited material. CVD is widely utilized in the fabrication of semiconductor devices, nanomaterials, and protective coatings due to its ability to produce high-quality, high-performance films.
Key Points Explained:
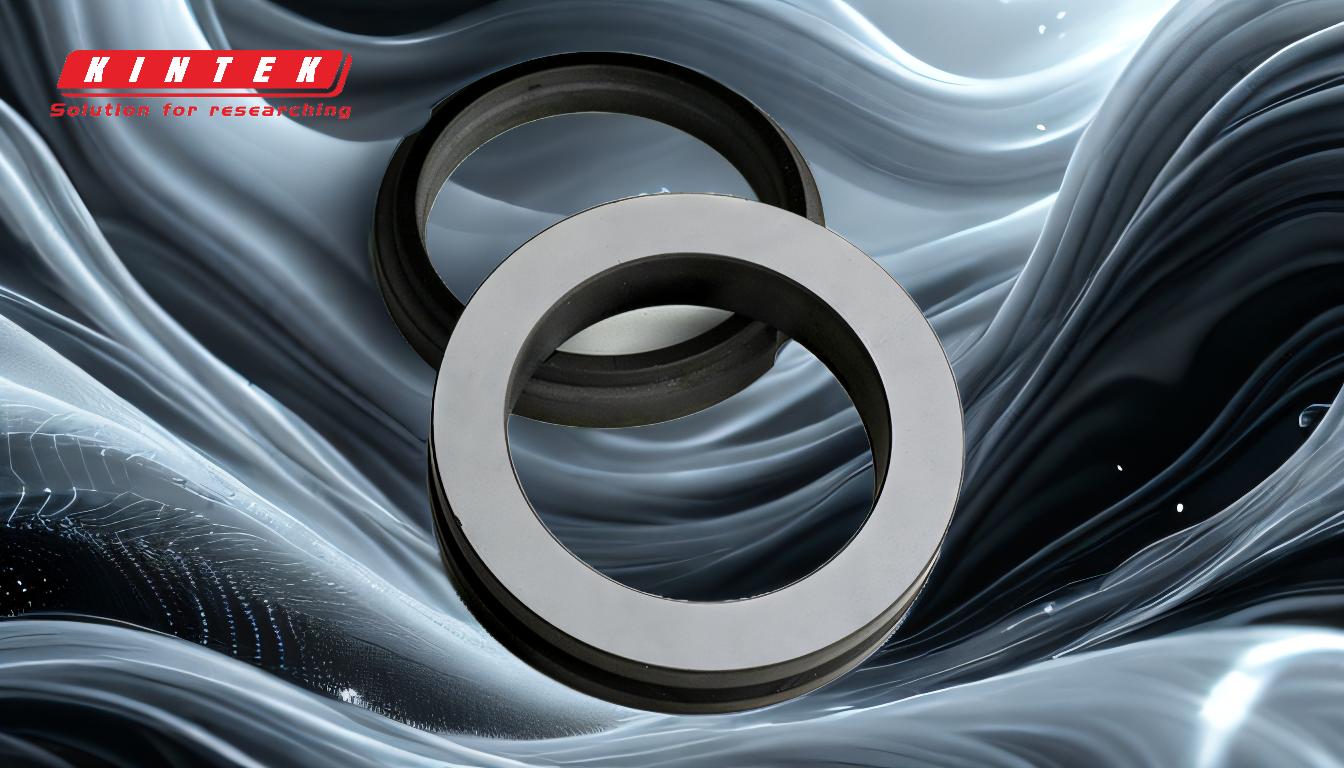
-
Introduction of Reactants:
- Gaseous precursors are introduced into a reaction chamber containing the substrate. These precursors are typically in vapor form and are selected based on the desired material to be deposited.
- The introduction process involves precise control of flow rates to ensure uniform deposition.
-
Activation of Reactants:
- Precursors are activated through methods such as thermal energy, plasma, or catalysts. This activation is crucial for initiating the chemical reactions necessary for deposition.
- Thermal activation involves heating the substrate to high temperatures (e.g., 1000-1100 ˚C) to prepare the surface chemistry and etch passivation.
-
Surface Reaction and Deposition:
- Activated precursors react at the substrate surface to form the desired material. This step involves chemisorption and diffusion of reactants onto the substrate.
- Surface non-homogeneous reactions lead to the formation of ceramic nanocomposite coatings on metallic or non-metallic substrates.
-
Removal of Byproducts:
- Volatile or non-volatile byproducts are eliminated from the reaction chamber. This step is essential to maintain the purity and quality of the deposited film.
- Purging residual gas is crucial for optimal growth and to prevent contamination.
-
Key Parameters Influencing CVD:
- Deposition Temperature: High temperatures are often required to activate the chemical reactions and ensure proper adhesion of the deposited material.
- Pressure: Both atmospheric and low-pressure conditions can be used, depending on the specific requirements of the deposition process.
- Flow Rates of Precursors: Precise control of precursor flow rates is necessary to achieve uniform and high-quality films.
-
Applications of CVD in Semiconductors:
- CVD is extensively used in the fabrication of semiconductor devices, where it is employed to deposit thin films of materials such as silicon dioxide, silicon nitride, and various metals.
- The process is also crucial in the development of nanomaterials and protective coatings, providing high-performance and durable surfaces.
-
Challenges and Considerations:
- Substrate Temperature Control: Maintaining the correct substrate temperature during deposition and cooling is critical for achieving the desired material properties.
- Byproduct Management: Efficient removal of byproducts is necessary to prevent defects and ensure the integrity of the deposited film.
In summary, the CVD process is a sophisticated technique that plays a vital role in semiconductor manufacturing. By carefully controlling the introduction, activation, and reaction of gaseous precursors, high-quality thin films can be deposited onto substrates, enabling the production of advanced semiconductor devices and materials.
Summary Table:
Key Aspect | Description |
---|---|
Introduction of Reactants | Gaseous precursors are introduced into a reaction chamber for uniform deposition. |
Activation of Reactants | Precursors are activated via thermal energy, plasma, or catalysts. |
Surface Reaction | Activated precursors react on the substrate to form desired materials. |
Byproduct Removal | Volatile/non-volatile byproducts are eliminated to maintain film purity. |
Key Parameters | Deposition temperature, pressure, and precursor flow rates. |
Applications | Semiconductor devices, nanomaterials, and protective coatings. |
Challenges | Substrate temperature control and byproduct management. |
Discover how CVD can enhance your semiconductor manufacturing—contact our experts today!