Deposition in semiconductor manufacturing refers to the process of adding thin layers of materials onto a substrate to create the intricate structures required for semiconductor devices. This process is critical for producing high-quality, high-performance solid materials and thin films that form the foundation of modern electronics. Various deposition technologies, such as Chemical Vapor Deposition (CVD), Physical Vapor Deposition (PVD), and Atomic Layer Deposition (ALD), are employed to achieve precise control over layer thickness and composition. These techniques enable the creation of complex semiconductor devices by depositing materials like aluminum, tungsten, and other components onto substrates. Deposition processes are essential for ensuring the functionality, reliability, and performance of semiconductor devices.
Key Points Explained:
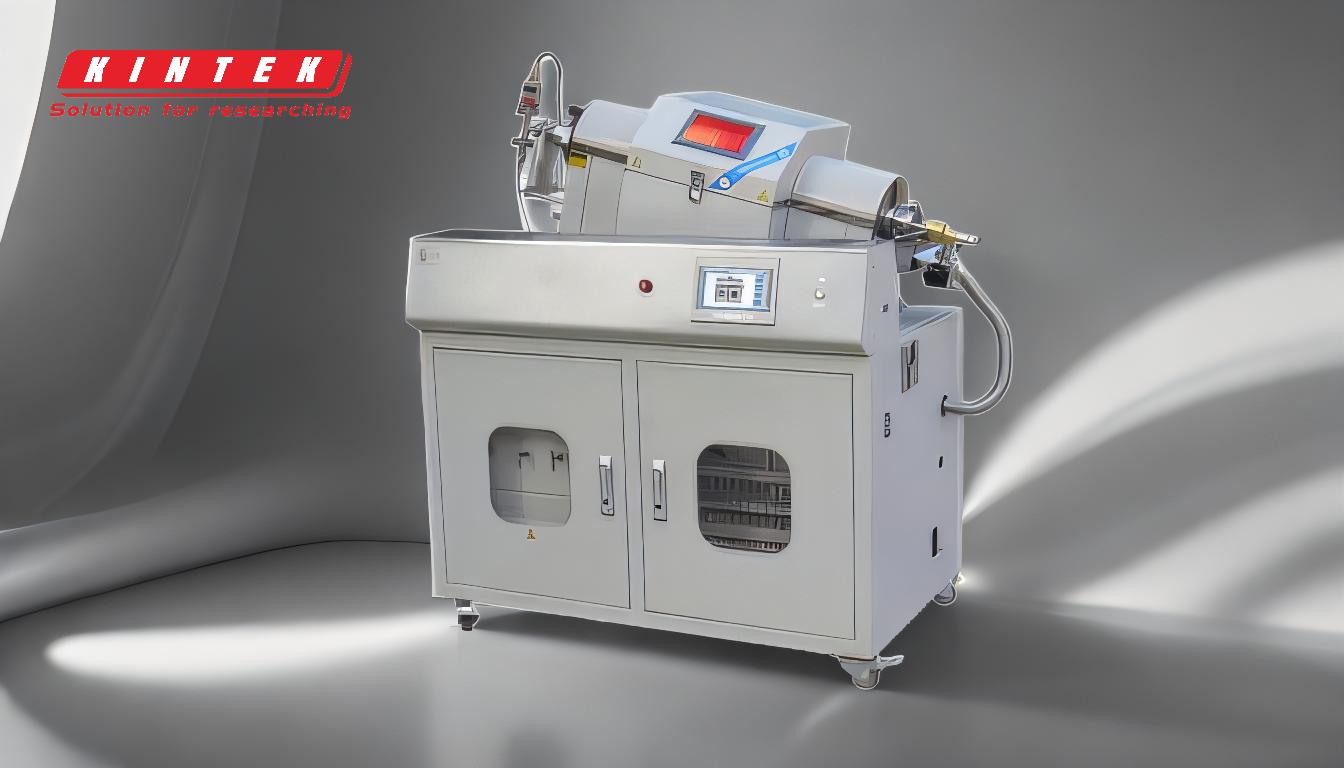
-
Definition and Purpose of Deposition in Semiconductor Manufacturing:
- Deposition is the process of adding thin layers of materials onto a substrate to form the structures needed for semiconductor devices.
- It is a critical step in semiconductor manufacturing, as it directly impacts the quality, performance, and functionality of the final product.
- The primary goal is to create high-quality, high-performance solid materials and thin films that meet the stringent requirements of modern electronics.
-
Types of Deposition Technologies:
-
Chemical Vapor Deposition (CVD):
- Involves the chemical reaction of gaseous precursors to form a solid material on the substrate.
- Common variants include Low Pressure CVD (LPCVD), Plasma Enhanced CVD (PECVD), and Atomic Layer Deposition (ALD).
-
Physical Vapor Deposition (PVD):
- Involves the physical transfer of material from a source to the substrate, often through sputtering or evaporation.
-
Other Techniques:
- Sub-Atmospheric Pressure CVD (SACVD), Atmospheric Pressure CVD (APCVD), Ultra-High Vacuum CVD (UHV-CVD), and Epitaxial Deposition (Epi) are also used for specific applications.
-
Chemical Vapor Deposition (CVD):
-
Materials Used in Deposition Processes:
-
Aluminum:
- Commonly used for the main layer of the substrate due to its excellent electrical conductivity and compatibility with semiconductor processes.
-
Tungsten:
- Often deposited using CVD techniques for applications requiring high conductivity and durability.
-
Other Materials:
- Various secondary layers are deposited to create specific components, such as insulators, conductors, and semiconductors.
-
Aluminum:
-
Advantages of Advanced Deposition Techniques:
-
Precision and Control:
- Techniques like ALD offer atomic-level precision, enabling the creation of ultra-thin films with uniform thickness.
-
Versatility:
- Different deposition methods can be tailored to specific materials and applications, providing flexibility in semiconductor manufacturing.
-
Room-Temperature Processing:
- Methods like aerosol deposition allow for processing at room temperature, which is beneficial for substrates with low melting points or polymers.
-
Precision and Control:
-
Applications of Deposition in Semiconductor Manufacturing:
-
Transistors and Integrated Circuits:
- Deposition is used to create the various layers of transistors and interconnects in integrated circuits.
-
Memory Devices:
- Thin films deposited through these processes are essential for the fabrication of memory cells in devices like DRAM and flash memory.
-
Optoelectronics:
- Deposition techniques are used to create layers for optoelectronic devices, such as LEDs and photovoltaic cells.
-
Transistors and Integrated Circuits:
-
Challenges and Future Trends:
-
Material Compatibility:
- Ensuring that deposited materials are compatible with existing semiconductor processes and do not introduce defects.
-
Scalability:
- Developing deposition techniques that can be scaled up for high-volume manufacturing while maintaining precision and quality.
-
Emerging Technologies:
- Innovations like aerosol deposition and room-temperature processing are expected to play a significant role in the future of semiconductor fabrication.
-
Material Compatibility:
By understanding the various deposition techniques, materials, and their applications, semiconductor manufacturers can optimize their processes to produce high-performance devices that meet the demands of modern technology.
Summary Table:
Aspect | Details |
---|---|
Definition | Adding thin layers of materials onto a substrate for semiconductor devices. |
Key Techniques | CVD, PVD, ALD, SACVD, APCVD, UHV-CVD, Epitaxial Deposition. |
Common Materials | Aluminum, Tungsten, Insulators, Conductors, Semiconductors. |
Advantages | Precision, Versatility, Room-Temperature Processing. |
Applications | Transistors, Integrated Circuits, Memory Devices, Optoelectronics. |
Challenges | Material Compatibility, Scalability, Emerging Technologies. |
Optimize your semiconductor manufacturing process with advanced deposition techniques—contact our experts today!