Deposition of coating material refers to the process of applying a thin layer of material onto a substrate to enhance its properties, such as corrosion resistance, wear resistance, electrical conductivity, or aesthetic appeal. This process is widely used in industries like automotive, aerospace, electronics, and manufacturing. Deposition techniques vary depending on the desired properties, substrate material, and application requirements. Common methods include physical vapor deposition (PVD), chemical vapor deposition (CVD), electroplating, and thermal spraying. Each method has its own advantages and limitations, making it suitable for specific applications. Understanding the deposition process is crucial for selecting the right technique to achieve the desired coating properties.
Key Points Explained:
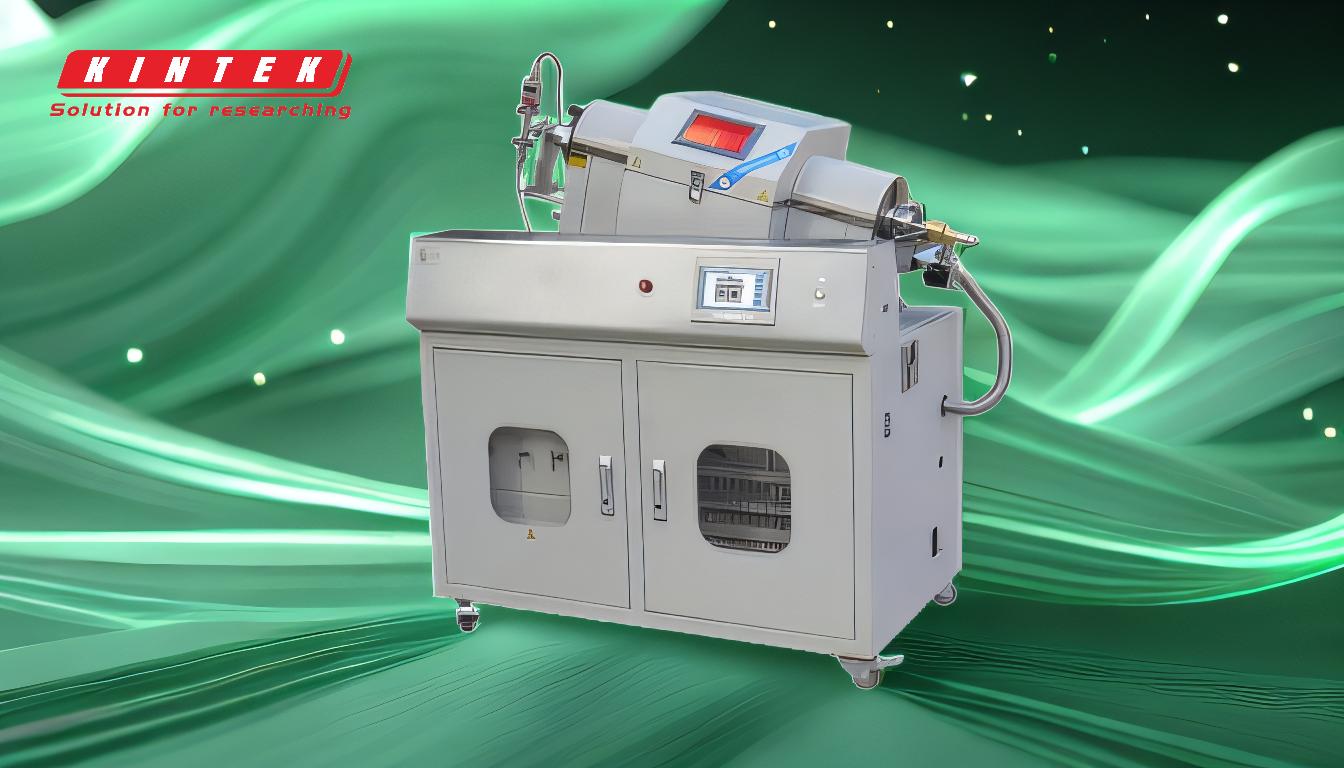
-
Definition of Coating Deposition:
- Coating deposition is the process of applying a thin layer of material onto a substrate. This layer can be metallic, ceramic, polymer, or composite, depending on the application.
- The primary goal is to improve the substrate's performance by enhancing properties such as hardness, corrosion resistance, thermal insulation, or electrical conductivity.
-
Importance of Coating Deposition:
- Protection: Coatings protect substrates from environmental factors like corrosion, oxidation, and wear.
- Functionality: They can add functional properties, such as electrical conductivity or thermal insulation.
- Aesthetics: Coatings are often used to improve the appearance of products, such as decorative finishes on consumer goods.
-
Common Deposition Techniques:
-
Physical Vapor Deposition (PVD):
- PVD involves vaporizing the coating material in a vacuum and depositing it onto the substrate. Techniques include sputtering and evaporation.
- It is used for hard, wear-resistant coatings, such as titanium nitride (TiN) on cutting tools.
-
Chemical Vapor Deposition (CVD):
- CVD uses chemical reactions to deposit a coating from a gas phase onto the substrate. It is ideal for high-temperature applications and produces uniform, high-quality coatings.
- Applications include semiconductor manufacturing and protective coatings on turbine blades.
-
Electroplating:
- Electroplating uses an electric current to deposit a metal coating onto a conductive substrate. It is commonly used for decorative finishes, corrosion protection, and improving electrical conductivity.
-
Thermal Spraying:
- This technique involves melting the coating material and spraying it onto the substrate. It is used for thick coatings and large surface areas, such as in aerospace and automotive industries.
-
Physical Vapor Deposition (PVD):
-
Factors Influencing Deposition:
- Substrate Material: The choice of deposition method depends on the substrate's properties, such as thermal stability and surface roughness.
- Coating Material: Different materials require specific deposition techniques to achieve the desired properties.
- Application Requirements: The intended use of the coated product determines the coating thickness, adhesion strength, and other performance criteria.
-
Advantages and Limitations:
-
Advantages:
- Enhanced durability and performance of substrates.
- Ability to tailor coatings for specific applications.
- Improved product lifespan and reduced maintenance costs.
-
Limitations:
- High equipment and operational costs for some techniques.
- Complexity in achieving uniform coatings on complex geometries.
- Environmental and safety concerns, especially with chemical-based methods.
-
Advantages:
-
Applications of Coating Deposition:
- Automotive: Coatings are used on engine components, brake systems, and decorative trims to improve performance and aesthetics.
- Aerospace: Protective coatings are applied to turbine blades, fuselage, and other critical components to withstand extreme conditions.
- Electronics: Thin films are deposited on semiconductors, circuits, and displays to enhance electrical properties.
- Manufacturing: Cutting tools, molds, and dies are coated to improve wear resistance and extend service life.
By understanding the deposition process and its various techniques, manufacturers can select the most appropriate method to achieve the desired coating properties for their specific applications. This ensures optimal performance, durability, and cost-effectiveness of the coated products.
Summary Table:
Aspect | Details |
---|---|
Definition | Applying a thin layer of material to enhance substrate properties. |
Key Benefits | Corrosion resistance, wear resistance, electrical conductivity, aesthetics. |
Common Techniques | PVD, CVD, electroplating, thermal spraying. |
Applications | Automotive, aerospace, electronics, manufacturing. |
Advantages | Enhanced durability, tailored coatings, cost-effectiveness. |
Limitations | High costs, complex geometries, environmental concerns. |
Discover the best coating deposition solution for your needs—contact our experts today!