Magnetron sputtering cathode is a critical component in the magnetron sputtering process, a plasma-based physical vapor deposition (PVD) method widely used for thin film deposition. The cathode, also referred to as the target, is the material source from which atoms are sputtered onto a substrate to form a thin film. This process is driven by a high-energy plasma created by applying a negative voltage to the cathode, attracting positive ions that collide with the target surface, causing atoms to be ejected. The technique is highly versatile, enabling the deposition of a wide range of materials, including metals, alloys, and dielectrics, with precise control over film properties. It is extensively used in industries such as semiconductors, optics, and microelectronics due to its efficiency, low-temperature operation, and ability to produce high-quality coatings.
Key Points Explained:
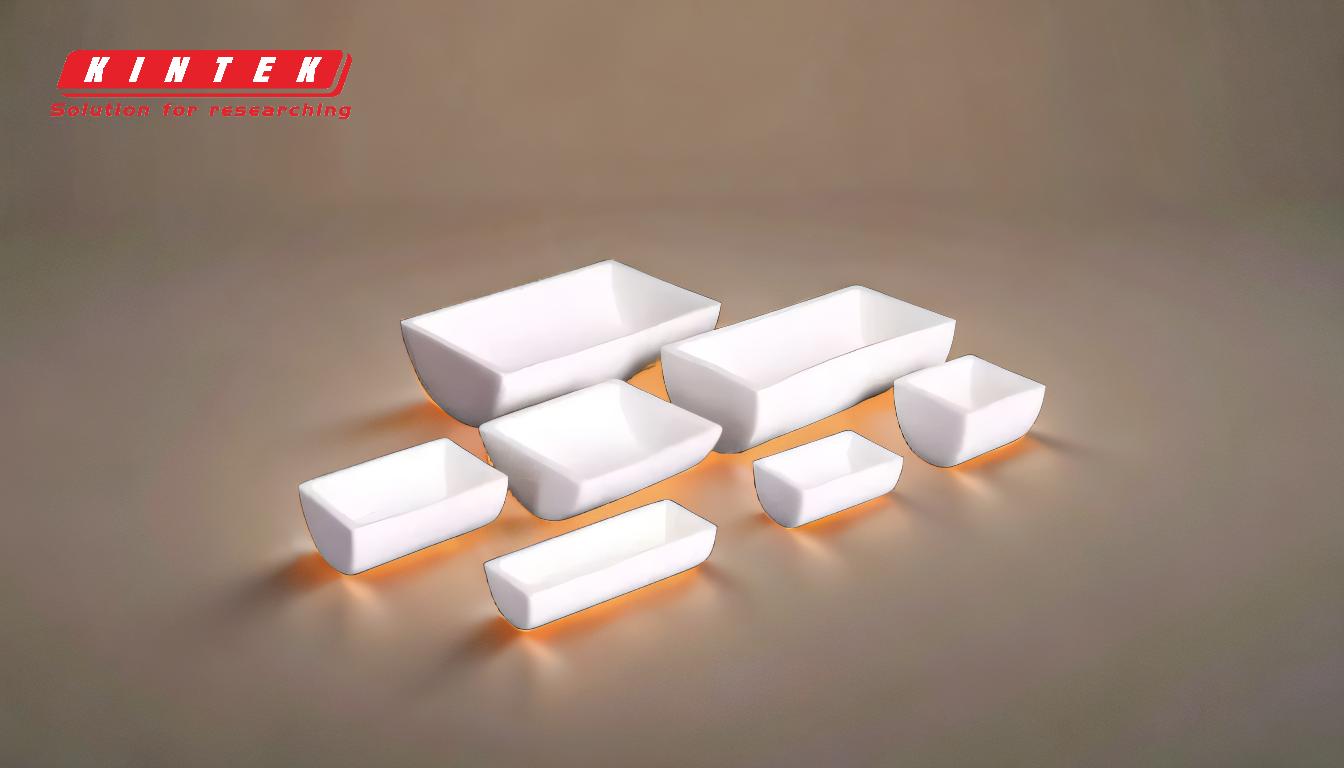
-
What is Magnetron Sputtering?
- Magnetron sputtering is a PVD technique where a high-energy plasma is used to sputter atoms from a target material (cathode) onto a substrate, forming a thin film.
- The process is plasma-based, involving the interaction of ions with the target material to eject atoms, which are then deposited onto the substrate.
- It is widely used in industries such as semiconductors, optics, and microelectronics due to its precision, versatility, and ability to deposit a wide range of materials.
-
Role of the Cathode in Magnetron Sputtering
- The cathode, or target, is the material source from which atoms are sputtered. It is typically made of the material intended for deposition (e.g., metals, alloys, or dielectrics).
- A negative voltage (often −300 V or more) is applied to the cathode, attracting positive ions from the plasma. These ions collide with the target surface, transferring energy and causing atoms to be ejected.
- Magnets placed behind the cathode create a magnetic field that traps electrons, enhancing plasma density and improving deposition efficiency.
-
How Magnetron Sputtering Works
- The process begins with the generation of a plasma in a vacuum chamber. Positive ions in the plasma are accelerated toward the negatively charged cathode.
- When these ions collide with the target surface, they transfer kinetic energy to the target atoms. If the energy exceeds the binding energy of the surface atoms, sputtering occurs.
- The sputtered atoms travel through the vacuum and deposit onto the substrate, forming a thin film with desired properties such as conductivity, reflectivity, or hardness.
-
Advantages of Magnetron Sputtering
- Versatility: Compatible with nearly all materials, including metals, alloys, and dielectrics. It can also deposit compounds while maintaining their composition.
- High Deposition Rates: The process is efficient, allowing for rapid thin film deposition.
- Low-Temperature Operation: Suitable for temperature-sensitive substrates.
- Precision and Control: Enables precise control over film thickness, composition, and properties.
-
Applications of Magnetron Sputtering
- Semiconductors: Used for depositing thin films in the production of integrated circuits and other electronic components.
- Optics: Creates coatings with specific optical properties, such as anti-reflective or reflective films.
- Decorative Coatings: Used in the production of decorative films for consumer products.
- Machining Industry: Provides wear-resistant and protective coatings for tools and components.
-
RF Magnetron Sputtering
- A variant of magnetron sputtering, RF (radio frequency) magnetron sputtering, is particularly useful for depositing non-conductive materials, as it does not require the target to be conductive.
- This technique expands the range of materials that can be deposited, including insulators and ceramics.
-
Key Parameters in Magnetron Sputtering
- Voltage and Power: The applied voltage and power determine the energy of the ions and the rate of sputtering.
- Magnetic Field: The strength and configuration of the magnetic field influence plasma confinement and deposition efficiency.
- Pressure and Gas Composition: The choice of sputtering gas (e.g., argon) and chamber pressure affect the sputtering process and film properties.
In summary, the magnetron sputtering cathode is a fundamental component in the magnetron sputtering process, enabling the deposition of high-quality thin films with precise control over their properties. Its versatility, efficiency, and compatibility with a wide range of materials make it a cornerstone technology in modern manufacturing and research.
Summary Table:
Aspect | Details |
---|---|
Process | Plasma-based PVD technique for thin film deposition. |
Cathode Role | Material source (target) for sputtering atoms onto a substrate. |
Key Mechanism | Negative voltage attracts ions, causing atoms to eject and form thin films. |
Advantages | Versatile, high deposition rates, low-temperature operation, precise control. |
Applications | Semiconductors, optics, decorative coatings, wear-resistant coatings. |
RF Magnetron Sputtering | Expands material range to include non-conductive materials like ceramics. |
Key Parameters | Voltage, magnetic field, pressure, and gas composition. |
Learn how magnetron sputtering cathodes can enhance your thin film processes—contact our experts today!