Material deposition in manufacturing refers to the process of adding material layer by layer to create a part or product. This technique is widely used in additive manufacturing (3D printing) and other advanced manufacturing processes. It involves depositing materials such as metals, polymers, ceramics, or composites in precise patterns to build up a three-dimensional object. The process can be achieved through various methods, including extrusion, sintering, melting, or bonding, depending on the material and the desired outcome. Material deposition enables the creation of complex geometries, customization, and rapid prototyping, making it a cornerstone of modern manufacturing.
Key Points Explained:
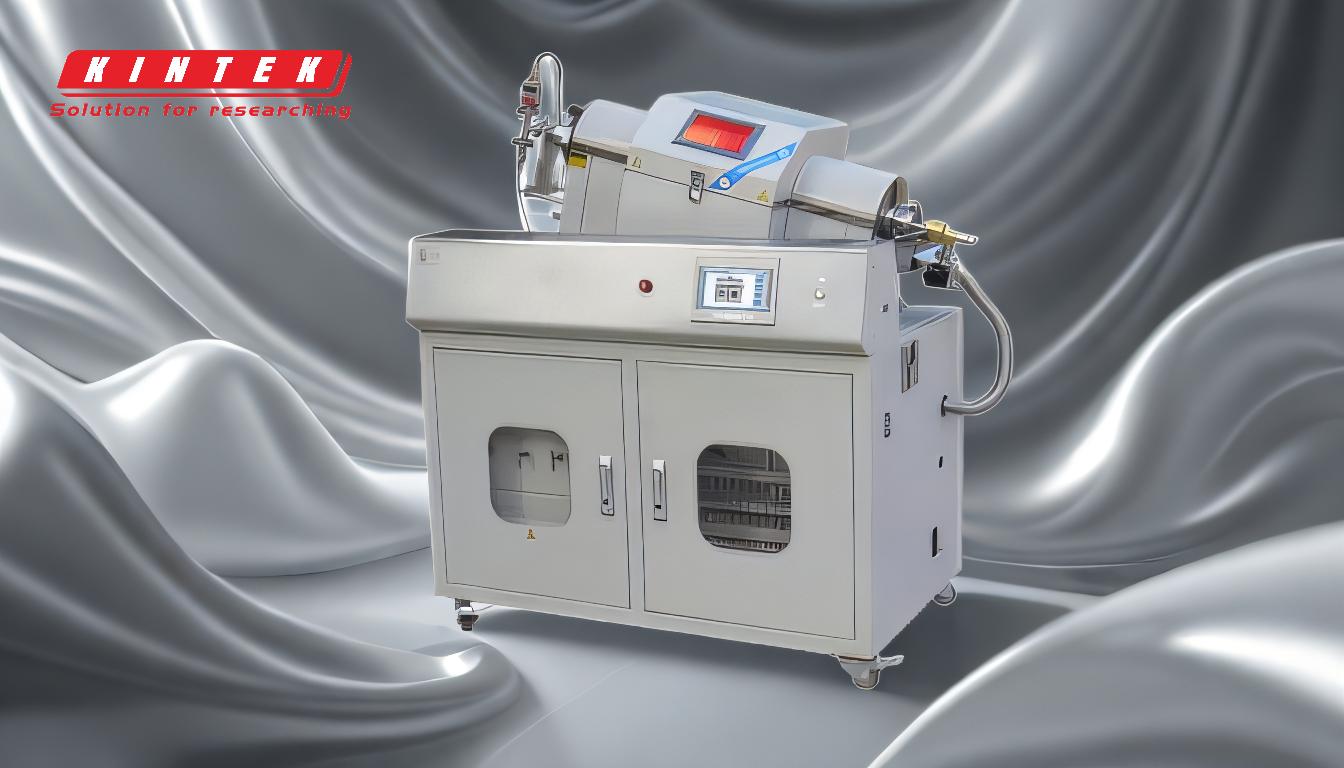
-
Definition and Purpose of Material Deposition:
- Material deposition is the process of adding material in controlled layers to construct a part or product.
- It is a fundamental technique in additive manufacturing, enabling the creation of complex structures that are difficult or impossible to achieve with traditional subtractive methods.
- The purpose is to build components with high precision, customization, and efficiency, often reducing material waste.
-
Types of Material Deposition Techniques:
- Extrusion-Based Deposition: Common in fused deposition modeling (FDM), where thermoplastic filaments are extruded through a heated nozzle and deposited layer by layer.
- Powder Bed Fusion: Techniques like selective laser sintering (SLS) or direct metal laser sintering (DMLS) use lasers to fuse powdered material into solid layers.
- Directed Energy Deposition (DED): A process where focused thermal energy (e.g., lasers or electron beams) is used to melt and deposit material onto a substrate.
- Binder Jetting: A method where a liquid binding agent is selectively deposited onto a powder bed to bind particles together.
- Material Jetting: Similar to inkjet printing, where droplets of material are deposited onto a build platform and cured using UV light or heat.
-
Materials Used in Deposition:
- Metals: Commonly used in aerospace, automotive, and medical industries for high-strength components. Examples include titanium, aluminum, and stainless steel.
- Polymers: Widely used for prototyping and consumer products. Examples include ABS, PLA, and nylon.
- Ceramics: Used for high-temperature and wear-resistant applications. Examples include alumina and zirconia.
- Composites: Materials like carbon fiber-reinforced polymers are used for lightweight, high-strength applications.
-
Applications of Material Deposition:
- Rapid Prototyping: Allows for quick iteration and testing of designs, reducing development time and costs.
- Custom Manufacturing: Enables the production of personalized products, such as medical implants or custom-fit prosthetics.
- Repair and Maintenance: Used to repair worn or damaged components, extending their lifespan.
- Complex Geometries: Facilitates the creation of intricate designs, such as lattice structures or internal channels, which are challenging with traditional methods.
-
Advantages of Material Deposition:
- Design Freedom: Enables the creation of complex and lightweight structures.
- Reduced Waste: Additive processes typically use only the material needed, minimizing waste.
- Cost-Effective for Low-Volume Production: Ideal for small batches or one-off parts without the need for expensive tooling.
- Customization: Allows for easy modification of designs to meet specific requirements.
-
Challenges and Considerations:
- Material Limitations: Not all materials are suitable for deposition, and some may require specialized equipment.
- Surface Finish: Parts may require post-processing to achieve the desired surface quality.
- Speed: Deposition processes can be slower than traditional manufacturing methods for large-scale production.
- Cost of Equipment: High initial investment in advanced deposition systems can be a barrier for some manufacturers.
-
Future Trends in Material Deposition:
- Multi-Material Deposition: Development of systems capable of depositing multiple materials in a single build, enabling hybrid components.
- Increased Automation: Integration of robotics and AI to enhance precision and efficiency.
- Sustainability: Focus on eco-friendly materials and processes to reduce environmental impact.
- Scalability: Advances in technology to make deposition processes more viable for large-scale production.
By understanding these key points, manufacturers and purchasers can make informed decisions about implementing material deposition techniques in their operations, leveraging its benefits while addressing its challenges.
Summary Table:
Aspect | Details |
---|---|
Definition | Adding material layer by layer to create parts or products. |
Techniques | Extrusion, Powder Bed Fusion, Directed Energy Deposition, Binder Jetting. |
Materials | Metals, Polymers, Ceramics, Composites. |
Applications | Rapid Prototyping, Custom Manufacturing, Repair, Complex Geometries. |
Advantages | Design Freedom, Reduced Waste, Cost-Effective for Low-Volume Production. |
Challenges | Material Limitations, Surface Finish, Speed, Equipment Cost. |
Future Trends | Multi-Material Deposition, Automation, Sustainability, Scalability. |
Ready to leverage material deposition for your manufacturing needs? Contact us today to get started!