Microwave Plasma Chemical Vapor Deposition (MPCVD) is an advanced technique used to deposit high-quality thin films and coatings, particularly diamond films, on various substrates. It utilizes microwave energy to generate a plasma, which activates the precursor gases, leading to the deposition of materials at relatively low temperatures compared to other CVD methods. MPCVD is widely used in industries such as semiconductors, optics, and tool coatings due to its ability to produce uniform, high-purity, and defect-free films. The mpcvd machine is the core equipment in this process, enabling precise control over deposition parameters and ensuring consistent results.
Key Points Explained:
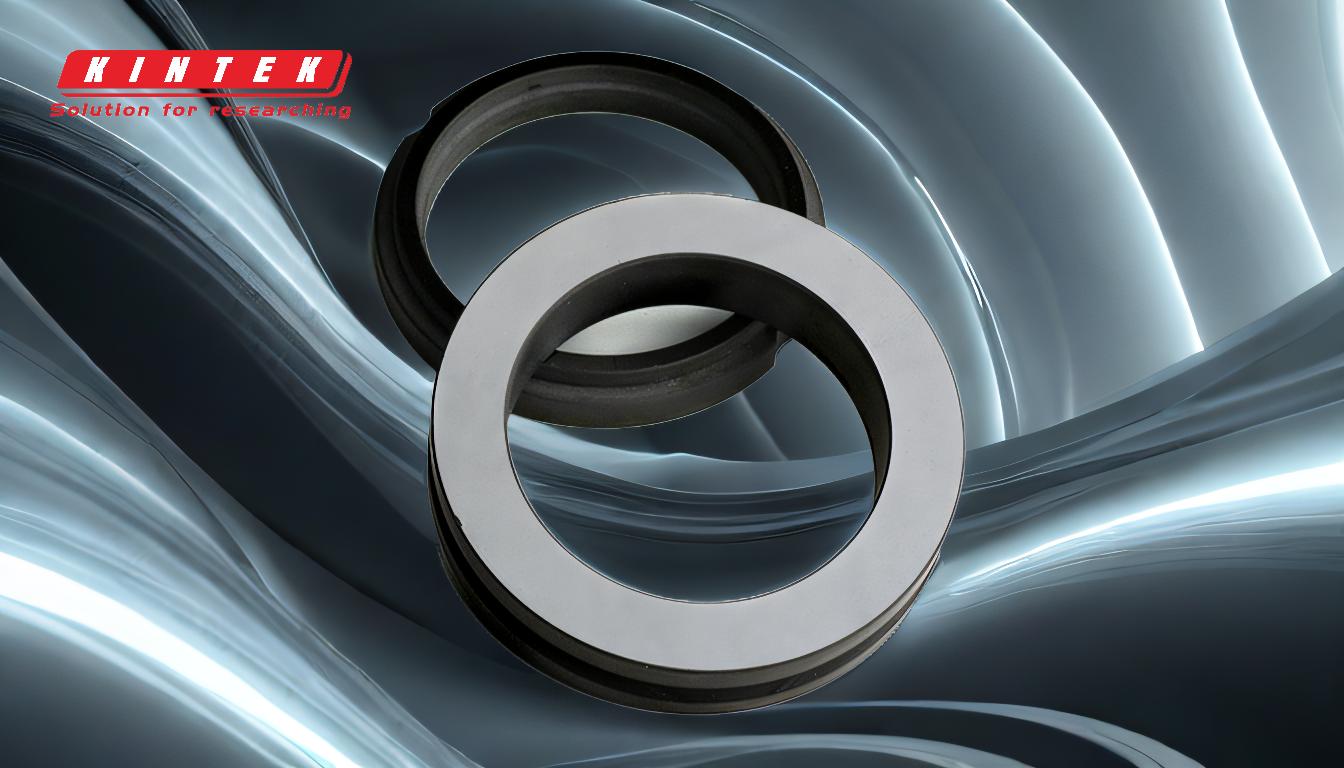
-
What is MPCVD?
- MPCVD stands for Microwave Plasma Chemical Vapor Deposition. It is a specialized form of CVD that uses microwave energy to create a plasma, which ionizes and activates precursor gases for thin film deposition. This method is particularly effective for producing high-quality diamond films and other advanced materials.
-
How does MPCVD work?
- The process begins with the introduction of precursor gases, such as methane and hydrogen, into a vacuum chamber. Microwave energy is then applied to generate a plasma, which dissociates the gases into reactive species. These species deposit onto a substrate, forming a thin film. The mpcvd machine controls critical parameters like gas flow, pressure, temperature, and microwave power to ensure optimal deposition conditions.
-
Advantages of MPCVD:
- High-Quality Films: MPCVD produces films with exceptional purity, uniformity, and minimal defects, making it ideal for applications requiring precision.
- Low-Temperature Deposition: Unlike other CVD methods, MPCVD operates at relatively low temperatures, reducing the risk of substrate damage.
- Versatility: It can deposit a wide range of materials, including diamond, silicon carbide, and other advanced coatings.
- Scalability: The process is scalable, making it suitable for both research and industrial applications.
-
Applications of MPCVD:
- Semiconductors: MPCVD is used to deposit diamond films for heat sinks and electronic components.
- Optics: It produces coatings for lenses, mirrors, and other optical components to enhance durability and performance.
- Tool Coatings: Diamond coatings deposited via MPCVD improve the wear resistance and lifespan of cutting tools.
- Research: MPCVD is widely used in material science research to explore new materials and deposition techniques.
-
Key Components of an MPCVD Machine:
- Microwave Generator: Provides the energy needed to create plasma.
- Vacuum Chamber: Maintains a controlled environment for deposition.
- Gas Delivery System: Regulates the flow of precursor gases.
- Substrate Holder: Positions and heats the substrate for uniform deposition.
- Control System: Manages process parameters to ensure consistency and quality.
-
Challenges and Considerations:
- Cost: MPCVD machines are expensive due to their advanced technology and precision components.
- Maintenance: Regular maintenance is required to ensure optimal performance and longevity.
- Process Optimization: Achieving the desired film properties often requires fine-tuning of parameters, which can be time-consuming.
-
Future Trends in MPCVD:
- Automation: Increasing automation in mpcvd machines to improve efficiency and reduce human error.
- New Materials: Expanding the range of materials that can be deposited using MPCVD, such as graphene and other 2D materials.
- Energy Efficiency: Developing more energy-efficient systems to reduce operational costs and environmental impact.
In conclusion, MPCVD is a powerful and versatile technique for depositing high-quality thin films, with the mpcvd machine playing a central role in enabling precise and consistent results. Its applications span across various industries, and ongoing advancements continue to enhance its capabilities and efficiency.
Summary Table:
Aspect | Details |
---|---|
Definition | MPCVD uses microwave energy to create plasma for thin film deposition. |
Key Advantages | High-quality films, low-temperature deposition, versatility, scalability. |
Applications | Semiconductors, optics, tool coatings, research. |
Key Components | Microwave generator, vacuum chamber, gas delivery system, substrate holder. |
Challenges | High cost, maintenance, process optimization. |
Future Trends | Automation, new materials, energy efficiency. |
Ready to explore how MPCVD can revolutionize your thin film processes? Contact us today for expert guidance!