Plasma-Enhanced Chemical Vapor Deposition (PECVD) is a versatile and widely used technique for depositing thin films of various materials on substrates. It is particularly valuable in the semiconductor, solar cell, and microelectronics industries due to its ability to operate at relatively low temperatures compared to other chemical vapor deposition (CVD) methods. PECVD involves introducing precursor gases into a vacuum chamber, igniting a plasma using a high-frequency electrical discharge, and using the resulting reactive species to deposit thin films on a substrate. This process is used for applications such as forming protective and insulating layers in integrated circuits, producing thin-film transistors for displays, and creating wear-resistant coatings.
Key Points Explained:
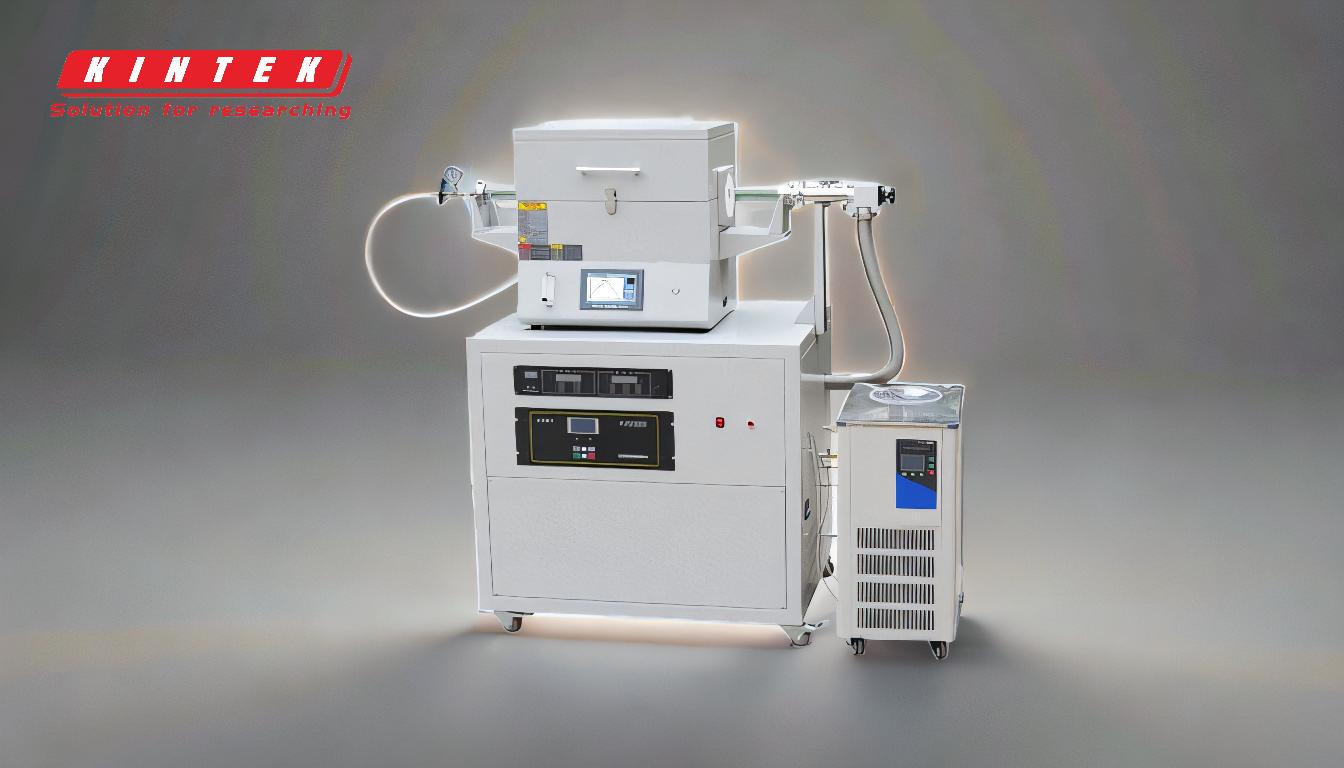
-
What is PECVD?
- PECVD is a thin-film deposition technique that uses plasma to enhance chemical reactions for material deposition.
- It operates at lower temperatures (250°C–350°C) compared to traditional CVD, making it suitable for temperature-sensitive substrates.
- The process involves introducing precursor gases (e.g., silane, ammonia) into a vacuum chamber and igniting a plasma using a high-frequency electrical discharge.
-
How Does PECVD Work?
- The substrate is placed in a deposition chamber between two electrodes: a ground electrode and a radio frequency (RF) excitation electrode.
- Precursor gases are mixed with inert gases and introduced into the chamber.
- Plasma is generated by an electrical discharge, creating a reactive environment that drives chemical reactions to deposit thin films on the substrate.
-
Applications of PECVD:
-
Semiconductor Industry:
- Used for depositing silicon nitride (SiN) and silicon oxide (SiOx) films as protective and insulating layers in integrated circuits.
- Enables the production of thin-film transistors (TFTs) for active matrix LCD displays.
-
Solar Cell Manufacturing:
- Used to deposit amorphous silicon (a-Si:H) and other materials for solar cells.
-
Optoelectronics and MEMS:
- Applied in the production of anti-reflective coatings, wear-resistant films (e.g., TiC), and barrier layers (e.g., aluminum oxide).
-
Decorative and Mechanical Coatings:
- Used to produce diamond-like carbon (DLC) films for mechanical performance and decorative purposes.
-
Semiconductor Industry:
-
Advantages of PECVD:
-
Lower Temperature Requirements:
- Suitable for substrates that cannot withstand high temperatures, such as glass or polymers.
-
Uniform Film Deposition:
- Produces films with excellent uniformity and surface quality.
-
Versatility:
- Can deposit a wide range of materials, including insulators, semiconductors, and protective coatings.
-
Lower Temperature Requirements:
-
Materials Deposited by PECVD:
- Silicon nitride (SiN) and silicon oxide (SiOx) for insulation and passivation in semiconductors.
- Amorphous silicon (a-Si:H) for solar cells and thin-film transistors.
- Diamond-like carbon (DLC) for wear-resistant and decorative coatings.
- Titanium carbide (TiC) and aluminum oxide (Al2O3) for barrier and protective layers.
-
Comparison with Other CVD Techniques:
- PECVD operates at lower temperatures than thermal CVD, making it more suitable for delicate substrates.
- It provides better film uniformity and surface quality compared to some other CVD methods.
- The use of plasma allows for faster deposition rates and enhanced control over film properties.
-
Key Components of a PECVD System:
- Vacuum Chamber: Maintains a controlled environment for deposition.
- Electrodes: Generate the plasma through an RF electrical discharge.
- Gas Delivery System: Introduces precursor and inert gases into the chamber.
- Substrate Heater: Heats the substrate to the required temperature (250°C–350°C).
-
Future Trends in PECVD:
- Development of new plasma sources (e.g., ECR plasma) for improved film quality and deposition rates.
- Expansion into emerging fields such as flexible electronics and advanced optoelectronic devices.
- Integration with other deposition techniques for hybrid fabrication processes.
By leveraging the unique capabilities of PECVD, industries can achieve high-quality thin-film deposition for a wide range of applications, ensuring enhanced performance and durability of electronic and optoelectronic devices.
Summary Table:
Aspect | Details |
---|---|
Temperature Range | 250°C–350°C, ideal for temperature-sensitive substrates |
Key Applications | Semiconductors, solar cells, optoelectronics, MEMS, decorative coatings |
Advantages | Low-temperature operation, uniform film deposition, material versatility |
Materials Deposited | SiN, SiOx, a-Si:H, DLC, TiC, Al2O3 |
Comparison to CVD | Lower temperatures, better uniformity, faster deposition rates |
Discover how PECVD can elevate your thin-film processes—contact our experts today!