Physical Chemical Vapor Deposition (PVD/CVD) is a process used to deposit thin films of materials onto a substrate through either physical or chemical reactions. Physical Vapor Deposition (PVD) involves the physical transfer of material from a source to the substrate, typically through processes like sputtering or evaporation. Chemical Vapor Deposition (CVD), on the other hand, involves chemical reactions in the vapor phase to produce a solid film on a heated substrate. Both methods are widely used in industries such as semiconductor manufacturing, coatings, and nanotechnology due to their ability to produce high-quality, uniform thin films.
Key Points Explained:
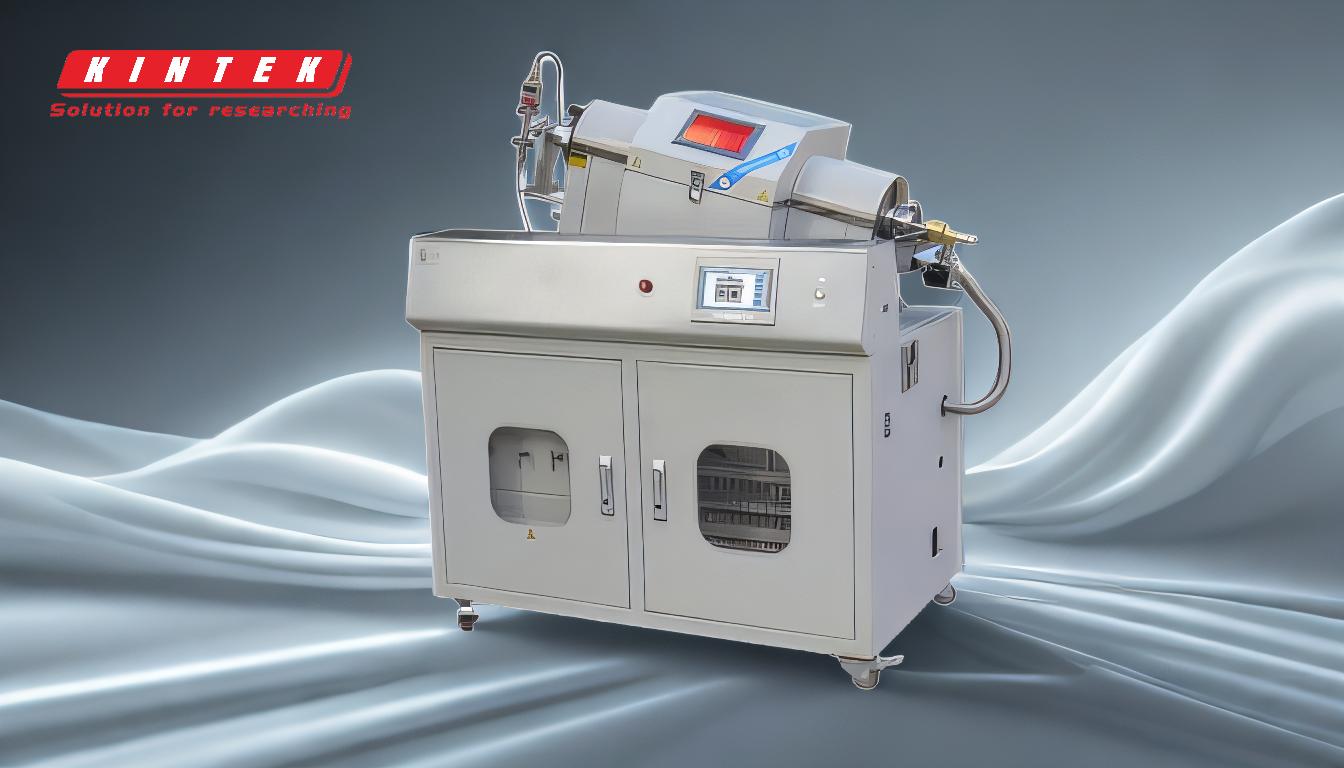
-
Definition of Physical Chemical Vapor Deposition (PVD/CVD):
- PVD involves the physical transfer of material from a source to a substrate, often using techniques like sputtering or evaporation. The material is vaporized in a vacuum and then condenses on the substrate to form a thin film.
- CVD involves chemical reactions in the vapor phase that result in the deposition of a solid film on a heated substrate. The process relies on the chemical reaction between gaseous precursors and the substrate surface.
-
Process Overview:
-
PVD Process:
- The source material is vaporized in a high vacuum environment.
- The vaporized material then travels through the vacuum and condenses on the substrate, forming a thin film.
- Common PVD techniques include sputtering (where atoms are ejected from a target material due to bombardment by energetic particles) and evaporation (where the source material is heated until it vaporizes).
-
CVD Process:
- Gaseous precursors are introduced into a reaction chamber.
- These precursors undergo chemical reactions on the heated substrate surface, leading to the formation of a solid film.
- The process involves several steps: transport of reacting gaseous species to the surface, adsorption of the species on the surface, surface-catalyzed reactions, surface diffusion, nucleation and growth of the film, and desorption of gaseous reaction products.
-
PVD Process:
-
Types of CVD:
- Aerosol-Assisted CVD: This method uses aerosol to deliver the precursor to the substrate. The aerosol is typically generated from a liquid precursor and is transported to the substrate where it reacts to form the film.
- Direct Liquid Injection CVD: In this method, a liquid precursor is directly injected into a heated chamber. The liquid is vaporized and then reacts on the substrate surface.
- Plasma-Based CVD: Instead of using heat, this method uses plasma to initiate the chemical reactions. The plasma provides the necessary energy to break down the precursors and facilitate the deposition process.
-
Advantages of PVD and CVD:
-
PVD Advantages:
- High purity of the deposited films.
- Ability to deposit a wide range of materials, including metals, alloys, and ceramics.
- Excellent adhesion of the films to the substrate.
-
CVD Advantages:
- Ability to deposit films with complex compositions and structures.
- High-quality, uniform films with excellent step coverage.
- Suitable for depositing materials that are difficult to deposit using PVD, such as certain ceramics and semiconductors.
-
PVD Advantages:
-
Applications:
-
PVD Applications:
- Used in the production of thin-film solar cells, optical coatings, and decorative coatings.
- Commonly used in the semiconductor industry for depositing metal layers and diffusion barriers.
-
CVD Applications:
- Widely used in the semiconductor industry for depositing silicon dioxide, silicon nitride, and other dielectric materials.
- Used in the production of hard coatings for cutting tools, as well as in the fabrication of carbon nanotubes and graphene.
-
PVD Applications:
-
Equipment and Facilities:
- Both PVD and CVD processes require sophisticated equipment and cleanroom facilities to ensure the quality and purity of the deposited films.
- The equipment typically includes vacuum chambers, heating elements, gas delivery systems, and control systems to monitor and regulate the deposition process.
In summary, Physical Chemical Vapor Deposition encompasses both PVD and CVD techniques, each with its own set of processes, advantages, and applications. These methods are essential in modern manufacturing and technology, providing the means to create high-quality thin films for a wide range of industries.
Summary Table:
Aspect | PVD | CVD |
---|---|---|
Process | Physical transfer of material (e.g., sputtering, evaporation) | Chemical reactions in vapor phase to deposit solid films |
Advantages | High purity, wide material range, excellent adhesion | Complex compositions, uniform films, step coverage |
Applications | Thin-film solar cells, optical coatings, semiconductor metal layers | Semiconductor dielectrics, hard coatings, carbon nanotubes, graphene |
Equipment | Vacuum chambers, heating elements, gas delivery systems | Reaction chambers, plasma systems, aerosol delivery systems |
Discover how PVD and CVD can enhance your manufacturing process—contact us today for expert advice!