Physical vapor deposition (PVD) is a coating process widely used in the watchmaking industry to enhance the durability, aesthetics, and functionality of watch components. PVD involves the deposition of thin layers of material, such as titanium nitride or zirconium nitride, onto the surface of watch parts in a vacuum environment. This process creates a hard, wear-resistant, and corrosion-resistant coating that can also provide unique colors like gold, black, or rose gold. PVD coatings are commonly applied to watch cases, bracelets, and bezels, offering both protective and decorative benefits. The process is highly precise and environmentally friendly, making it a preferred choice for luxury and high-performance watches.
Key Points Explained:
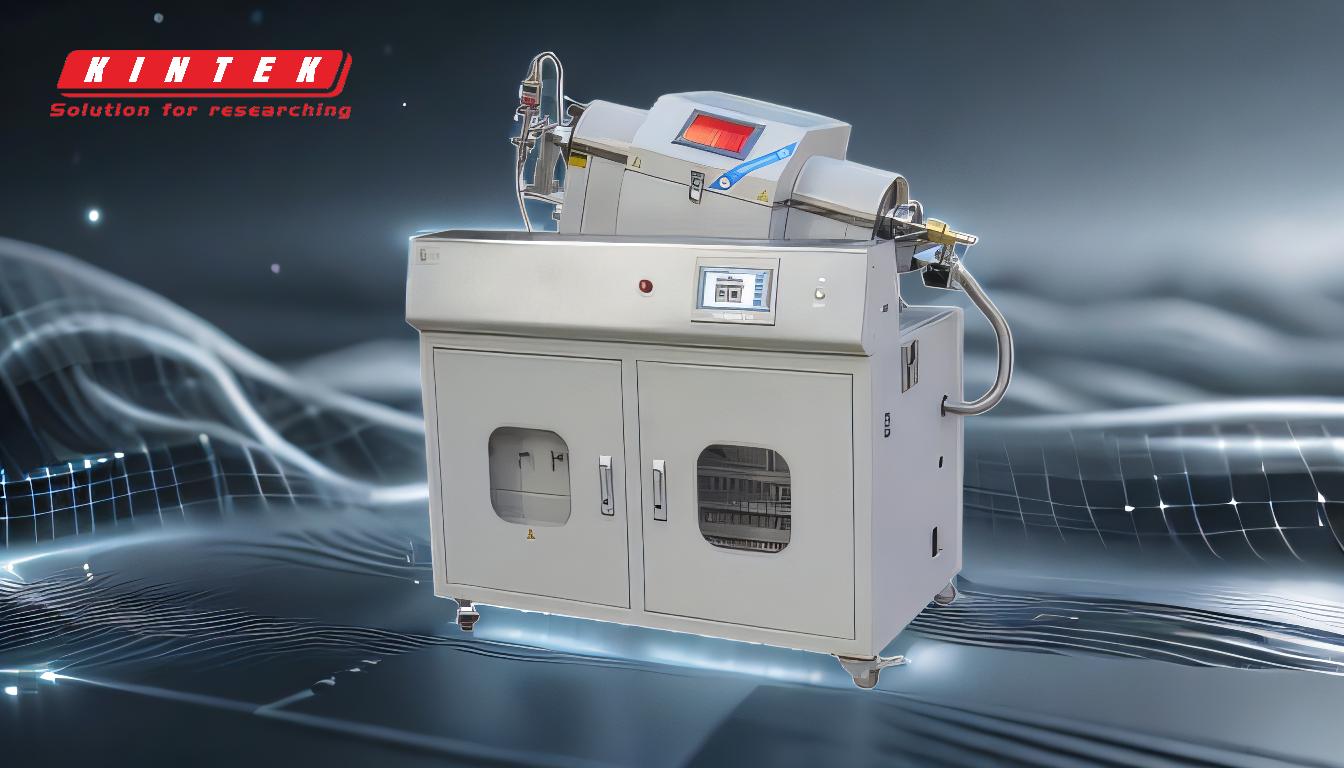
-
What is PVD?
- Physical vapor deposition (PVD) is a vacuum-based coating process where materials are vaporized and then deposited onto a substrate, such as watch components. This process creates a thin, uniform, and durable layer that enhances the surface properties of the material.
-
How PVD Works in Watchmaking:
- PVD involves several steps:
- Vacuum Creation: The watch components are placed in a vacuum chamber to eliminate contaminants and ensure a clean deposition environment.
- Vaporization: The coating material (e.g., titanium, zirconium) is vaporized using techniques like sputtering or evaporation.
- Deposition: The vaporized material condenses onto the watch components, forming a thin, even layer.
- Cooling: The coated components are cooled and removed from the chamber.
- PVD involves several steps:
-
Benefits of PVD in Watches:
- Durability: PVD coatings are highly resistant to wear, scratches, and corrosion, making them ideal for watch components exposed to daily wear and tear.
- Aesthetics: PVD allows for a variety of colors and finishes, such as gold, black, or rose gold, enhancing the visual appeal of watches.
- Functionality: The coatings can improve the performance of watch parts by reducing friction and increasing hardness.
- Environmental Friendliness: PVD is a clean process that produces minimal waste compared to traditional plating methods.
-
Applications in Watchmaking:
- PVD is commonly used for:
- Watch cases
- Bracelets
- Bezels
- Crowns and pushers
- It is particularly popular in luxury and sports watches, where both durability and aesthetics are critical.
- PVD is commonly used for:
-
Comparison with Other Coating Methods:
- PVD vs. CVD (Chemical Vapor Deposition): PVD operates at lower temperatures, making it suitable for materials that cannot withstand high heat. It also produces thinner and more precise coatings.
- PVD vs. Electroplating: PVD coatings are harder and more durable than electroplated coatings, which are prone to chipping and wear over time.
-
Limitations of PVD:
- Cost: PVD is more expensive than traditional coating methods due to the specialized equipment and vacuum environment required.
- Thickness: While PVD coatings are thin and precise, they may not be suitable for applications requiring thick protective layers.
- Color Limitations: Although PVD offers a range of colors, achieving certain shades can be challenging.
-
Future Trends in PVD for Watches:
- Advances in PVD technology are enabling even more durable and versatile coatings, such as diamond-like carbon (DLC) coatings, which offer superior hardness and scratch resistance.
- The use of PVD in smartwatches is growing, as it provides both aesthetic and functional benefits for wearable technology.
By understanding the principles and benefits of PVD, watchmakers and consumers can appreciate the value it adds to modern timepieces, combining advanced technology with timeless elegance.
Summary Table:
Aspect | Details |
---|---|
What is PVD? | Vacuum-based coating process for thin, durable layers on watch components. |
How PVD Works | Vacuum creation, vaporization, deposition, and cooling. |
Benefits | Durability, aesthetics, functionality, and environmental friendliness. |
Applications | Watch cases, bracelets, bezels, crowns, and pushers. |
Comparison | PVD vs. CVD: Lower temperatures, thinner coatings. |
Limitations | Higher cost, limited thickness, and color challenges. |
Future Trends | DLC coatings and growing use in smartwatches. |
Learn how PVD coatings can elevate your watch designs—contact our experts today for more information!