Physical vapor deposition (PVD) of thin films is a process that involves the physical transfer of material from a source to a substrate in a vacuum environment. This method is widely used to create thin, uniform coatings with specific properties such as hardness, corrosion resistance, and optical enhancement. PVD techniques, such as thermal evaporation and electron-beam evaporation, are employed in industries like electronics, optics, and solar energy. The process is environmentally friendly and produces high-quality coatings with excellent adhesion and durability.
Key Points Explained:
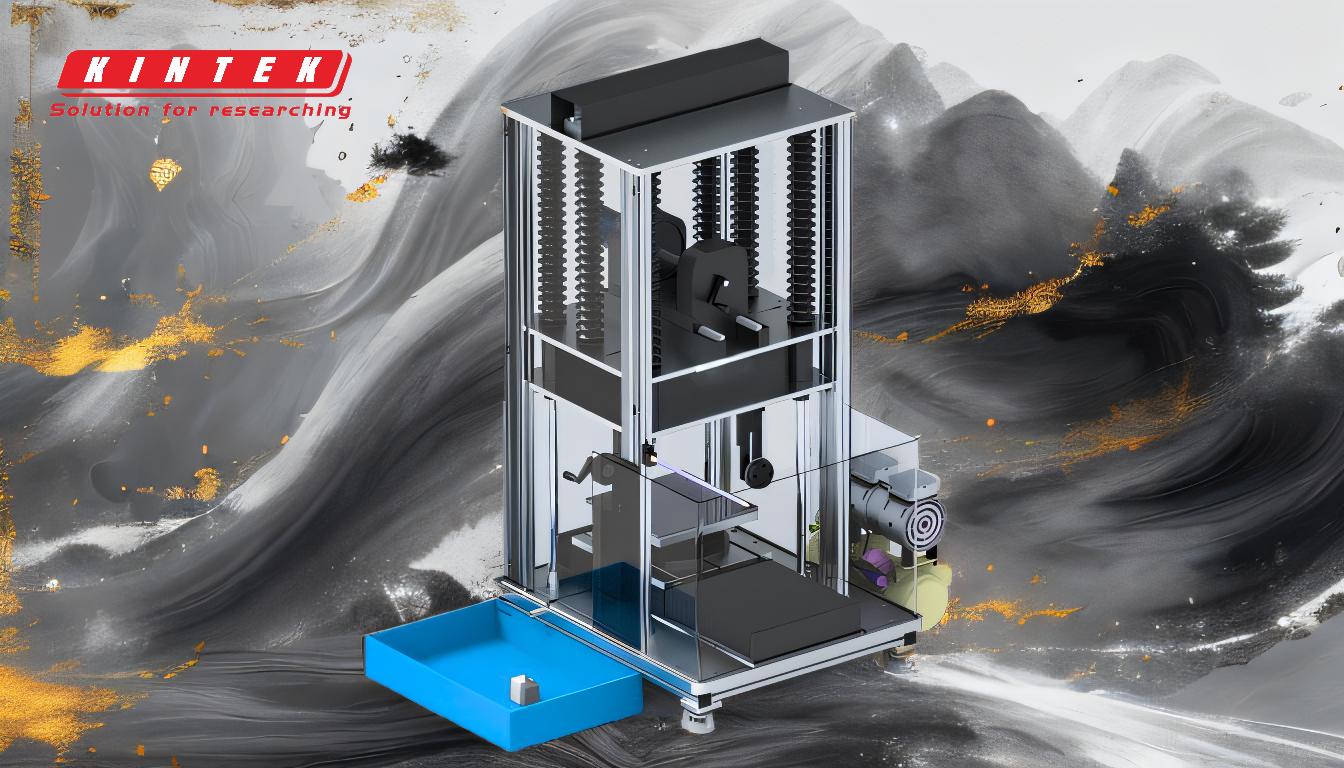
-
Definition and Overview of PVD:
- Physical vapor deposition (PVD) is a vacuum-based process where a solid material is vaporized and then deposited onto a substrate to form a thin film.
- This method is used to create coatings with specific functional properties, such as improved wear resistance, enhanced optical performance, or aesthetic upgrades.
-
Thermal Evaporation:
- Thermal evaporation is a common PVD technique where the target material is heated to its vaporization point using a tungsten filament or electron beam.
- The vaporized material travels through a vacuum and condenses on the substrate, forming a thin film.
- This method is ideal for depositing pure metals, oxides, and nitrides, making it suitable for applications like solar cells, OLED displays, and thin-film transistors.
-
Electron-Beam Evaporation:
- Electron-beam (e-beam) evaporation uses a focused electron beam to heat and vaporize the target material.
- The resulting vapor is deposited onto the substrate, creating a thin film with high precision and uniformity.
- This technique is particularly useful in the production of solar panels and glass coatings due to its ability to handle high-melting-point materials.
-
Vacuum Environment:
- PVD processes require a vacuum to ensure the purity and quality of the deposited film.
- The vacuum removes unwanted gases and contaminants, allowing the vaporized particles to travel directly to the substrate without interference.
- This results in coatings with excellent adhesion and minimal defects.
-
Advantages of PVD:
- PVD coatings are extremely hard, corrosion-resistant, and capable of withstanding high temperatures.
- The process is environmentally friendly, as it does not involve harmful chemicals or produce significant waste.
- PVD coatings are highly durable and provide superior ablation resistance, making them suitable for demanding applications.
-
Applications of PVD:
- PVD is widely used in industries such as electronics, optics, and renewable energy.
- Common applications include depositing conductive layers on solar cells, enhancing the durability of cutting tools, and improving the optical properties of lenses and displays.
-
Comparison with Other Methods:
- Unlike chemical vapor deposition (CVD), which relies on chemical reactions, PVD is a purely physical process.
- PVD offers better control over film thickness and composition, making it preferable for applications requiring precise and uniform coatings.
In summary, physical vapor deposition is a versatile and efficient method for producing high-quality thin films with tailored properties. Its ability to operate in a vacuum environment ensures clean and precise coatings, making it a preferred choice for a wide range of industrial applications.
Summary Table:
Aspect | Details |
---|---|
Definition | Vacuum-based process to deposit thin films with specific functional properties. |
Techniques | Thermal evaporation, electron-beam evaporation. |
Key Advantages | Hard, corrosion-resistant, durable, and environmentally friendly coatings. |
Applications | Electronics, optics, solar energy, cutting tools, and optical enhancements. |
Comparison with CVD | PVD is a physical process, offering better control over film properties. |
Interested in high-quality PVD coatings for your industry? Contact us today to learn more!